Pad in PCB Design
By:PCBBUY 08/12/2021 17:19
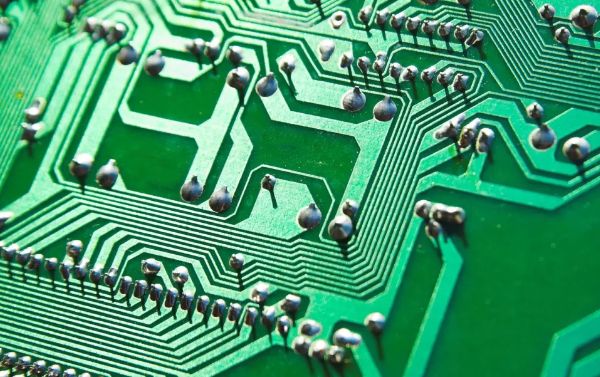
A pad is the exposed region of metal on a circuit board that the component lead is soldered to. Multiple pads in conjunction are used to generate the component footprint or land pattern on the PCB. The two types of pads available are through-hole and surface mount pads. In this passage, we will focus on the topic, please check and read the content below to learn more knowledge.
What are the types of pad?
Surface mount pads
Pads used to mount surface mount components are called surface mount pads. These pads have the following features:
1. Pad which shows the copper area. This can be rectangle, round, square, or oblong.
2. Solder mask layer
3. Solder paste
4. Pad number (number of pads present for the component)
SMD pad vs NSMD pad
Proper pad design is critical to ensure the manufacturability of BGA components. There are basically two types of BGA pads – the solder mask-defined pad (SMD) and the non-solder mask-defined pad (NSMD).
Solder mask defined (SMD) BGA pads
SMD pads are defined by the solder mask apertures applied to the BGA pads. These pads have the solder mask aperture such that the mask opening is smaller than the diameter of the pad they cover. This is done to shrink the copper pad size that the part will be soldered to.
The image shows how the solder mask has been specified to cover a part of the copper pad underneath. This can lead to two advantages – firstly, the overlapping mask helps prevent the pads from lifting off the board because of mechanical or thermal stress. The second advantage is that the opening in the mask will create a channel for every ball on the BGA to align with while the part moves through the soldering process.
The copper layer of an SMD BGA pad conventionally has a diameter equal to the pad on the BGA. To generate the SMD overlay, a reduction of 20% is traditionally used.
Non-solder mask defined BGA pads (NSMD)
NSMD pads vary from SMD pads in that the solder mask is defined to not contact the copper pad. The mask is instead created such that a gap is generated between the pad edge and the solder mask. Here the copper pad size is defined by the copper pad diameter instead of the mask layer
NSMD pads can be smaller than the diameter of the solder ball, and this reduction in pad size is 20% of the ball diameter. This approach leaves more room between adjacent pads enabling easier trace routing and is used for high density and fine pitch BGA chips. One disadvantage of NSMD pads is their high susceptibility to delamination due to thermal and mechanical stresses. However, NSMD pad delamination can be prevented when standard manufacturing and handling practices are followed.
Through-hole pads
Pads used to mount through-hole components are called through-hole pads and are of two types:
The plated through-hole (PTH)
PTH refers to a pad with a through-hole. The hole wall will be plated with copper and sometimes with solder or another protective plating. The hole plating is done using the process of electrolysis. The plating provides for electrical connection between the different layers of the board.
The non-plated through-hole
NPTH refers to a pad without plating in the hole. This pad is mostly used for single-sided boards or these holes are used for mounting the PCB in an enclosure and screws are mounted through these holes. Conventionally, unplated holes will have an area around the hole that is clear of any copper (similar to board edge clearance). This is done to prevent shorts between copper layers and parts that are to be placed.
What are the considerations of Pad in PCB Design?
Ensuring a PCB pad stack design meets manufacturability and reliability requirements needs one to consider several factors:
· Maximum tolerances build up the minimum insulation between opposing conductors, which in this case refers to the hole plating and the copper in the trace and plane layers. They need to comply with the standards of the engineered product. For telecommunication equipment, a minimum insulation spacing of 4 mils is required and for other products it is 5 mils.
· There need to be robust connections between traces and plated through-holes or vias.
· The aspect ratio needs to be such that the hole wall should withstand the stress of the plating process without failure.
Even if you follow the guidelines above, drilled holes might not always pass through the board as specified. This might happen due to the following factors:
· Drill wander can occur where the drill can deviate from the preferred drilling axis (eccentricity)
· Alignment errors in the film layers
· Laminate shrinkage during lamination. This might lead to an error in locating the drill hole.
· Inaccurate registration of the layers during lamination
Drill wander is when drilled holes are off from where they are actually supposed to be. Each manufacturer would have reached a tolerance after going through its process, called drill tolerance. This drill tolerance is used to define the hole shadow of every drill hole. High precision manufacturers can keep the tolerance down to ±5 mils also known as TIR (total included radius). In the US, middle-tier manufacturers can keep this tolerance down to ±6 mils and other manufacturers can hold it down to ±7 mils. It is important for the PCB designer to know where the board will be manufactured to provide accurate allowances for the drill wander error. When it comes to high-volume production, drill wander tolerance should be much higher.
Industry Category