Differential Pair in PCB Design
By:PCBBUY 09/06/2021 10:02
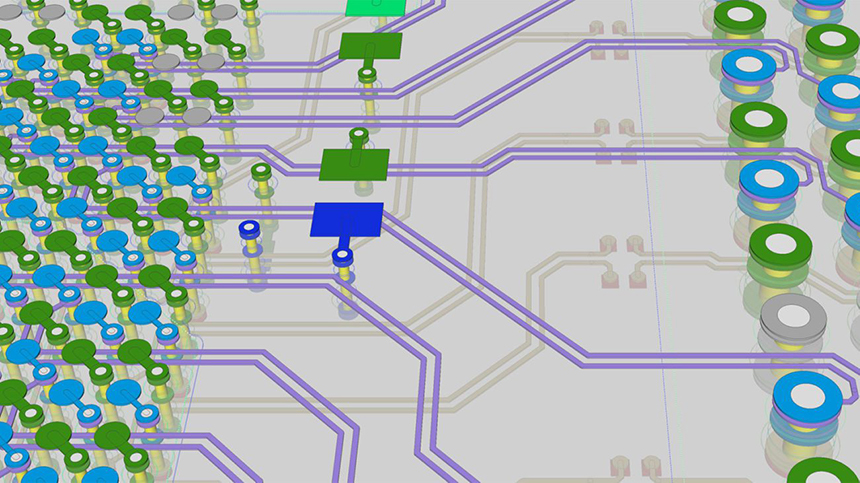
Before we can start routing the PCB, we need to define Design Rules for our differential traces. To get the correct parameters, we have to use the specifications from our PCB house and the provided calculator. This will give us the appropriate trace width and trace separation for the desired differential impedance. In this case, we want a single ended impedance of 50 Ohms and a differential line impedance of 100 Ohms.
In this passage, we will focus on the differential pair in PCB design. If you are going to learn more information, you can check and read the content below we prepare below.
What is the basic of differential pair in PCB design?
If differential pairs are so difficult to rout, then why invest the time and effort to use them? The answer is that differential pairs are naturally resistant to common mode noise, have little return through the grounding plane, minimize signal loss and increase the signal-to-noise ratio (SNR). They are also routed close together, meaning that outside noise shifts the signals in the pair by approximately the same amount, thereby increasing their noise rejection.
Furthermore, because current returns through one of the traces, very little actually flows through the ground plane to elsewhere in your system. This means that when routed correctly, differential pairs can cross analog/digital planes and power boundaries without causing too much EMI.
What are the advantages of differential pair in PCB design?
So why use differential pairs when we are so use to routing traces the good ol single ended mode fashion? Well when going high speed, all sorts of noise and electromagnetic interferences start to crop up in the circuit that degrades our signal. So basically we use this technique to for the following reasons:
· To minimize electronic crosstalk,
· Attenuate Electromagnetic Interference,
· Reduce both noise emission and noise acceptance,
· Improvement in Signal to Noise (S/N) ratios,
· Effective isolation from power systems,
· Low power requirement.
It is because of these awesome benefits that they are used in the popular and familiar communication protocols such as SATA, LVDS, PCI-E, DDR, 10gig Ethernet where the data-rates can range between 1.5Gbit/s to around 10 Gbit/s.
What are the factors of differential pair routing?
Fan-out and end routing
Let’s start at that differential driver on the left (Differential driver). Imagine the TRUE ( TRUE differential driver) and COMPLEMENT ( Differential driver COMPLEMENT) outputs are adjacent balls on a fine-pitch BGA, fanned-out to inner layers. Whatever else you do, keep the track lengths to fan-out vias equal, and then keep the lengths after those vias equal until you start the parallel track pattern. That parallel track pattern is the coupled section because there’s an electromagnetic coupling between the two sides.
Corner angles and curves
If you only want good signal integrity, make no corner tighter than 135°. Many device application notes tell you the same. That angle works well for 45° routing. You’ll hear that curves give you better signal integrity, but for most PCB tracks – even for very fast signaling – that isn’t true. Get curves wrong and you’ll make it a whole lot worse – and what “wrong” means isn’t always obvious.
Matching to other differential pairs
Add length in coupled sections only, and keep the pair coupled all the way because the differential impedance and delay-per-unit-length are different from the single-ended values – even within the same pair.
Matching between a differential pair and single-ended signals
In this case, you almost invariably need to add length to the pair, not the single-ended signal. As with matching between pairs, add length in coupled sections only. The application notes or standards docs will tell you how much.
What are the guidelines of PCB differential pair routing?
Route the different pairs together
The two traces of the pair need to be clearly identified as a diff pair for the layout team so that they are routed together across the entire length of the signal.
· Avoid using vias if possible. If you do use them, they should be placed in symmetrical pairs. Try to keep them as close together as possible and place the vias equally from the pads that they are routing from.
· Inner layer routing is preferable to minimize crosstalk, but that means transitioning through the layers with vias.
· Keep the diff pairs isolated from other traces. This is often done by specifying a clearance of three times the normal trace width spacing.
· If possible, consider broadside diff pair routing on adjacent signal layers. This will allow for higher routing density and better crosstalk control.
Keep the routing symmetrical between the two traces
A successful diff pair should result in the lines closely mirroring each other. To do that, consider these ideas as you route:
· Plan your routing to avoid obstacles such as vias or passive parts to maintain the symmetry of the pair (as shown in the picture above).
· Plan your pad entry and exit routing so that the traces mirror each other as closely as possible.
· Use the same trace widths throughout the length of the trace.
· Keep the spacing between the pair consistent.
Keep the trace lengths of the pair the same
As discussed previously, the lengths of the two lines in the pair must be the same length. To achieve this, you may have to put small sections of trace tuning into the shorter line to equalize them. Although this will alter the symmetry of the lines slightly, the length is more important. If the unequal lengths are because of non-symmetrical pad locations, try to add your trace tuning in this area of the lines.
Industry Category