PCB wave soldering
By:PCBBUY 06/15/2021 18:03
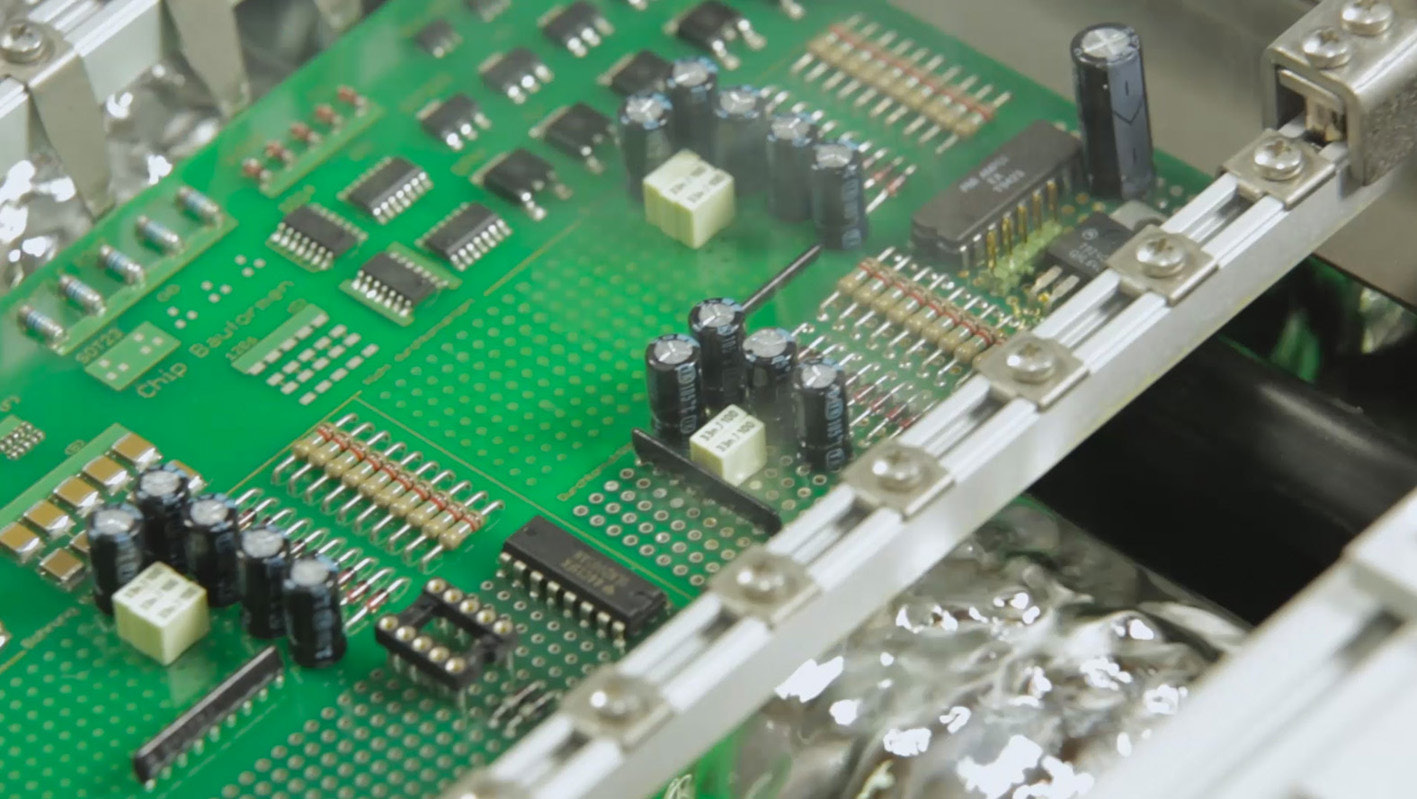
Back to the days when surface mount technology was not entirely developed, "wave soldering" was a very famous soldering technique. Nearly every PCB used wave soldering for the placement of electronic components. Wave soldering is a mass soldering procedure that will permit you to make many PCBs quickly.
You will need to pass every PCB over a pan of liquefied solder. There, a pump will create a surge of solder that will resemble a standing "wave." This standing wave showers over the printed circuit board, and the electronic components will get soldered to the PCB. So, the contact between the solder and the lock does the magic.
