What is Solder Mask Used for PCB Manufacturing Process?
By:PCBBUY 04/13/2022 09:48
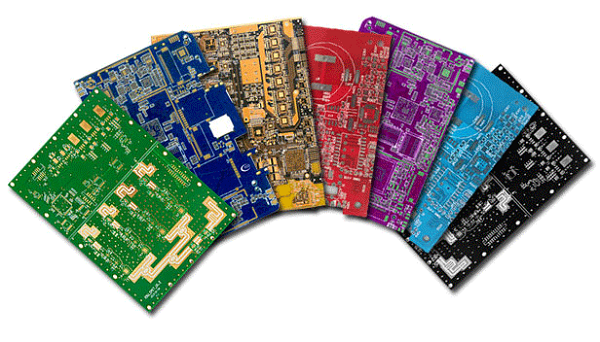
There are different types of colors available for PCB boards. The standard color of printed circuit boards is the green solder mask. However, with the advent of much innovation and technological advancement, the color of PCBs is now changing. In recent years the use of other colors instead of green PCBs is on the increase was driven by most of the assemblers.
In this passage, you can get everything about the information of solder mask usages. If you are interested in the uses of solder mask, please check and read the content below for more knowledge.
What are main types of PCB solder mask?
Top and bottom side masks
These are typically used by engineers to identify openings in the green solder mask, already applied on the PCB. This particular layer of solder mask is added through epoxy or film methods. Next, the component pins are soldered to the board utilizing the openings that have been registered using the masks.
The traces on the top-side of the board are called top traces and the corresponding solder mask used is called a top-side mask. Identical to the top-side mask, the bottom mask is used for the bottom side of the board.
Epoxy liquid solder masks
The most cost-effective option among solder masks is epoxy. It is a polymer that is silkscreened on the PCB. Silkscreening refers to a printing technique that uses a woven mesh to support ink-blocking patterns. The mesh enables the open areas to be identified for the process of ink transfer. This step is then followed by thermal curing.
Liquid photoimageable (LPI) solder masks
LPI solder masks are actually a mix of two distinct liquids. These liquids are kept separately and mixed right before the application of the mask layer to enable longer shelf life. LPI is also one of the more cost-effective options among various other types.
LPI is employed for curtain coat, screen printing, and spray applications. This mask is a blend of various polymers and solvents. A thin coating can be formed using this mask that can stick to the target area surface. After using this mask, the PCB will generally not require any final surface finish that is currently available.
What the solder mask should be used?
An appropriate solder mask depends upon the physical dimensions of the board, components, holes, and conductors, the surface layout, as well as the final application for your product.
You will need a photoimageable solder resist for most modern PCB designs. The surface topography will depend on whether to use a liquid or dry application. And a dry application is that lay down a uniform thickness across the entire surface. But it will be the best for dry mask adheres of your PCB surface is very flat. And if there are complex surface features, you’d better select with a liquid (LPISM) so that there will be a better contact with the copper of your traces and the laminate.
What are the differences of PCB solder mask colors?
If you are up for selecting the printed boards, some parameters require to be taken into consideration. One of them is choosing the color of the PCB solder mask. Though green is the most traditional color being used, other colors like yellow, white, and black, which are also available, do not require any extra charges. As there is a wide range of colors available for the PCB solder mask, the problem is which color needs to be selected. Are there any advantages or disadvantages to choosing any color other than green? Given below is the small guide which is going to help you in choosing different solder mask color other than the standard green color:
Green
Green PCB board can relieve fatigue regarding visuals. As green does not require enhanced efforts in inspection, workers prefer to use them. Less review of green printed circuit boards leads to a less tiring job. Also, it is reported that human eye sensors are sensitive to green color. It is mentioned prior that the PCB color of green has a higher contrast, making it suitable for identifying the board traces and residues quickly.
It has also been seen that the green solder mask is superior to other solder mask colors. The green solder mask consists of different excellent properties compared to additional solder masking colors. This color produces good results with solder mask dams and plays its role in manufacturing integrated circuits.
Red
The red solder mask color tends to be bold and professional. The contrast present between planes, spaces, and traces is quite good.
On the contrary to the green printed circuit board, the contrast is lower. Any magnification is used for inspecting the board traces in case of defects. It is to be noted that silkscreen is known to stand against red background well as it cleans up the flux residues. Though red looks attractive, eye-catching and bold, green is still considered the best.
Blue
PCB color blue for the solder mask resembles the same Arduino blue color. Compared to red and green printed circuit boards, the contrast between empty spaces, planes, and traces is shallow. In blue solder mask color, magnification is considered necessary and is mandatory for inspecting manufacturing defects.
However, it is to be noted that the contrast between the solder mask and silkscreen is relatively high that is the plus point for using blue color. So, if you are using a board with the label – heavy, then the right choice, in this case, might be blue for you.
Remember that blue seems to be an excellent choice if you want to match the solder mask color with your Arduino, and you do not care about showing off-board traces.
Black
THE Black PCB color is tough to handle. The contrast between empty spaces, planes, and traces is lower than other solder mask colors, but it is non – existent. Very powerful magnification is required for the inspection of this board. Inspecting it is nothing more than a nightmare as it needs a tilted angle for casting a shadow to find traces.
Another problem with black PCB color is its heat absorption during the process of reflow. As far as cleanliness is concerned, the black solder mask needs hard efforts because the flux stains tend to be harder on the board and eventually require steps to get removed.
One of the advantages of a black solder mask is that it works well with the contrast of silkscreen. The difference between silkscreen and pads is pretty much okay. You do not need any lighting or optics to see the distinction as it is visible. Currently, only gloss black is available. Matte black solder mask color is still to be designed for prototypes.
White
If you think that a black solder mask is the hardest to handle, you have not seen white yet. Experiments show that there is nothing good about a white solder mask. White PCB color exhibits contrast that is even lowest as compared to black. When it comes to inspecting, even tilting it to light does not help in its traces' appearance. Cleaning the white printed circuit board is too hard as hints are hard to be seen. However, the silkscreen contrasts in white solder masks are the same as those found in black color, which implies that they work very well. Keeping in view other parameters, we don't recommend the white solder mask.
Industry Category