What are the Applications of Heavy Copper PCB?
By:PCBBUY 08/26/2024 16:15
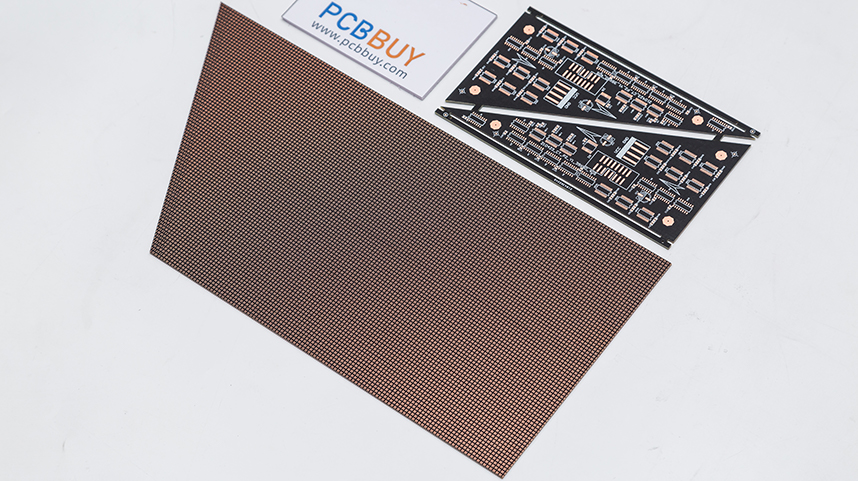
Heavy copper PCBs (Printed Circuit Boards), also known as thick copper PCBs, are specialized circuit boards that incorporate thicker copper layers compared to standard PCBs. These boards are widely used in applications that require higher current carrying capabilities, improved thermal management, and robust mechanical strength. The increased thickness of the copper layers, which typically ranges from 3 oz/ft² to over 10 oz/ft², makes heavy copper PCBs suitable for demanding applications such as power electronics, automotive, aerospace, and industrial systems. This article explores the various applications of heavy copper PCBs, supported by technical details, data, and industry-specific knowledge.
Understanding Heavy Copper PCBs
Heavy copper PCBs are characterized by the use of copper layers significantly thicker than those found in conventional PCBs. Standard PCBs generally have copper thicknesses of 1 oz/ft² (35 µm), while heavy copper PCBs can have thicknesses ranging from 3 oz/ft² (105 µm) to 20 oz/ft² (700 µm) or more. The key advantages of heavy copper PCBs include:
Enhanced Current Carrying Capacity: Thicker copper layers allow the PCB to handle higher currents without overheating or suffering from voltage drops.
Improved Thermal Management: The increased copper thickness facilitates better heat dissipation, reducing the thermal resistance of the PCB and helping to maintain optimal operating temperatures for components.
Increased Mechanical Strength: The robust copper layers provide mechanical durability, making the PCB more resistant to thermal cycling, physical stress, and vibration.
Table 1: Comparison of Standard and Heavy Copper PCBs
Feature |
Standard PCB (1 oz/ft²) |
Heavy Copper PCB (3 oz/ft² and above) |
Copper Thickness |
35 µm |
105 µm to 700 µm |
Current Carrying Capacity |
Low to moderate |
High |
Thermal Management |
Basic |
Advanced |
Mechanical Strength |
Standard |
Enhanced |
Applications in Power Electronics
Heavy copper PCBs are extensively used in power electronics due to their ability to handle high currents and dissipate heat effectively. Power electronics involve the conversion and control of electrical power using devices like rectifiers, inverters, and power regulators, which often generate substantial heat.
Key Applications in Power Electronics:
Power Supplies: Heavy copper PCBs are used in high-power supply units for servers, telecommunications, and industrial equipment. They ensure reliable operation by managing high current flows and minimizing overheating.
Motor Drives: Industrial motor drives require robust PCBs to handle high power levels. Heavy copper PCBs provide the necessary current handling capacity and thermal management, ensuring efficient motor control and operation.
DC-DC Converters: These converters are widely used in renewable energy systems and electric vehicles. Heavy copper PCBs allow for efficient conversion of DC power, supporting high current loads and reducing power loss.
Equation 1: Current Carrying Capacity
The current carrying capacity of a copper trace can be estimated using the following formula:
Applications in Automotive Industry
The automotive industry is another sector where heavy copper PCBs find significant applications. Modern vehicles are equipped with numerous electronic systems that require reliable PCBs to manage high currents and withstand harsh environmental conditions.
Key Applications in Automotive:
Electric Vehicle (EV) Charging Stations: Heavy copper PCBs are used in EV charging stations to handle the high currents required for fast charging. They ensure safety and efficiency by managing power distribution effectively.
Powertrain Control Systems: In hybrid and electric vehicles, powertrain control systems require PCBs that can handle high currents and provide reliable thermal management. Heavy copper PCBs are ideal for these applications.
