What are the issues of PCB crosstalk?
By:PCBBUY 07/24/2023 16:02
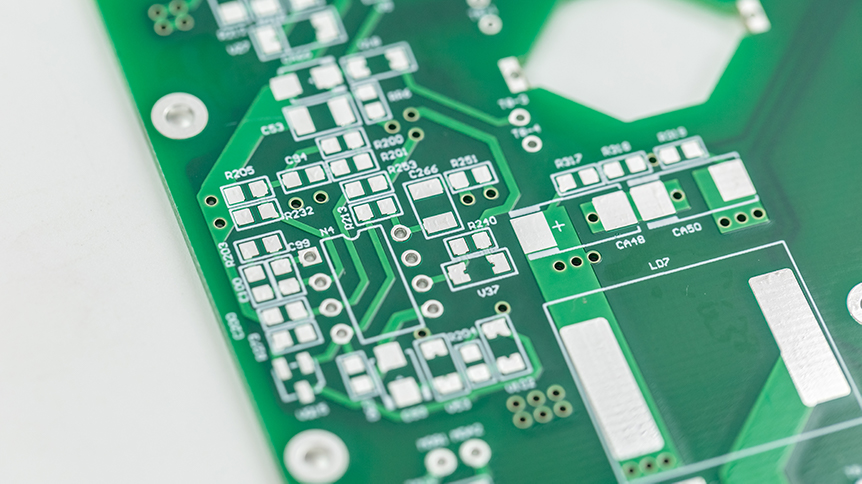
Crosstalk is generally specified as a percentage of the signal that appears on the victim line, relative to the aggressor line. It can also be expressed in terms of dB below the driven line level. NEXT varies with the frequency of the transmission since higher frequencies create more interference.
Do you know the basic information of crosstalk in PCB design? If you are searching more information about crosstalk in PCB design, please check and read the content below for more professional knowledge.
What are the causes of crosstalk?
· Capacitive and inductive coupling: Capacitive coupling is due to parasitic capacitance and inductive coupling occurs due to mutual inductance.
· Difference in propagation velocity: It can be avoided by trace length matching and propagation delay matching.
· PCB vias: PCB vias with stubs create reflections, thus ringing which generates crosstalk. One way to avoid this is to back drill the vias.
· Increased data rates: With increased data rate, the rise time increases as well. According to Faraday’s law, with an increase in rise time, the crosstalk will also increase. One way to reduce crosstalk between such signals is to increase the spacing between the traces.
· Board size: As the PCB board size increases, the trace lengths also increase, and these traces behave as antennas. So, it is important to keep the trace lengths as minimum as possible.
What are the issues of PCB crosstalk?
Too much activity in a circuit board can make the transmission of a signal difficult. Think of two traces on a circuit board running together side-by-side. If the signal of one trace is “louder” with more amplitude than the signal of the other, it could over-power that other trace. And just as it can be difficult in a noisy room to keep your own thoughts straight when trying to speak, the “victim” trace on a PCB will be similarly influenced by the louder signal. The problem then is that the victim signal will start behaving like the aggressor signal instead of behaving the way that it is supposed to.
Crosstalk is defined as the unintentional electromagnetic coupling between traces on a printed circuit board. The overpowering of one signal in a trace by another one is the result of this coupling even though the two traces are not in physical contact with each other. This can happen on a PCB that has acceptable trace spacing for manufacturing but where the spacing is not acceptable for crosstalk.
In addition to the potential for crosstalk between two traces that are side-by-side on the same layer, there is an even greater risk for traces that are running parallel to each other vertically between two layers. This effect is known as broadside coupling and happens because the two signal layers are separated by only a very small thickness of core material. This distance is often less than the spacing between two traces on the same layer.
How is PCB crosstalk minimized?
· Make use of segregated transmission lines: Crosstalk is induced by the aggressor trace onto the victim trace, so it is obvious that a higher aggressor voltage will induce more crosstalk. Therefore, it is best to segregate groups of nets according to their signal amplitude. This strategy prevents larger voltage nets (3.3V) from affecting smaller voltage nets (1.5V).
· Implement back drilled vias: Via stubs decrease signal integrity, hence an increase in crosstalk. This can be reduced by implementing back drilling.
· Reduce parallel trace runs: Longer trace runs (more than 500mils) increase the mutual inductance hence crosstalk.
· Maintain adequate separation between the traces: Provide adequate separation between traces (adopt 3W rule). If adequate separation is not maintained, then it will increase the mutual capacitance (Cm). The 3W rule reduces the crosstalk by 70%. To achieve 98% crosstalk reduction, go for 10W.
· Use guard traces: Guard traces are used to control capacitive crosstalk between transmission lines. Such traces should be used wisely as they make routing difficult.
· Adopt orthogonal routing: Route adjacent signal layers orthogonally to minimize capacitive coupling between them.
· Do not decrease the signal rise time: Decreased signal rise time increases the crosstalk.
· Opt for differential pair routing: Tightly coupled differential routing eliminates crosstalk because the noise from the aggressor is coupled equally into both branches of the differential pair, producing common-mode noise. Differential pairs reject the common mode noise that helps with crosstalk reduction.
· Terminate even and odd mode transmission properly: A three resistor network (T termination) can be used to terminate the odd and even mode.
Industry Category