What Is a BGA Chip during for PCB Designers in Industry?
By:PCBBUY 09/14/2022 14:05
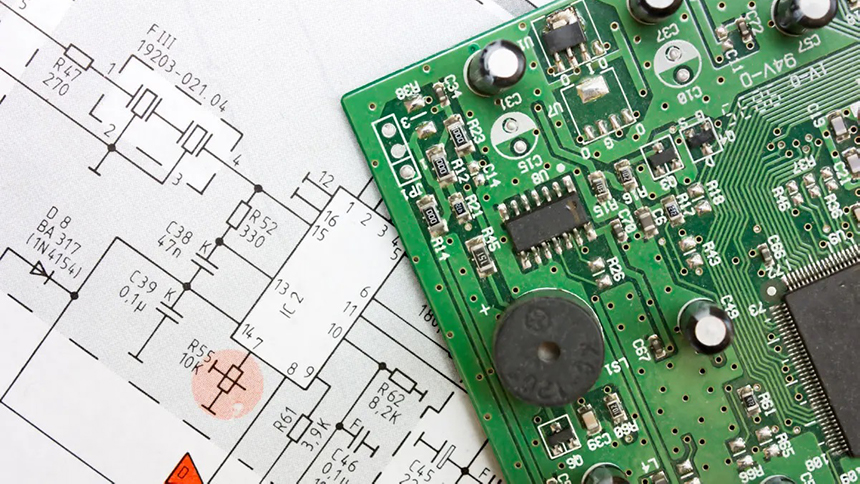
The BGA package began to make headlines as the next step in packaging technology. They offered higher interconnect density than both thru-hole PGA’s and surface-mount QFPs at comparable costs without the manufacturing problems associated with those packages.
If you are looking for more professional BGA chip during the PCB layout, please check and read the content in this passage.
What is the basic definition of BGA chip during the PCB layout?
BGA chips win over QFP (quad flat package) chips in terms of the shape of BGA packages. BGA packages make the physical size of chips dramatically reduced with solder ball array replacing peripheral leads at QFP chips, which is especially obvious when multiple I/O pins are available. The surface area of BGA linearly increases with the improvement of I/O pin count while that of QFP increases with the improvement of I/O pin count square. As a result, BGA package provides more manufacturability to components with multiple pins than QFP.
Generally speaking, I/O pin count ranges from 250 to 1089, which is specifically determined by packaging type and size. As far as manufacturability is concerned, BGA chips also perform better than QFP chips. The pins of BGA package chips are ball-shaped and are distributed in 2D array. Moreover, I/O pins feature larger pitch than QFP and perform as hard balls that won't be deformed due to contact. When it comes to chip manufacturers, another merit of BGA chips lies in its high yield. The assembly defect rate of BGA chips is normally at 0.3ppm to 5ppm per pin that can be regarded as equivalently no defect.
What are the classifications of BGA in PCB?
There are many types of BGA packaging, the general shape structure is square or rectangular. According to the arrangement mode of solder ball welding, it can be divided into peripheral type, staggered type and full array type BGA. According to the different substrates, it can be divided into 3 types as following:
· PBGA (Plastic Ball Grid Array)
· CBGA (Ceramics Ball Grid Array)
· TBGA (Tape Ball Grid Array)
What are the issues of processing BGA in PCB?
· Operators must wear electrostatic bracelets.
· Should adjust the airflow and pressure of the hot air gun in advance before desoldering BGA
· The temperature of the hot air gun should be well set in advance (generally controlled at 280~320℃) to prevent the chip from being damaged by excessively high temperature in the process of desoldering. It should not adjust the temperature again during desoldering.
· When desoldering BGA, gently touch the BGA with tweezers to confirm whether the solder on the pad melts away to prevent the BGA pad on the circuit board from being damaged.
· To avoid secondary ball soldering, the orientation marked on the PCBA , should be paid attention to when repairing the BGA.
How to process BGA soldering in PCB?
Dip a small amount of dense flux on the BGA tin balls and PCBA pads, retrieve the original mark and place the BGA. The BGA should be glued and positioned to prevent it from being blown away by hot wind. However, it should be noted that too much flux should not be put in. Otherwise, excessive bubbles of rosin will cause the chip to shift when heating. PCBA board also is fixed on the BGA rework platform and must be placed level, change the suitable nozzle, nozzle on the BGA chip and left 4 mm, choose BGA to rework stations primary set temperature curve, click on the screen of automatic soldering (note: will not apply pressure on BGA soldering process, easy to cause a short circuit between tin ball under the.)
With the melting of the BGA tin ball and the formation of the PCBA solder pad soldering, and through the surface tension of the tin ball, the chip will automatically center even if there is a deviation from the motherboard. When the BGA repair table is heated, the BGA soldering operation will be completed at this time. However, it should be noted that the BGA repair table will make an alarm sound after heating.
What is the importance of BGA in PCB?
BGA sockets are used for surface-mounting BGAs onto PCBs. BGA sockets help to mount the BGA chips onto PCBs without much hassle. The main problem of mounting an IC onto a PCB is that it can be very difficult to locate the pins of the IC on a PCB and solder them individually. Also, the mounting process can be very time consuming and frustrating if not done correctly. By using BGA sockets, these problems are solved. A BGA socket is made of plastic in the shape of a rectangle and has spaces on its underside to accommodate each solder ball of the BGA chip.
BGA sockets come in two types: active and passive. An active BGA socket has electrical contacts on its underside to which the solder balls of the BGA chip are connected. A passive BGA socket does not have any contact pads on its underside. Instead, it is connected to a PCB using through-holes or surface mount technology (SMT) components. In this article, we will only be looking at active BGA sockets.
BGA sockets are available in a variety of sizes depending on the size of the BGA chip that they are designed to accommodate. Some BGA sockets are designed to accommodate only one BGA chip, while others accommodate two or even four chips. The size of a BGA socket is usually specified in terms of the number of rows and columns on its underside. For example, if a BGA socket is designed to accommodate a 4×4-ball BGA chip, then it would have 16 contact pads arranged in 4 rows and 4 columns.
Industry Category