BOM in PCB
By:PCBBUY 06/11/2021 17:04
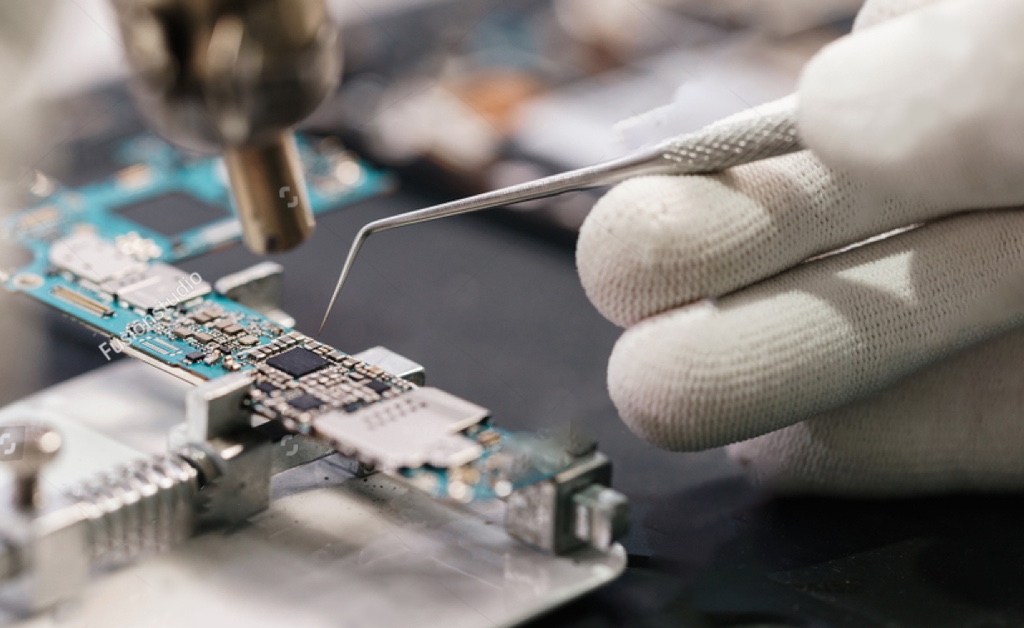
Electronic products are made up of numerous parts. This list of features needs to be created, checked, and even audited regularly if your organization is responsible for manufacturing and distributing any electronic product. It cannot be ignored. In a complete layperson's terms, the Bill of Materials (BOM) could be considered the "shopping list" of any given electronic product manufacturer.
The BOM should answer as many questions related to your electronic PCB product as possible, from what they are, how they should assemble, to what kind of staff, and how much team is necessary for the assembly.
Let's compare the tech industry to the service PCB industry. They essentially have their version of a BOM, which assists them when they need to order supplies or hire staff. It is no different when it comes to electronic product manufacturers. Although some of the items on their list may be different, it is still essential for them to create one.
How to create a BOM?
There are three questions you need to be asking yourself when creating a BOM for your next project: The "when," the "what," and the "how." After discussing these topics with your selected staff and the client who has assigned the project to your organization, you can then proceed with your project.
It would help if you thought of an electrical product project like the head chef of a restaurant feels when preparing their restaurant. There are more similarities between the two than you think.
Most restaurants need to answer these three questions quickly, accurately, and in the right order. If they do not (and most do not), they usually face dire consequences down the road.
It is what happens with smaller-scale restaurants. They approach these questions in an air of panic, not knowing what question to answer first and getting less than complete information on answering these questions. The larger chain restaurants have an established system of answering these questions.
The system in question is the same when it comes to electrical product projects. When you have been assigned an electrical product project, you are essentially preparing something, just like the head chef at a restaurant meets preparing food for diners. The only real difference here is that there is no real creative factor involved. There is no "menu creation" for an electrical product.
Why is BOM important?
Anything that involves electronic products requires a lot of organization and operations when it comes to any materials. The purpose of a BOM is to make sure that everything involved in an electronic product project is operating smoothly. When this process is not organized correctly, a lot of unsavory things can happen.
Costs
The creation of a proper BOM can reduce the costs involved in a project. Because there are many materials necessary when it comes to a project, much money goes into them. If a BOM is accurate and organized correctly, it can save a lot of money. One of the worst things that any manufacturer can do is rush to create a BOM. If the logistics list is in a hurry, two things can happen.
First, insufficient material is ordered, and it will cost more money to get more materials contained, especially if time is of the essence, and you need the materials delivered quickly.
The second thing that can happen is that you can get too many materials, it also means spending too much money. While it is true that you will possibly have surplus materials for the next project, the amount paid exceeds the necessary amount.
Staffing and Personnel
One thing related to cost is employees and people. Having staff to work on a project is something that should be directly determined by what is contained in the BOM. If you don't take the BOM seriously, it can affect employees to hire too many people. The staff members will not be compensated the way they like or also employ a few people, and their production will suffer from being overwhelmed and overworked.
How many levels of an ideal BOM?
There is no hard and fast answer to this, and it would be foolish to think that there is anything "ideal" when it comes to a BOM. From the standpoint of saving money, the ideal BOM only has one level; this way, fewer materials need to order, and there are not as many procedures involved.
From the standpoint of making sure that a project is significant, the ideal BOM has many levels. The more stories of a BOM have the more attention to detail involving the necessary assemblies. However, this could cost more than necessary.
Different projects demand different materials and other ways to assemble these materials. Because of this, we need to create a different BOM. Some of them only have one level, and some of them have multiple levels. There is no "ideal" BOM, not if you are interested in saving money.
There are a couple of things to consider when determining how many levels a BOM should have, and if you are interested in a successful project where costs are as low as possible, you will consider these
How involved are the parts?
Sometimes the parts involved in a BOM are complex and require a lot of different aspects to construct. It is the most common reason why there would be a need for a multi-level BOM. A multi-level BOM means that they can micromanage efficiently, and this can save money and time on some of the more complicated operations of a project since it is easier to detect things that go wrong.
If the parts involved in a project are not complicated, it would be a better idea to have a single level BOM since there would not be necessary to order smaller materials to assist in constructing the part.
Industry Category