LED PCB
By:PCBBUY 06/03/2021 18:02
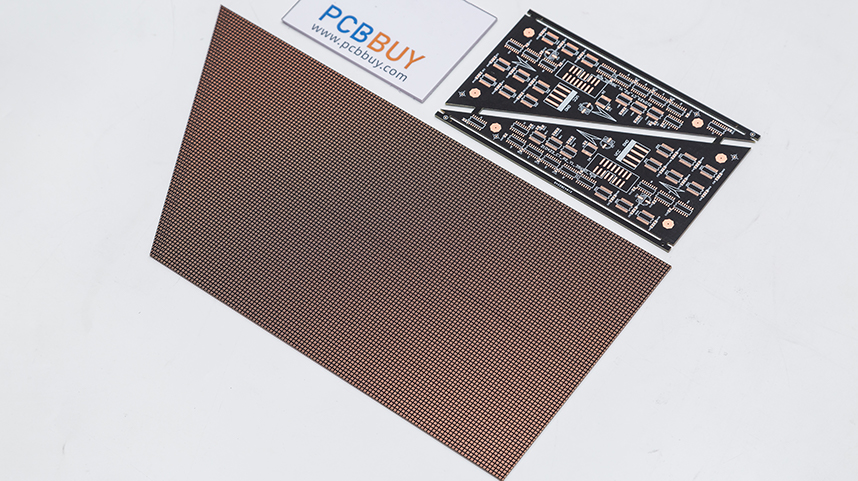
The rapid development of the printed circuit PCB influences the LED industry. Some LEDs were soldered on PCB to created lighting electronic products.
As we all know that LED will generate more heat compared with other electronic parts, which required the PCB to have a better ability for dissipating heat. For these special requirements, metal core PCB is frequently used on LED PCB, especially aluminum core PCB. This is because the aluminum PCB typically includes a thin layer of thermally conductive dielectric material that can transfer and dissipate the heat with much greater efficiency than a traditional rigid PCB.
Now SMD packaging type is the most widely used packaging form in LED applications. In general, it’s limited for the light emitted from a single LED component. Multiple LED components would be used for single light fixture to make sufficient light. Like other semiconductor devices, PCB is the best method to electrically connect the LED components. And a PCB with LED components soldered is usually called as “LED PCB”.
To help you understand why the LED lighting industry uses PCBs, we’ve outlined the nature of PCB base layers, the attractive qualities of aluminum PCBs and why they work well in the LED lighting industry.
What are the advantages of LED PCB?
When it comes to the advantages of using LED PCB, well there are plenty of them and we are now going to mention a few so that you know about the application too.
.Light in Weight
.No Dimension Issues
.Efficient Low Power Consumption
.Available In Different Sizes
.Heat Dissipation Performance
.Dust and Moisture resistant
.May be used in silver flex membrane switches and copper flex membrane switches.
How PCB influences LED industry?
For many companies within the LED PCB industry, aluminum PCBs are the new standard. This is because of the numerous benefits and features aluminum PCBs contain. Some of these benefits include the following:
Less Expensive
You can find aluminum in mines across the world, making it easy to access and refine, especially compared to other metals. This abundance means aluminum is much less expensive than other rarer metals. As a result, manufacturing with aluminum is also less expensive, especially when it comes to aluminum PCBs.
Aluminum-based circuit boards are also inexpensive when compared to other methods of heat transfer, such as heat sinks. While heat sinks may be slightly more effective at transferring heat than aluminum bases, they are much more expensive to add on to the PCB.
Environmentally Friendly
Most of us know that aluminum soda cans are recyclable, and aluminum boards are no different. Aluminum PCBs are recyclable and non-toxic, which means disposing of them is relatively easy and environmentally sound.
Improved Durability
Compared to ceramic and fiberglass, aluminum is much sturdier. This strong, durable material is much more resistant to breakage, and can better handle the stresses of the manufacturing process. This also means that the end PCB is much more resistant to damage from everyday handling, especially in impact-prone environments.
Lightweight
Despite how durable it is, aluminum is very lightweight. This means a PCB can have improved resilience without additional weight, an important factor in manufacturing. Not only this result in a lighter end product, but it makes shipping and handling of the circuit boards and end products much cheaper and easier to handle in large quantities.
Better Heat Transfer
In electronics, consistently high temperatures can cause serious damage, negatively affecting functionality. This makes heat transference one of the most important parts of a finished PCB.
Heat transference is a term referring to how well thermal energy moves from one place to another. How effectively a material does his depends on the materials conduction, convection and radiation. Conduction refers to how easily a material will transfer thermal energy from one area to another, while convection is the transfer of thermal energy from a material to a fluid and radiation refers to the amount of thermal energy a material gives off.
Aluminum has some of the best qualities for heat transfer, because it conducts thermal energy fairly easily, transferring it away from critical parts and minimizing thermal damage to the PCB. Comparatively, fiberglass is much less conductive. This difference results in PCB boards that are much more efficient at thermal energy transfer — in fact, aluminum-backed designs can be up to more efficient than fiberglass-backed designs by up to 10 times!
Because of these qualities, specifically the incredible ability to dissipate heat, aluminum PCBs have become the new PCBs of choice within the LED lighting industry. This growing popularity within the LED industry is due to a few incredible capabilities and improvements upon LED PCB designs made possible with aluminum PCBs. These include:
Increased LED Density
Each PCB design allows for a greater number of LEDs to mount onto it. Each of these LEDs produces heat, heating up the PCB more quickly. This can be a serious problem for the longevity of the LED lights, because each LED must stay within a strict range of temperatures in order to function properly.
Traditional fiberglass-based designs have a cap on the density of lights per board, purely because the board can get too hot. This is because fiberglass transfers heat relatively slowly, causing the heat to build up. With aluminum boards however, more LEDs can function simultaneously without exceeding the specified temperature tolerance. This is because in an aluminum-core PCB, heat transfers quickly and efficiently, due to the high thermal conductivity of the material.
Longer Operating Time
As with most electronics, the longer you use them, the hotter they get. This can negatively impact the functionality of the system and alter its operation, especially in more complex systems. In the case of LEDs, the quality and color of the lights change depending on how hot they get, and operating at a hotter temperature reduces the overall lifespan of the LED.
With aluminum LED PCBs, the improved heat transferring qualities of the material results in the LEDs operating at a lower temperature for a longer amount of time. This means aluminum PCB LEDs can operate for much longer before they finally fail.
Industry Category