What Role Does PCB Copper Balance Play in PCB Manufacturing?
By:PCBBUY 10/28/2024 16:58
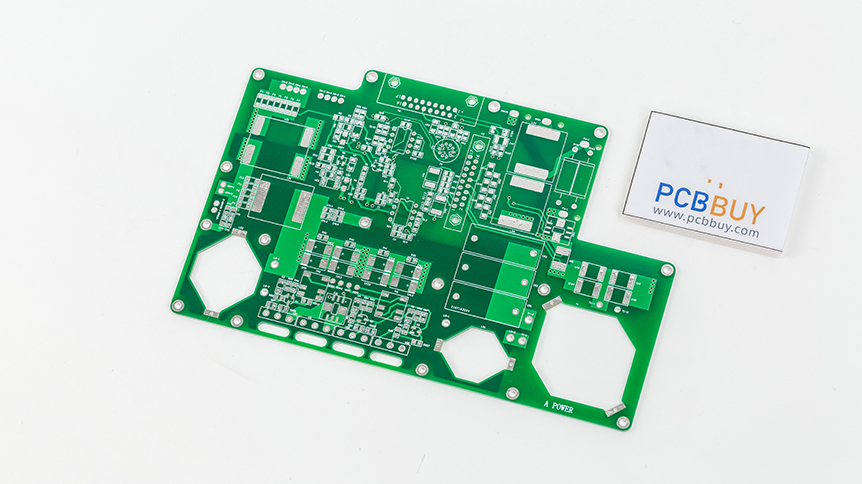
Printed Circuit Boards (PCBs) are fundamental components in modern electronics, serving as the backbone for most electronic devices. One of the critical aspects of PCB design and manufacturing is copper balance. This concept not only influences the electrical performance of the PCB but also affects its thermal characteristics, manufacturing yield, and overall reliability. In this article, we will explore the role of PCB copper balance in detail, discussing its principles, effects on performance, and the methodologies used to achieve optimal copper balance in PCB manufacturing.
How to Understand Copper Balance?
Copper balance refers to the distribution of copper within the PCB. This includes both the copper layers and the traces that connect various components. An imbalance can occur when there is a significant difference in copper thickness or area on opposite sides of the board. Such imbalances can lead to several issues, including warping, stress concentrations, and uneven thermal expansion.
What Are Principles of Copper Balance?
The balance of copper is primarily influenced by the following factors:
1. Copper Weight: The weight of copper used in PCB manufacturing is often measured in ounces per square foot (oz/ft²). Standard copper weights range from 1 oz/ft² to 2 oz/ft², depending on the application. A higher copper weight typically indicates a thicker copper layer, which can impact the board's thermal and electrical performance.
2. Layer Configuration: The arrangement of layers in a multilayer PCB affects the overall copper balance. Each layer's thickness and area should be considered to ensure that the overall board is balanced.
3. Trace Width and Spacing: The width and spacing of the traces also contribute to copper balance. Wider traces can carry more current but may also create imbalances if not designed properly.
4. Thermal Management: Thermal conductivity is affected by copper distribution. An unbalanced copper layer may lead to hot spots, adversely affecting component reliability.
What Is Importance of Copper Balance?
1. Mechanical Stability
One of the primary reasons to maintain copper balance is to ensure mechanical stability. An unbalanced PCB can warp during the manufacturing process, leading to difficulties in assembly and ultimately affecting performance.
Case Study: A study conducted by IPC (Institute of Printed Circuits) found that PCBs with a copper imbalance of more than 15% were prone to warping and dimensional changes during the soldering process.
2. Electrical Performance
Copper balance directly influences electrical performance. Uneven distribution can lead to differences in resistance and inductance, potentially causing signal integrity issues.
Research Data: A report by the International Journal of Electronics showed that PCBs with a balanced copper distribution had a 30% lower signal loss compared to those with significant imbalances.
3. Thermal Performance
Proper copper balance helps in effective heat dissipation. In high-power applications, uneven copper distribution can lead to thermal hotspots, which can cause components to fail.
Thermal Analysis: Using computational fluid dynamics (CFD), researchers have demonstrated that balanced copper distributions enhance thermal conductivity, reducing the maximum temperature rise in PCBs by up to 20%.
What Is Achieving Copper Balance in PCB Design?
Design Techniques
1. Layer Symmetry: Ensure that the design has symmetrical layers where possible. This can help minimize thermal and mechanical stresses.
2. Trace Design: Use wider traces for high-current paths and maintain uniform spacing to ensure that the copper distribution remains balanced.
3. Copper Fill: Incorporate copper fills in areas of the PCB that may require additional support or heat dissipation.
What Are Simulation and Modeling?
Utilizing software tools for simulation can help designers visualize the copper distribution across the PCB. Finite Element Analysis (FEA) can predict how changes in copper balance will affect the mechanical and thermal behavior of the PCB.
What Are Testing and Validation?
Once the PCB is manufactured, testing for copper balance is essential. Techniques such as:
X-ray Inspection: This non-destructive testing method helps identify copper distribution issues within multilayer boards.
Microsection Analysis: This method involves cutting the PCB to analyze the layer structure and copper distribution.
Conclusion
Copper balance is a crucial aspect of PCB manufacturing that directly affects mechanical stability, electrical performance, and thermal management. Achieving the right balance involves careful design, simulation, and validation processes. By understanding the principles and implications of copper balance, engineers can enhance the reliability and performance of PCBs, thereby contributing to the overall quality of electronic devices.
References
1. IPC. (2017). "IPC-2221: Generic Standard on Printed Board Design."
2. International Journal of Electronics. (2019). "Impact of Copper Balance on Signal Integrity in PCBs."
3. Computational Fluid Dynamics Research. (2020). "Thermal Analysis of PCB Copper Distribution."
Industry Category