Advanced Driver Assistance Systems (ADAS): ADAS technologies, such as adaptive cruise control and collision avoidance systems, rely on heavy copper PCBs to ensure stable performance under high electrical loads.
Table 2: Heavy Copper PCB Specifications for Automotive Applications
Application |
ADAS Modules |
Current Rating |
Operating Temperature |
EV Charging Stations |
6 oz/ft² |
Up to 100 A |
-40°C to 85°C |
Powertrain Control Systems |
8 oz/ft² |
Up to 150 A |
-40°C to 125°C |
ADAS Modules |
4 oz/ft² |
Up to 50 A |
-40°C to 105°C |
Applications in Aerospace and Defense
The aerospace and defense industries require PCBs that can withstand extreme conditions, including high temperatures, mechanical stress, and exposure to harsh environments. Heavy copper PCBs meet these stringent requirements due to their robust construction.
Key Applications in Aerospace and Defense:
Power Distribution Units (PDUs): Heavy copper PCBs are used in PDUs for aircraft and military vehicles, where they handle high currents and provide reliable power distribution under challenging conditions.
Radar Systems: Radar and communication systems in military applications demand PCBs that can manage high power levels and dissipate heat efficiently. Heavy copper PCBs ensure stable performance and reliability.
Avionics: Avionics systems, which include navigation, communication, and control systems, rely on heavy copper PCBs for their durability and ability to handle high currents and thermal loads.
Equation 2: Heat Dissipation
The heat dissipation capacity of a heavy copper PCB can be estimated using the following formula:
Applications in Industrial Systems
Industrial applications often involve heavy machinery and equipment that operate under high power conditions. Heavy copper PCBs are essential in these environments to ensure the reliability and safety of electronic control systems.
Key Applications in Industrial Systems:
Power Inverters: Inverters used in industrial automation and renewable energy systems, such as solar inverters, require heavy copper PCBs to handle high currents and provide efficient power conversion.
Uninterruptible Power Supplies (UPS): Heavy copper PCBs are used in UPS systems to manage high current loads during power outages. They ensure continuous power supply to critical systems.
Welding Equipment: Industrial welding machines operate at high currents, requiring heavy copper PCBs to ensure stable performance and prevent overheating.
Table 3: Heavy Copper PCB Use Cases in Industrial Applications
Application |
Copper Thickness |
Current Handling |
Temperature Range |
Heat Dissipation |
Power Inverters |
10 oz/ft² |
200 A |
-20°C to 60°C |
High |
UPS Systems |
8 oz/ft² |
150 A |
0°C to 50°C |
Moderate |
Welding Equipment |
12 oz/ft² |
250 A |
250 A |
Very High |
Applications in Renewable Energy
The shift towards renewable energy sources has increased the demand for robust and reliable PCBs that can handle high power levels. Heavy copper PCBs play a critical role in various renewable energy applications, such as solar and wind power systems.
Solar Power Inverters: Heavy copper PCBs are used in solar inverters to manage the high currents generated by photovoltaic panels. They ensure efficient power conversion and distribution.
Wind Turbine Control Systems: The control systems of wind turbines require PCBs that can withstand high currents and harsh environmental conditions. Heavy copper PCBs provide the necessary durability and reliability.
Battery Management Systems (BMS): Heavy copper PCBs are used in BMS for energy storage systems, ensuring efficient power management and thermal control.
Design Considerations for Heavy Copper PCBs
Designing heavy copper PCBs involves several considerations to ensure optimal performance and reliability. Key design aspects include:
Trace Width and Spacing: Wider traces are required to handle high currents and reduce resistance. Proper spacing is essential to prevent electrical short circuits and ensure safety.
Thermal Management: Integrate thermal vias and heat sinks to enhance heat dissipation. The use of heavy copper layers inherently improves thermal management.
Material Selection: Use high-quality dielectric materials to withstand the increased thermal and mechanical stresses associated with heavy copper PCBs.
Equation 3: Trace Width Calculation
The trace width required for a specific current can be calculated using the IPC-2221 standard formula:
Conclusion
Heavy copper PCBs are critical components in various high-power and high-reliability applications. From power electronics and automotive systems to aerospace, industrial machinery, and renewable energy, heavy copper PCBs provide the necessary current handling, thermal management, and mechanical strength required in these demanding environments. By understanding the applications and design considerations of heavy copper PCBs, engineers and manufacturers can optimize their products for performance, reliability, and safety.
References
-
IPC-2152: Standard for Determining Current Carrying Capacity in Printed Board Design.
-
Wang, X., & Zhu, S. (2018). Design and Fabrication of Heavy Copper PCBs. Journal of Electronics Manufacturing.
-
Kim, D. Y., & Park, J. H. (2017). Thermal Management in Heavy Copper PCBs. IEEE Transactions on Components, Packaging, and Manufacturing Technology.
-
Lee, H. S., & Lee, M. (2019). Advancements in Heavy Copper PCB Technology. International Journal of Circuit Design and Technology.
-
IPC-2221B: Generic Standard on Printed Board Design.
Industry Category