PCB assembly
By:PCBBUY 04/29/2021 18:01
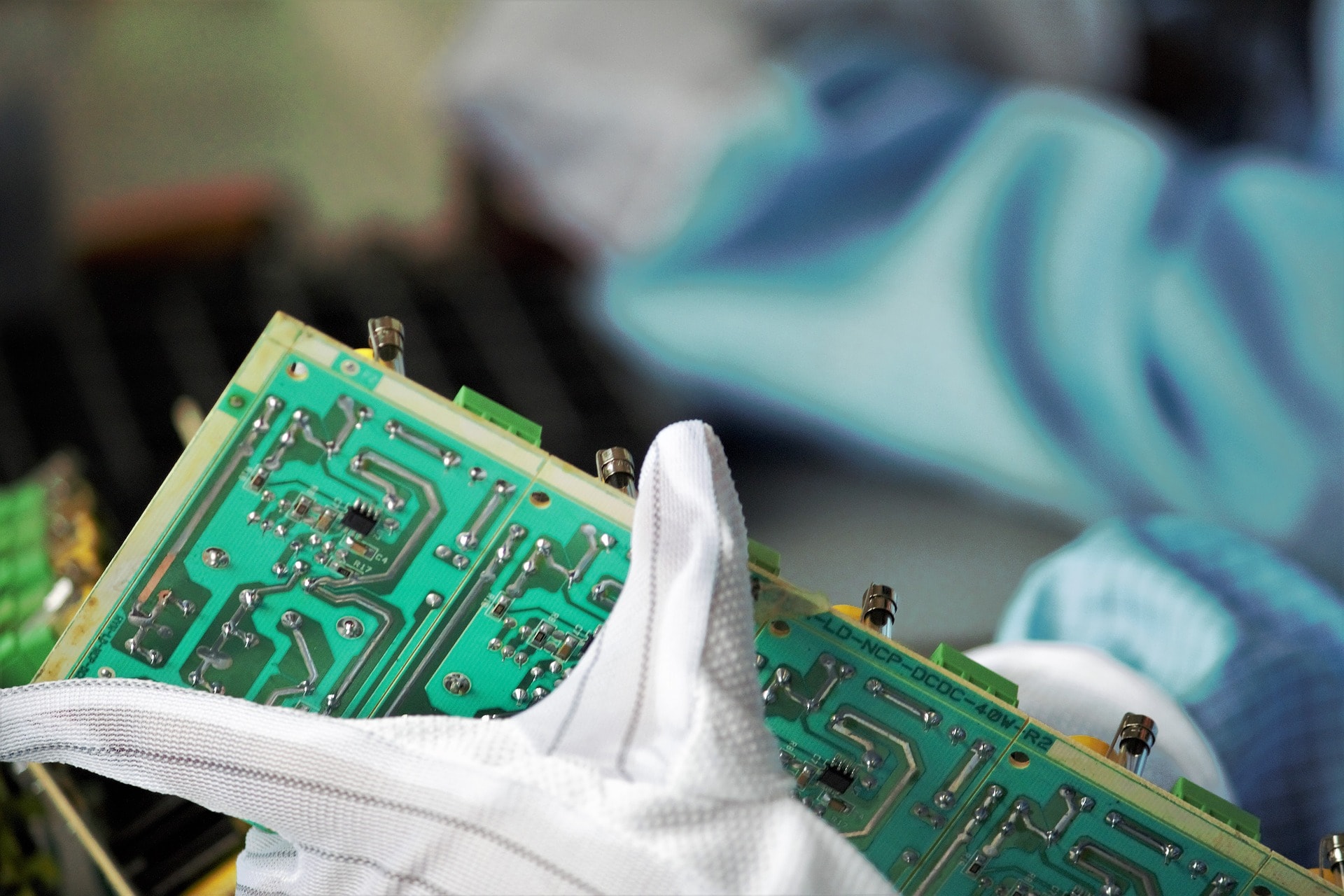
Within a printed circuit board electronics assembly, production or manufacturing process there are a number of individual stages. Each stage of assembly and production must be compatible with the next, and there must be feedback from the output to the input to ensure that the highest quality is maintained. In this way any problems are detected quickly and the process can be adjusted accordingly.
A PCB with components mounted on is called an assembled PCB and the manufacturing process is called PCB assembly or PCBA for short. The copper lines on bare board, called traces, electrically link connectors and components to each other. They run signals between these features, allowing the circuit board to function in a specifically designed way. These functions range from the simple to the complex, and yet the size of PCBs can be smaller than a thumbnail.
