What is Signal Integrity Analysis in PCB Design for Designers?
By:PCBBUY 11/20/2021 09:23
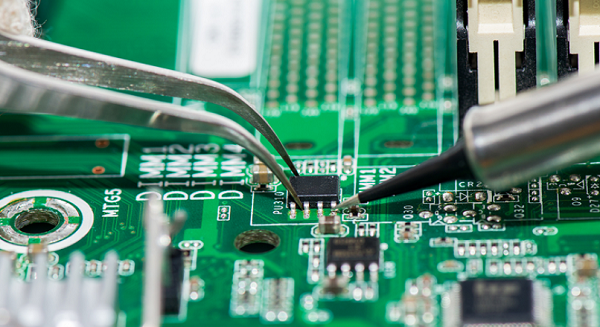
Extensive research has been done on the best way to design transmission lines so high-speed signals can travel at maximum efficiency. To reduce potential problems with signal integrity and other transmission issues, it’s important to make sure your PCB supplier provides boards with a strong design.
If you are curious about the signal integrity analysis in PCB design, please check and read the content for more information in this passage.
What are the considerations of signal integrity in PCB design?
When we have signal integrity issues in a PCB, it may not work as desired. It may work in an unreliable manner – works sometimes and sometimes not. It may work in the prototype stage, but often fail in volume production; it may work in the lab, but no reliably in the field; it worked in older production lots, but fails in new production lots, etc. A signal is said to have lost its integrity when:
· It gets distorted, i.e. its shape changes from the desired shape
· Unwanted electrical noise gets superimposed on the signal degrading its signal to noise (S/N) ratio
· It creates unwanted noise for other signals and circuits on the board
A PCB is said to have requisite signal integrity when:
· All signals within it propagate without distortion
· Its devices and interconnections are not susceptible to extraneous electrical noise and Electromagnetic Interference (EMI) from other electrical products in its vicinity as per or better than regulatory standards
· It does not generate or introduce or radiate EMI in other electrical circuits/cables/ products either connected to it or in its vicinity, as per or better than regulatory standards
What are the issues of PCB signal integrity?
PCB signal integrity issues mainly include signal reflection, crosstalk, signal delay, and timing errors.
Reflection
When the signal is transmitted on the transmission line, when the characteristic impedance of the transmission line on the high-speed PCB does not match the source impedance or load impedance of the signal, the signal will be reflected, causing the signal waveform to overshoot, undershoot and the ringing phenomenon caused by it. Overshoot refers to the first peak (or bottom) of the signal transition. It is an additional voltage effect above the power supply level or below the reference ground level. Undershoot refers to the signal jump change to the next valley (or peak). Excessive overshoot voltage often impacts the device for a long period of time, causing damage to the device. Undershoot will reduce the noise margin. Ringing increases the time required for signal stabilization, which affects system timing.
Crosstalk
In PCB, crosstalk refers to the undesired noise interference caused by the electromagnetic energy through the mutual capacitance and mutual inductance coupling to the adjacent transmission line when the signal propagates on the transmission line. It is caused by interaction of different structures of the electromagnetic field in the same area. Mutual capacitance causes coupling current, which is called capacitive crosstalk; while mutual inductance causes coupling voltage, which is called inductive crosstalk. On the PCB, crosstalk is related to trace length, signal line spacing, and the condition of the reference ground plane.
Signal delay and timing error
The signal is transmitted at a limited speed on the wires of the PCB, and the signal is sent from the driver to the receiver, with a transmission delay in between. Excessive signal delays or mismatched signal delays can lead to timing errors and disrupted logic device functionality.
High-speed digital system design analysis based on signal integrity analysis can not only effectively improve product performance, but also shorten product development cycles and reduce development costs. With the development of digital systems toward high speed and high density, it is extremely urgent and necessary to master this design weapon. With the continuous improvement and improvement of signal integrity analysis models and calculation analysis algorithms, digital system design methods that use signal integrity for computer design and analysis will be widely and comprehensively applied.
What are the tools for PCB signal integrity?
MATLAB is a great tool and many of the standard calculations you’d need to perform are built into MATLAB. This includes calculations that are specific to network analysis, which is an indispensable part of signal integrity analysis in PCB design. Some of these tasks include:
· Circuit design and simulation tools. SPICE simulators are the cornerstone of modern circuit design and evaluation. They basically automate a complex matrix algebra problem and return electrical data at any point in your circuit.
· Fourier and Laplace analysis. These are applicable in circuit design, transmission line design, and any other area of signal integrity analysis in PCB design involving conversions between time-domain data and frequency-domain data.
· S-parameter manipulations. I’ve always thought S-parameters were a bit overgeneralized, but they have conceptually satisfying meanings in specific situations. You’ll often need to convert between different parameters.
· Signal processing tasks. Fourier/Laplace analysis is probably the most common task, but there are many other tasks that you might need to perform as part of wrangling waveform data from measurements or simulations. Convolution, statistical analysis, and regression are a few examples.
· Optimization tools. MS Excel includes three basic optimization algorithms as part of the Solver package, which you can use for signal integrity analysis in PCB design. These are an evolutionary algorithm with constraint handling, generalized reduced gradient (GRG Nonlinear), and simplex algorithms. These are easy to access, configure, and execute when you have a large set of interrelated data. More advanced optimization problems (multi-objective, numerical, discrete, etc.) require specialized tools or scripting.
· 3D EM field solvers. Advanced design tools will contain field solvers for automating certain signal integrity tasks. When you’re designing unique design structures or you need to visualize EMI emissions/reception in your board, a field solver is by far the best tool you can use.
Industry Category