What Is Thermal Aging Test and the Function for PCB Assembly?
By:PCBBUY 01/07/2022 10:05
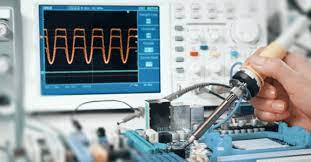
Thermal Aging Testing is performed to determine the operational life of the PCB board. It tests the capability of PCB components to withstand extreme temperatures for an extended period of time. The reliability of components placed on a printed circuit board decreases exponentially with time. This eventually results in the failure of the PCB due to differences in coefficients of thermal expansion (CTE) across the PCB material.
If you are curious about the professional information about thermal aging test in PCBA process, please check and read the content below in this passage.
Wanna know PCB knowledge? Check and read for more.
Why to process thermal aging test in PCBA?
The purpose of PCB aging tests is to gather data for assessing the long-term reliability of a PCBA that may be placed into continuous operation for over 100,000 hours (at least 20 years). These tests evaluate an entire PCBA, so they tell you the overall reliability of the bare circuit board, its components, solder and mechanical components, and any other materials used in the construction of the PCBA. Obviously, a PCBA cannot be tested for 20 years continuously, so test engineers will perform simulated life testing or other tests to evaluate long-term stability.
With performance requirements and fabrication requirements becoming more complex over time, so has the documentation process used by PCB manufacturers and design teams. With the right design software, a design team can quickly generate their test and fabrication data directly from their PCB layout. Important requirements like the reliability of solder joints, required PCB materials, use of conformal coatings, and a range of test methods can be specified within the project documents and easily shared with manufacturers.
What is the process of thermal aging test in PCBA?
Thermal aging applied to PCB assemblies or end-products is at changing temperatures for 250 hours in a temperature chamber, following the ECIA - EIA-364-17 standard - "TP-17B Temperature Life with or without Electrical Load Test Procedure for Electrical Connectors and Sockets".
The PCB assemblies are subjected to changes in air temperature in the thermal aging chamber with temperature elevates gradually to 105℃. Through the combined effects of high-and-low temperature changes and electric power, the defects of the assembled circuit board are exposed, such as poor welding, component parameter mismatch, temperature drift, and the faults caused during the debugging process. So we can eliminate the defects. Thermal aging also functions to stabilize the parameters of the non-defective circuit boards.
What are the main steps of thermal aging test in PCBA?
During PCBA production, aging test is necessary. The aging test generally simulates the external humid and high-temperature environment to test the PCBA finished product, so that the functional board is subjected to the change of air temperature in a thermal aging device with temperature changes, and through the combined effects of high temperature, low temperature, high and low-temperature changes, and electric power, Expose the defects of the functional board, such as poor welding, component parameter mismatch, temperature drift and failures caused during the debugging process, so as to eliminate it, and stabilize the parameters of the non-defective functional board. Because this situation has also occurred in electronic processing factories nowadays, PCBA boards are normal when shipped, but various defects appear after a short period of use, so in fact, it is necessary to conduct PCBA board aging tests.
1. Put the functional board at the ambient temperature into the heat aging equipment at the same temperature.
2. The PCBA board is in operation.
3. Then the temperature in the equipment should be reduced to the specified temperature value at a specified rate.
4. After the temperature in the equipment reaches a stable level, the PCBA board should be exposed to low temperature conditions for 2h.
5. Then the temperature inside the equipment should rise to the specified temperature at a specified rate.
6. After the temperature in the device reaches a stable level, the PCBA board should be exposed to high temperature for 2h.
7. Then the temperature inside the equipment should be reduced to room temperature at a prescribed rate.
8. Repeat 3 to 7 consecutively. Until the specified aging time, and the PCBA board is measured and recorded once according to the specified aging time.
Industry Category