What is Alignment and Balancing in PCB Assembly for Manufacturers?
By:PCBBUY 11/23/2021 09:42
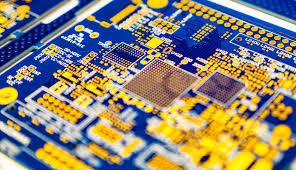
This alignment procedure allows for a more efficient Automated Assembly Process via Pick & Place machines, and the same benefits are observed in Solder Mask application. If the actuator does not have to spend much time moving between areas on the PCB, the process takes place more quickly, and the lead time for your project is effectively reduced. This becomes particularly important for larger orders such as Mid-Volume Production runs. Even small groups of similar components yields considerable advantage in this respect, compared to a design with similar components scattered across the PCB.
Do you know the methods to choose proper alignment in PCB assembly process? In this passage, we are going to tell you all the details and information about alignment in PCB assembly, if you are curious about it please check and read the content below.
Why alignments affect PCB design?
The entire EAGLE community has been shouting from the rooftops to give you alignment tools, and we’ve been listening. After all, there’s nothing enjoyable about squinting to count grid points while you line up that row of SMD resistors or vias. The new alignment tools in Autodesk EAGLE includes everything you might expect:
· Align a set of objects by their top, bottom, left, right, or center origins.
· Evenly space grouped objects based on horizontal or vertical distributions.
· Align new design blocks or library parts to your grid settings with grid alignment.
Now, while all of these alignment tools will surely make your life easier at design time, they even have an impact down the road during manufacturing. It’s more than just making your board beautiful; alignment tools can help with。
How to determine the right alignment for PCB?
The gains made in the foundries end up carrying over to the printed circuit board so we also have to get better with each generation. Etch processes give way to additive processes in order to get down to the 25 micron trace/space realm. That might be enough - for now.
Meanwhile, the PCB stack-up has to accommodate the increased circuit density one way or another; more traces per layer or more layers overall. Either way, the precision of the layer-to-layer alignment is tightening up on a regular basis. We’re likely to see a greater use of lasers and other means, such as MSAP, to get reliable results at this scale.
The best alignment method for PCB fabrication is still the humble tooling hole. This is a set of non-plated holes with precisely defined locations and even more precise diameter tolerances. They are always non-plated because the plating process is too imprecise for repeatable fixturing. These holes key the board or panel to a matching set of pins on a fixture or, I should say fixtures.
These precision holes in the bare board will be used to align the layers during the initial lamination and any subsequent lamination cycles. After the press, the board will be placed in another jig for application of soldermask and silkscreen. Yet another fixture will use them for electrical probing to find opens and shorts. Good panels will then be put on a robotic assembly line and then on to a soldering machine using the same holes. There may be some additional testing and automatic optical inspection (AOI) that follows.
What are the challenges of alignment and components for PCB?
Increased density, shrinking footprints, higher data rates, and thermal management are but a few of the challenges affecting the design and fabrication of printed circuit boards (PCBs) in today’s electronic systems. And did I mention cost?
An important, although sometimes overlooked consideration, is these increasingly sophisticated PCBs often require more complex connector systems. Most of the aforementioned design factors also affect connector design and performance, including smaller footprints, diminishing profiles, and the need for increased reliability. And did I mention cost? These strict connector design parameters can create conflicting goals for connector manufacturers, namely balancing the need for increased performance and density while managing costs.
One of the most common connector-related challenges – one that is often not considered until it raises its potentially ugly head – is aligning multiple connector sets between two mated PCBs.
This is a common point of discussion for Samtec Product Engineering and the Interconnect Processing Group (IPG)(1). They have worked with countless Design and Process Engineers on this issue. I spoke with Kevin Meredith, Product Engineer at Samtec, about the challenges of aligning multiple connector sets between two PCBs
How to process alignment and components for PCB with tools?
Back in the good old days, there was one size for tooling holes, 125 mils with a plus/minus tolerance of one mil. Now, there is an 89 mil hole too because everything in this game shrinks over time. Unilateral tolerances are often applied where the pin will be the nominal value with a plus tolerance but no negative tolerance. The hole then gets zero oversize and a small negative tolerance. The actual numbers come down to what the fab shop can do on a best-effort basis. It’s almost an interference fit but not quite.
The smaller boards that you’d find in a smartwatch or similar device do not have room for tooling holes on the board so the holes become a standard part of the assembly sub-panel. The sub-panel is maintained through fab, assembly and test and only broken down once the boards are known to be working up to the standard requirements.
Ok, we’re set up for component placement on the assembly line. But we aren’t. The pick and place machine has a camera that can find a specific set of features on the board. These features are called fiducial marks and they help the robotic arm calibrate on the exact location of the components.
Industry Category