And how PCBs are assembled? The PCB assembly process is a simple one, consisting of several automated and manual steps. With each step of the process, a board manufacturer has both manual and automated options from which to choose. To help you better understand the whole PCBA process in detail, we will provide you each step in detail below.
The PCB assembly process
What is solder paste stenciling?
The first step of PCB assembly is applying a solder paste to the board. Stencil,manufactured from metal or polymer, is applied with solder paste to all of the pads on the bare-board. This process is typically referred as solder paste stenciling. Stencil is used for solder paste stenciling process that consists of a bunch of holes and resembles to the SMD footprint pads on bare-board layout. The stencil is placed over the boards and a layer of solder paste is squeegee over it. This leaves a nice and uniform layer of solder on the SMD pads. The primary function of solder paste stenciling includes binding, connecting and cleaning.
What is pick and place?
Development of pick and place systems are directly related to the growing importance of surface mount technology. These systems have become an important aspect of PCB assembly line. Pick and place systems offer automated, faster and highly efficient solutions during the assembly process. They place components automatically on the PCBs. Traditionally, this was a manual process done. These days this step is an automated process among in order to the relatively faster operational rate and minimum errors.
What is reflow soldering?
Reflow soldering has gained significant attention over the past few years, particularly for its use in attaching surface mount components to printed circuit boards. Reflow soldering is primarily used to form the required solder joints. This process is carried out by pre-heating the components and solder paste, and melting the solder without causing damage.
Once the solder paste and surface mount components are all in place. This means the solder paste needs to solidify, adhering components to the board. PCB assembly accomplishes this through a process called "reflow".
What is deionized water cleaning of assembled boards?
Deionized water is used for the cleaning of PCBs before they leave the shop floor. Whenever a board is made or revamped, there is a substance called flux that is residue on the board. And this flux buildup winds up clingy after several months, can turn out to be marginally acidic prompting a debilitating of solder joints which will cause corrosion and longevity issues.
To clean the boards after assembly, we place the batches into a high-temperature, high-pressure equipment, all stainless-steel device. Any other metal would quickly disintegrate.
What is inspection and quality control?
In PCB assembly, quality control is very important at every stage. Further, inspection and quality control are performed by our industry experts in several different stages including visual inspection, structural inspection and automatic inspection. These technologies improve performance and offer overall defect coverage. Optical inspection, laser triangle measurement, X-ray inspection and X-ray lamination technology are some of the major technologies used in automatic inspection. Each of these technologies offers distinct benefits over another.
What is through-Hole component insertion?
A through-hole component is commonly identified as a device that is soldered with a wire or a metallic lead and mounted to the board. These components are placed with the help of the lead on plated holes of the board. Soldering is performed after placing these components on the respective plated holes. Critical factors to be considered include quality of the solder joint and the connection.
Strong mechanical bonds make through-hole component insertion technique superior to the SMT technique. Other advantages include reduced available routing area for signal traces on layers and cost-efficiency. Limited routing space for signal traces on layers are available for all lower layer on multilayer boards as holes pass through all layers on the opposite side.
What is mechanical customized insertion?
The need for customization of mechanical components has risen over the past few years. Different types of mechanical components include wires, heat-sinks, spacers and stand-offs, screws, and connectors. The effective adoption of customized insertion solutions involving various mechanical components will ensure performance enhancement for PCBs.
In addition, edge mount connectors and linear connectors also require customized insertion during PCB assembly. The use of turret solder for press mount terminal, which requires specialized tooling like swage tools, is also part of mechanical components.
What is conformal coating?
Conformal coating is typically used for protecting circuit boards from harsh environmental conditions, including moisture and chemical contaminants. The conformal coating is applied on PCBs and acts as a protective chemical coating or polymer film with a 25-75µm thickness. Conformal coating also helps to maintain long-term surface insulation resistance (SIR), thereby ensuring the operationality of the assembly.
What is final Inspection and functional test?
TFCT, also known as functional testing, is carried out during the last phase of the PCB assembly line. After the soldering step of the PCBA process is finished, a final inspection will test the PCB for its functionality. This inspection is known as a "functional test". The test puts the PCB through its paces, simulating the normal circumstances in which the PCB will operate.
Testing is the final and most important step in PCB assembly process, as it determines the success or failure of the process. This testing is also the reason why regular testing and inspection throughout the assembly process is so important.
Industry Category