What is Solder Paste in PCB Industry with 7 Main Tips?
By:PCBBUY 08/25/2022 16:07
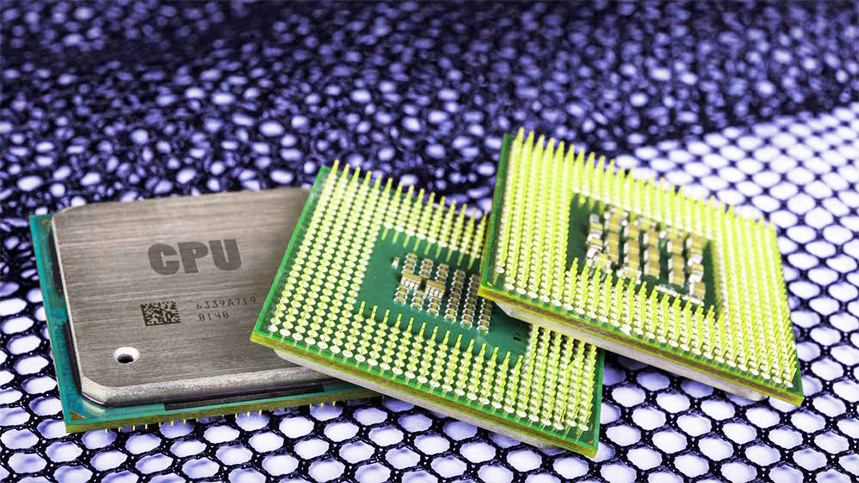
Solder is a kind of fusible metal with a lower melting point than the metal being soldered and also has specific compression capabilities with good conductivity and fast crystallization rate. When the solder melts, it can wet the metal’s surface being soldered and form the alloy layer to connect the metal. It is widely used in electronic product mounting.
During the earlier days of PCBs, components were hand soldered directly onto the board. The process was good initially and went on for a while until demands for PCBs increased with changes in the electronic market.
In this passage, please check and read the content below for more information about solder paste in PCB. If you are going to learn professional knowledge of solder paste in PCB.
What are the main types of solder paste in PCB?
During the earlier days of PCBs, components were hand soldered directly onto the board. The process was good initially and went on for a while until demands for PCBs increased with changes in the electronic market.
Solder has various categories. According to the melting point, solder can be divided into soft solder and hard solder. And the differences in composition make solder have several solder types: tin-lead solder, silver solder, copper solder, and so on. But in solder paste printing, PCB manufacturers usually use the tin-lead solder.
Tin-lead solder is the most popular in solder paste printing, and it is mainly composed of tin and lead, with some trace metal elements like Sb. Tin-lead solder is widely used in radiators and soldering of the electronic industry, and waving soldering dip and soldering in other sectors. One of the best tin-lead solders is named eutectic solder with 61.9% tin and 38.1% lead, enabling it to melt at a specific temperature but not in a temperature range. Besides, it has the lowest melting point to turn into a liquid from a solid.
Solder can also be categorized according to the type of flux used:
· Rosin based solder pastes: Rosin based pastes are made of rosin, a natural extract from pine trees. These fluxes can be cleaned if required after the soldering process using a solvent (potentially including chlorofluorocarbons).
· Water soluble flux based solder pastes: Water-soluble fluxes are made up of organic materials and glycol bases. There is a wide variety of cleaning agents for these fluxes.
· No clean solder paste: A no-clean flux is made with resins and various levels of solid residues. No-clean pastes save not only cleaning costs, but also capital expenditures and floor space. Although the no-clean flux based solder pastes sound attractive, they need a very clean assembly environment and may need an inert reflow.
How to use solder paste in PCB?
Whether you are using the solder paste in mass PCB assembly or prototype PCB assembly, you have to follow certain steps precisely. First, you have to apply the solder paste on the circuit boards. While doing this, you have to make sure that you are applying only to the areas where you will be soldering. There are different methods to achieve this. We have listed two of the most popular methods to apply solder,
Using Stencil
The first method is by using a stencil. The stencil allows you to apply solder paste only in the areas you want. Place the stencil over the board and apply the solder paste through this. You have to make sure that you apply the required amount of solder paste. If you apply too little, the joints will not be strong and break easily. On the other hand, if you apply too much, the joints will become too large. Besides, it will lead to the possibility of shorts between adjacent pads.
What are the applications of solder paste in PCB?
Electronic components were first hand soldered onto circuit boards until the wave soldering process was perfected for the mass production of PCBs. Next came the development of surface mount parts which were smaller than their thru-hole counterparts due to their lack of long leads, and eventually they became the dominant component package type used on circuit boards. The lack of thru-hole pins in surface mount parts, however, forced the development of a new method of soldering in order to hold them in place on the board until the soldering was complete. This new process is known as solder reflow, and it doesn’t use the standard pool of molten solder that the wave process uses. Instead, a sticky solder paste is used to hold the parts in place and solder them as well.
What are the methods of removing solder mask from PCB?
These factors and others must be evaluated before deciding on the most appropriate removal technique.
Grinding and Scraping
Basic hand grinding.Nothing fancy here, just lots of grunting and groaning. Often the use of a knife, scraper or pick in the hands of a skilled technician is the most controlled technique for removing solder mask from areas where you don't want it.
No special setup is needed but operator fatigue can be a drawback on large projects. Mechanical erasers, like the type a draftsman would use, can speed up the process. This technique is controlled and methodical, most commonly used when removing a thin layer of solder mask. It can be used in conjunction with other removal techniques as a final surface preparation step.
Machining and Milling
Milling machines can deliver the accuracy needed for precise solder mask removal.Would you use a milling machine to remove soldermask? Seems extreme, but can be a very effective and precise technique for removing solder mask. Since sharp cutters will be used, precision depth control is essential. The milling system will need to be fitted with a microscope for visual aid.
Carbide end mills are the most common type of cutter used. Since carbide cutters are so sharp they will tend to pull into the coating and may penetrate into the board surface. Turning the cutter in the opposite direction can be an effective technique for controlling the depth. Operator skill and experience are paramount.
Industry Category