Automotive PCB
By:PCBBUY 07/31/2021 09:18
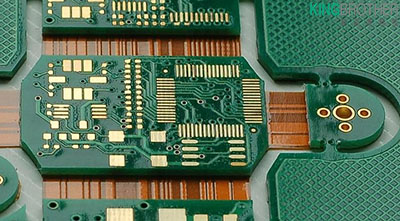
Today, no new car can run without an onboard computer — and those computers need sophisticated automotive printed circuit boards to make them run. And what are the working principles of automotive PCB? In this passage, we are going to talking about it, please check and read the content we prepare for you to learn more information.
What are the applications of PCB for automotive industry?
Because there are so many different types of electronic systems in today's cars, the types of PCBs needed for automotive electronics vary greatly. The same car may require flex PCBs, rigid PCBs and rigid-flex PCBs for different technologies. As people demand more accessories and features for their cars that are powered by electronic components, the need for automotive PCBs of varying types is only growing.
Car PCB manufacturers need to provide a wide variety of PCB options. The kinds of systems and operations that now use printed circuit boards for enhanced efficiency and safety include rear LED lights and running lights, transmission controls and comfort control units. You can also find car PCBs managing engines, entertainment systems, digital displays, radar, GPS, power relays timing systems, mirror controls and a lot more.
Not only do automotive circuit board manufacturers need to offer a variety of types of PCBs, but those who manufacture, assemble and ship printed circuit boards for the car industry must also be able to supply boards with the types of materials that can stand tough use and support long life cycles. This means high-temperature PCBs that allow the PCB to dissipate heat quickly, are crucial.
What are the advantages of PCB application for automotive industry?
To successfully solve the issue mentioned in the first paragraph, flex-rigid PCB is applied to reduce the number of connectors and solder joints, which has been conformed to for over 15 years. As flex-rigid PCB is applied in automotive systems, the following advantages can be embraced.
Obvious Improvement of Product Quality and Reliability
When applying flex-rigid PCB for automotives, connectors and soldering joints can be reduced, which can decrease the potential risks leading to electrical failures? Performance and reliability of automotive electronics control systems will proportionally go up with the reduction of connectors and soldering joints.
Cost Reduction Due to Manufacturing Steps Shrinking
As flex-rigid PCB is applied, soldering of tape cable and assembly connectors will be cut so that cost will go down. After all, all the manufacturing procedure implementation is costly.
Maintenance Simplification and Elimination
Flex-rigid PCB for automotives is composed by two or more than two pieces of rigid materials and one or more than one piece of flexible material while rigid sections are connected with each other through the application of flexible materials. Each rigid-flex circuit can be accurately packaged into a smaller package so that lots of administration and maintenance will be eliminated.
Designer and Assembly Freedom Improvement
Flex-rigid circuit designers are only responsible for rigid board layout. As for flexible section, they only need to lead the connection and are capable of freely fixing, slinging or piling, which dramatically eases design and assembly.
Up to now, two types of flex-rigid PCBs are available in current market:
Semi-flexible PCB
Flexible section of semi-flex PCB is made of thin FR-4 material, especially applicable for assembly calling for just a couple of flexibilities. Moreover, semi-flexible PCB leads to low cost.
Multi-flexible PCB
Made by polyimide (PI) material, multi-flexible PCB works agreeably on applications calling for dynamic flexibilities. Since PI layer can expands into internal rigid section of flex-rigid PCB, multi-flex circuit boards are more applicable for applications calling for gradually dynamic flexibilities.
What are the applications of multi-flexible PCB for automotive industry?
When the flexible section of flex-rigid PCB is made by flexible PI copper foil material, it belongs to multi-flexible PCB category. Belonging to a type of traditional flex-rigid PCB, multi-flexible PCB has been leveraged for more than three decades. Multi-flexible PCB features a hybrid structure laminated by rigid substrate material and flexible substrate material and interconnection between electrical conductors is achieved through electro-plated vias that will go through rigid and flexible materials. Figure 1 below demonstrates the structure of a two-layer flex-rigid circuit board.
Flexible substrate material depends on ordinary PI copper foil material and it is not only laid in flexible section but covers all the rigid section as well. However, it's equivalently effective to lay some structures of PI copper foil in selective section. Since manufacturing complexity will go up once flexible PI copper foil is used in selective section, this method is seldom used generally.
When it comes to multi-layer flexible PCBs, because adhesive along Z-axis direction features relatively high CTE (coefficient of thermal expansion), the adhesive will possibly lead to mechanical damage of electro-plated via during stress test or thermal shock test. Therefore, when automotive PCB calls for higher thermal reliability, it's obligatory to avoid using flexible substrate material and cover lay within rigid section since electro-plated vias are usually available in rigid section.
Furthermore, temperature reliability issues have to be considered in terms of adhesive and no-flowing prepreg of ordinary FR4 because FR4 prepreg is also a type of substrate material with high CTE. No-flowing prepreg of ordinary FR4 features a Tg that is 105°C that is lower than that of traditional FR4 prepreg by approximately 30°C.
Apart from FR4 material that is used as rigid substrate material, almost any type of rigid material is applicable for multi-flexible PCB, including high-Tg material, halogen-free material or even high frequency material.
Majority of flexible materials for flex-rigid PCB use PI with adhesive or PI without adhesive that performs better. Nevertheless, PEN and PET material can be also used for simple and asymmetric flex-rigid circuit board structure. LCP (liquid crystalline polymer) material can be regarded as an optimal flexible material without adhesive with high reliability design and high-speed signal transmission design. It's suggested that they should be baked prior to their applications to eliminate humidity due to high humidity absorption of PI. Multi-flex PCB with LCP as substrate material, however, doesn’t need to be baked.
Since flex-rigid PCB is concerned, multi-flex circuits can allow a couple of flexible layers to be simultaneously available. Because complex interconnections of circuit are integrated designed, it can be repeatedly manufactured, which is advantageous than cable and wire connection. Thus, characteristic impedance control signal transmission line design can be implemented to replace coaxial cable.
Industry Category