OSP finish PCB
By:PCBBUY 06/03/2021 18:08
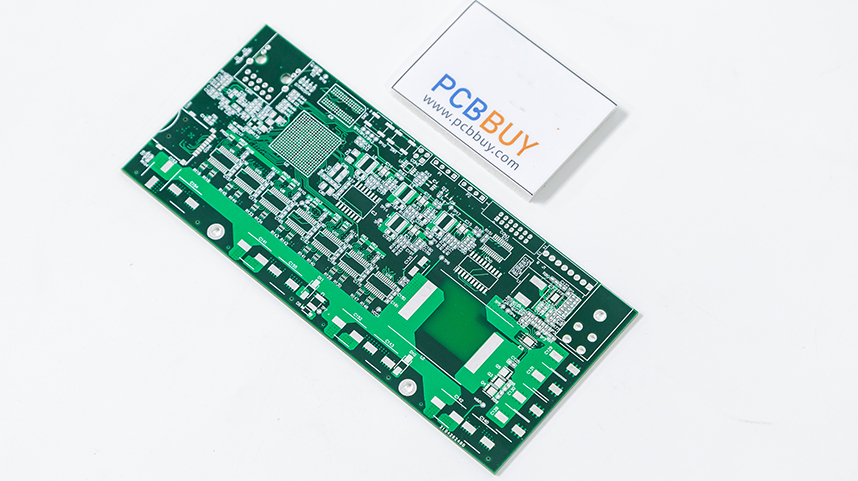
An OSP surface finish is an example of an organic PCB finish. There are no toxins involved in the process, making it environmentally friendly while still retaining its protective and anti-corrosive properties. Because of the absence of harmful chemicals, OSP boards are also RoHS compliant. This water-based finish provides a flat surface for attaching additional PCB components, and like the HASL process, it is cost-effective.
OSP can be used as an effective replacement for lead-free HASL due to its co-planarity. When you need a PCB surface finish that will provide sufficient flatness while offering a simple manufacturing process, OSP is arguably the best choice.
In s passage we will focus on the OSP finish and if you are curious about the detailed knowledge, check and read the content we provide below:
What is the OSP finish process?
Applying an OSP surface finish to a PCB usually involves a conveyorized chemical method or a vertical dip tank. The process generally looks like this, with rinses between each step:
Cleaning: The copper surface of the PCB is cleaned of oil, fingerprints and other contaminants that could affect the flatness of the applied finish.
Topography enhancement: The exposed copper surface undergoes micro-etching to increase the bond between the board and the OSP. This process also reduces oxidation. To achieve adequate film thickness, the micro-etching must be kept at a consistent speed.
Acid rinse: The PCB undergoes an acid rinse in a sulfuric acid solution.
OSP application: At this point in the process, the OSP solution is applied to the PCB.
Deionization rinse: The OSP solution is infused with ions to allow for easy elimination during soldering. This rinse should be used before preservatives build to avoid tarnishing from the presence of other ions in the OSP solution.
Dry: After the OSP finish is applied, the PCB must be dried.
OSP offers a simple and affordable process, but it’s also important to keep in mind that it’s extremely sensitive to handling and can easily retain scratches, which can degrade its solderability. Additionally, its shelf life is shorter than that of ENIG or HASL.
Common uses for OSP include:
Fine pitch devices: This finish is best to apply to fine pitch devices because of the lack of co-planar pads or uneven surfaces.
Server boards: OSP’s uses range from low-end applications to high-frequency server boards. This wide variation in usability makes it suitable for numerous applications. It’s also often used for selective finishing.
Surface mount technology (SMT): OSP works well for SMT assembly, for when you need to attach a component directly to a PCB’s surface.
What are the advantages of OSP?
Nowadays, OSP has been usually applied due to its advantages that are discussed below:
• Simple manufacturing process and Reworkable: Circuit boards coated with OSP can be easily reworked by PCB fabricators so that PCB assemblers are allowed to have fresh coatings once its coating is found damaged.
• Good wettability: OSP-coated boards perform better in terms of solder wetting when flux meets vias and pads.
• Environment friendly: Since water-based compound is applied in the process of OSP generation, it does no harm to our environment, just falling into people's expectations for green world. As a result, OSP is an optimal selection for electronic products catering to green regulations such as RoHS.
• Low cost: Due to the simple chemical compounds applied in OSP creation and its easy manufacturing process, OSP stands out in terms of cost among all types of surface finishes. It costs less, leading to a lower cost of circuit boards in the end.
• Fit for reflow soldering in double-side SMT assembly: Along with the constant development and progress of OSP, it has been accepted from single-sided SMT assembly to double-sided SMT assembly, dramatically widening its application fields.
• Low requirement for solder mask ink
• Long storage time
What is the storage requirement of OSP?
OSP needs adequate care during transportation and operation because OSP technology’s generated preservatives can cut as thin. With the long exposure of PCBs with OSP as a surface finish to humidity and high temperature, there is a possible generation of oxidation on PCBs’ surface. As a result, it can result in low solderability. Thus, some of the principles of soldering technique to use include:
Users must use a humidity display card and desiccant to utilize a vacuum package. They can also stop friction from destroying the PCB surface by placing release paper between PCBs.
Users must not directly expose these PCBs to the sunlight. For an optimal storage environment, the requirements are storage time of fewer than 12 months, the temperature of about 15 to 300C, and relative humidity of about 30 to 70 percent RH.
Industry Category