PCB Drilling
By:PCBBUY 08/31/2021 09:27
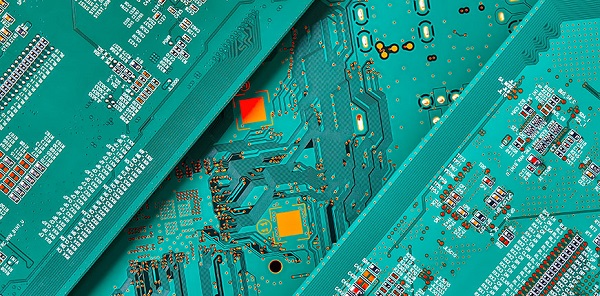
As a very important process of PCB manufacturing, drilling plays an essential role to affect the performance and quality of the finished products. When holes are drilled typically on a board base to thermally and electrically connect the board layers is known as drilling on a circuit board. These holes when connects the board layers is called vias. The main purpose of performing a drilling operation in the PCB fabrication process is to insert a through hole component lead or to connect the board layers for developing smooth circuitry on the PCB.
In this passage we will tell you everything about PCB drilling if you are interested in it, please check and read the content we provide to learn more professional information.
What are the technologies of PCB drilling?
This drilling process is made easy with the innovations in technologies over the years. Now PCB drilling can be done with small diameter drill bits, automated drilling machine, CNC drilling machine and many other effective drilling types of machinery that can suit with the PCB manufacturing of multiple type of circuit boards.
Automated drilling machine can drill the holes in the circuit board by controlling the drilling operations with a computer. When many holes need to be drilled of different sizes and diameter, CNC machine is one of the effective solution saving time and cost of production.
In case of drilling registration holes to make sure that further drilling performed on the center of the internal layer pads will be precise, an x-ray drill is used. This technology is used when via holes are linking copper layers together and holes are drilled on the leaded components.
In case of vias with very small diameter, using mechanical drill bits caused increasing of breakage on the circuit board in turn increasing the cost. When very small holes are drilled in, the board and connected with the board layers, they are termed as micro vias. One of the extensively used drilling technologies in current times is CO2 laser drilling, which is used for drilling and processing internal layer via holes.
In case of holes to be drilled for connecting only some copper layers instead of passing through the whole circuit board, one can go for a controlled depth drilling or performing pre-drilling on the sheets individually before PCB lamination or laser drilling mechanism.
It is recommended to take the help of PCB drilling experts at the initial stage of the PCB project while deciding on the PCB layout and technique of production in PCB manufacturing.
What the different types of are via drilled in PCB?
A raw circuit board can have many fabricated properties, including cut-outs, slots, and the finished board’s overall shape. The largest number of such properties will be the holes that are drilled into the board. The purpose of these holes can be broken down into three categories:
Via Holes
Small holes plated with metal are used to conduct electrical signals, power, and ground through the board layers. These holes are known as vias, and they come in different types depending on what is required:
Thru-hole: This is the standard via, and it goes through the entire board layer stackup from top to bottom. These vias can connect to traces or planes on as many internal layers as needed.
Buried: These vias start and stop on internal board layers without extending to an external layer.
Blind: A blind via starts on an external layer but only goes partway through the board. As with buried vias, they are more expensive to fabricate, but they free up room for routing, and their shorter barrel can also help improve the signal integrity of high-speed transmission lines.
Micro: This via has a smaller hole size than the others because it’s drilled with a laser.
Component holes
While surface mount parts are used for most active and discrete components on circuit boards today, many parts are still preferable to use with a thru-hole package. These components are typically connectors, switches, and other mechanical parts that need the more robust mounting that a thru-hole package provides.
Mechanical holes
A circuit board will usually have mechanical features or objects attached to it, such as brackets, connectors, or fans, which require holes for mounting. Although these holes are generally not plated with metal, they can be if the mounted feature requires an electrical connection to the board, such as chassis ground. In some cases, mounting holes are used to disperse the hot components’ heat to the inner plane layers.
What are the considerations of PCB drilling?
The drill press consists of a high-speed spindle, which rotates at speeds of about 300k RPM. These speeds are essential to produce the required accuracy for micron-level drilling on the PCB.
To maintain accuracy at high speeds, the spindle makes use of an air bearing and a direct drill bit assembly, which is held by a precision collet chuck. Additionally, the vibration of the tip of the bit is controlled within a 10-micron range. In order to maintain the exact position of the hole on the PCB, the drill is mounted on a servo table, which controls the motion of the table on the X and Y-axes. A tunnel actuator is used to control the motion of the PCB in the Z-axis.
As the pitch of the holes in the PCB assembly line is constantly decreasing and the demand for higher throughput is respectively increasing, the electronics to control the servo may lag behind at some point in time. The use of laser drilling to create through holes for manufacturing PCBs helps reduce or eliminate this lag and is the next generation’s requirement.
Industry Category