After that, the printed circuit board gets blowing air or water spray for safe cooling. This cooling process will secure the components in their place. Furthermore, wave soldering is usually done in a shielding gas environment as nitrogen usage helps mitigate solder defects.
What is the PCB wave process?
1. Wave Soldering Machine
In the market, you will encounter many kinds of wave soldering machines. You can buy lead wave solder machines or lead-free wave solder machines. It is all up to you. However, the main principles and fundamental parts of all of these machines are alike. A conveyor is an essential part that is used during this process. It takes printed circuit boards via various zones.
Next, you will see a pan of the solder and pump responsible for generating the primary wave. Furthermore, you will also get a flux sprayer and a preheating pad. Hence, these four main parts make up a soldering machine. The solder in wave soldering machines is mostly made up of metals' mixture.
If the machine has leaded solder, it will contain 49.5% lead, 50% tin, and 0.5% antimony. However, in the latest devices, lead-free models are available due to health concerns. So, tin-copper-nickel and tin-silver-copper alloys are frequently used.
2. Wave Soldering Temperature
Currently, tin alloys for soldering are regularly using Sn 60/Pb40 and Sn 63/Pb37. Therefore, it is recommended that you should make sure that the operating temperature stays around 260° ± 5°C. Nonetheless, you should also take into account the overall weight of the PCB and the parts.
Practically, heavy components can be heated up to 280°C. Lightweight components, which are heat-sensitive, can be heated at a temperature as low as 230 °C. Further, it would help if you also considered preheating and the conveying speed.
However, it is best to change the conveying speed rather than tin's temperature because the temperature change will damage the solder joints' quality by affecting the fluidity of the liquefied container. At high welding temperatures, copper will start to dissolve, and this will ruin the quality control of overall soldering.
3. Fluxing
During the wave soldering, you should apply liquid flux on the printed circuit board surface. You will observe that fluxing will enhance the soldering quality of the electronic components. These components, printed circuit boards, and also in liquid, when stored, are exposed to the atmosphere. This exposure can make them oxidized and thus affects the soldering quality.
Flux mainly removes dirt and oxides on the surface of the metal. Further, it also creates a film to stop the air from reacting with the metal surface during a high-temperature setup. Thus, solder cannot get oxidized easily. Nonetheless, it would help if you used the liquefied tin for soldering during the wave soldering process.
Currently, the melting point of the SAC305 lead-free solder is around 217 °C. And, the flux cannot be exposed to such a high temperature for long. Hence, if you wish to use change, you should add it before the printed circuit board goes through the tin solution.
Commonly, flux can be applied by two means. First, you can use a foaming change, and second, you can add it by spraying. In foaming flux, the flux gets attached to the circuit board, which passes through it. The major downside of this way is that you may observe that change is not uniformly applied. Thus, poor soldering can happen in the areas where flux doesn't exist.
In the spraying method, the flux is sprayed through the nozzle as the circuit board passes. The drawback of this method is that the change can be quickly given through the board gaps. And, flux can also directly pollute the electronic components of the circuit board's front. Further, if the change is not processed and only dropped straightly on the board, you can also observe the corrosion of the board.
4. Preheating
Normally, Preheating before the primary wave welding process begins. It can increase the upper plate's temperature to between 65 and 121°C with a heating rate lying between 2 °C /s and 40 °C /s. You will not be able to get the best soldering results if preheating is insufficient. It is because flux may not be able to reach every part of the PCB. On the other hand, if you set a very high temperature for preheating, "no-clean" flux can suffer. Now, if you are wondering what exactly a "no-clean" change is, we have explained it in the next sub-section.
5. Cleaning
The cleaning process washes a PCB with deionized water or with solvents to get rid of flux remains. However, there exists a kind of flux that doesn't need cleaning. Can you guess which one? Yes, of course, the "no-clean" changes, their remains after the soldering process, are benign.
But, it would help if you were careful; some applications do not want "no-clean" fluxes. It is only because "no-clean" changes can be susceptible to the conditions of the process. Now you know all about the wave soldering process.
Industry Category