What is OSP PCB Surface Finish through 3 Main Factors?
By:PCBBUY 04/09/2022 09:57
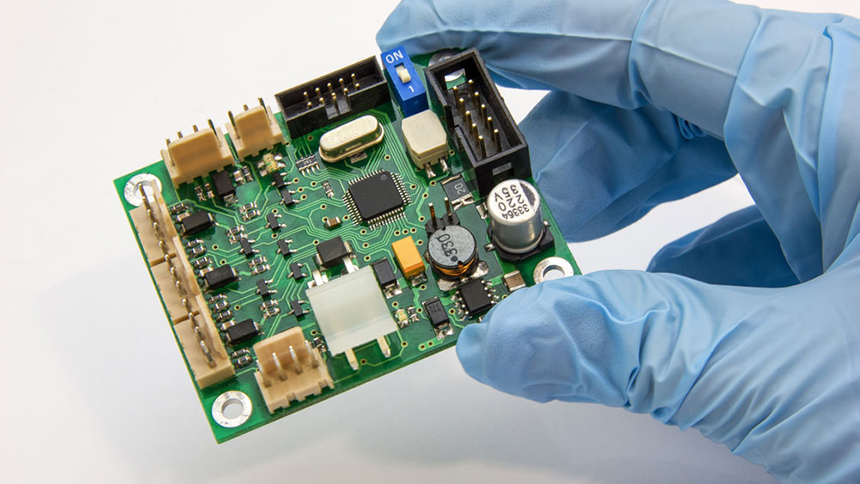
OSP is a water-based, organic surface finish that is typically used for copper pads. It selectively bonds to copper and protects the copper pad before soldering. OSP is environmentally friendly, provides a coplanar surface, is lead-free, and requires low equipment maintenance. However, it’s not as robust as HASL and can be sensitive while handling.
Are you going to learn more information OSP PCB surface finish? If you are going to search for knowledge about OSP PCB surface finish, please check and read the content to get all the details you want of OSP PCB surface finish.
What re the basic information of OSP PCB surface finish?
OSP is short for "organic solderability preservatives", and it's also called anti-tarnish. It refers to a layer of organic finish generated on clean and bare copper by adsorption. On the one hand, this organic finish is capable of stopping copper from being oxide, thermal shock or moisture. On the other hand, it has to be easily eliminated by flux in the later process of soldering so that the exposed clean copper can be jointed with melting solder so that solder joints can be generated in extremely short time.
The applied water-based chemical compound belongs to azole family such as benzotriazoles, imidazoles, and benzimidazoles, all of which get adsorbed on the copper surface with coordination formed between them and copper atoms, leading to the production of film. In terms of film thickness, film made through benzotriazoles is thin while that through imidazoles is relatively thick. The differentiation on thickness will bring distinct impact to effect of board finish which will be discussed in the later part of this article.
Why to choose OSP PCB surface finish?
This process maintains the copper surface from oxidation by applying a thin protective layer of a water-based organic compound over the exposed copper usually using a conveyorized method.
· The manufacturing process is simple and reworkable
· OSP coated boards perform better in terms of solder wetting.
· Low Cost
· Good for SMT assembly
· Flat Surface
What is the process of OSP PCB surface finish?
Oil Removal:
The effect of oil removal directly affects the quality of film formation. Poor oil removal, resulting in uneven film thickness. On the one hand, the concentration can be controlled within the process range by analyzing the solution. On the other hand, always check the oil removal effect is good, if the oil removal effect is not good, it should be replaced in time.
Micro-corrosion:
The purpose of Micro-corrosion is to form a crude copper surface which is easy to do the film formation. The thickness of the micro-corrosion directly affect the film-forming rate, therefore, to form a stable film thickness, it is very important to maintain the stability of micro-corrosion thickness. The general micro-corrosion thickness shall be controlled at 1.0um to 1.5um which is more appropriate, so that before each production, the micro-corrosion rate can be measured and the micro-corrosion time can be determined according to the micro-corrosion rate.
Film Formation:
It would be better to use the DI washing both before and after the film formation and the PH should be limited to between 4.0 and 7.0 to prevent contamination of the film forming solution. The key of OSP process is to control the thickness of anti-oxidation film which can easily affect welding performance. Generally, the film thickness is appropriate between 0.2-0.5um. For example, the thinner the film is, the poorer thermal shock capacity will be.
What are the benefits of OSP PCB surface finish?
Selecting the appropriate finish will depend on various factors, such as the finishing process, the PCB’s design and the quality of the final result. Not all finish types are appropriate for every PCB. Below are a few characteristics to keep in mind when considering the different ones:
Solderability
Avoiding soldering issues is essential to creating a PCB that will operate as intended. Smooth surfaces are necessary to ensure a connection that functions adequately within its given environment. Consider whether the surface finish can solder directly to the copper, such as in the case of immersion tin, or if it’s a layered technique, like ENIG.
Good wire bonding is also crucial, considering that different metals require unique manufacturing techniques and behave differently even in the same environments. Wires may consist of materials like aluminum, gold and copper, with each surface finish type being compatible or incompatible with these elements.
Processing Time
The processing window for a specific finish may be large or small — finishes like HASL have larger processing windows.
How much time the process takes depends on how complex the assembly is. Some surface finishes, like OSP, have limited thermal cycles and can’t withstand numerous soldering processes. After a few cycles, it will disappear, and the PCB will lose its protection against oxidation. However, an OSP surface finish for a PCB can be reworked during fabrication. The same applies to immersion silver.
Reliability
How well will the chosen surface finish stand up to its environment? If your PCB will need to meet specific reliability requirements, you will want a finish that accommodates these. Although cost is only one component of the many other elements mentioned here, you should consider how high the cost of failure will be if the PCB’s finish doesn’t work as intended and fails to protect the surface.
The IPC offers a set of standards under its TM-650 Test Methods Manual that details different ways to test PCBs for reliability and quality. These include techniques such as dimensional verification, chemical resistance, copper ductility and amount of signal loss. One test uses chemicals such as sulfuric acid and isopropanol to determine the effects these substances have on PCB dielectric materials.
Why OSP PCB surface finish is popular?
A PCB’s electrical connection depends on copper conductivity. However, whenever you expose copper to humidity, it tends to undergo oxidation. This causes problems in soldering, requiring high temperature that threatens the solid fixation of components on the printed circuit board. It also reduces the end product’s reliability.
Concerning PCB performance, surface finish undergoes two major responsibilities. First, protects the copper from oxidation. Second, offering a surface that delivers high solderability whenever you are set to assemble the components on the printed circuit board.
You can classify board finishes based on the type of technologies. Also, you can do this according to the chemical substances they are involved in. These include ENEPIG, ENIG, OSP, Immersion Silver/Tin, Hot air soldering leveling (HASL), and more. In comparison with other types of finishes, OSP is becoming prevalent due to its environment-friendly and low cost attributes. This is one good reason why we must understand it better. This is what this article is focuses on.
Industry Category