Castellated holes in PCB
By:PCBBUY 06/28/2021 17:15
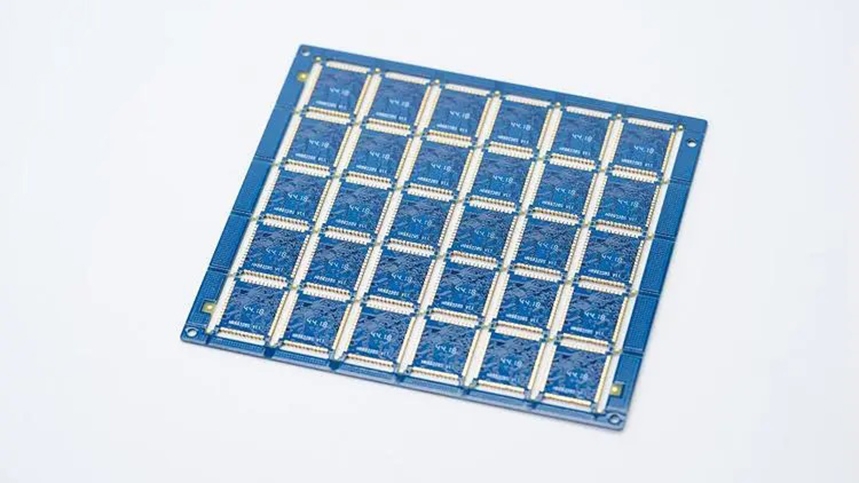
Castellated holes are indentations whose creation is in the form of semi-plated spots. Mostly, you’ll find these plated holes on the edges of printed circuit boards. Based on the application, these holes may differ in appearance. As opposed to the standard half holes, some may appear like a large or small portion of a circle that’s broken.
The half holes do serve as pads with an obvious intention. The intention is to create good connections between the module board and another board; that’s the board where the soldering will occur. As mentioned earlier, castellated holes are increasingly becoming popular.
In this passage, we provide you very detailed information of castellated holes in PCB. Please come and read the content we prepare for you below.
Why to use castellated holes?
We use castellated holes for a whole lot of different reasons. Mostly, designers use them to create printed circuit board modules. Examples of these PCB modules include Bluetooth and Wi-Fi modules. We also use castellated holes in combining two boards. Castellated holes bring about excellent wireless PCB-to-PCB links.
How are castellated holes formed?
Creating or instead of forming castellated holes is not a complicated process as such. It’s a straightforward process than you may imagine. The creation of these holes is through a normal via the method. It includes drilling and copper plating full holes in the PCB, which involves cutting the top spot in half. These will form partial or half holes on the edge of the PCB.
What are the advantages of castellated holes?
Without a doubt, castellated holes come with their advantages worth noting. They are the new thing, especially in the world of PCBs. The following are some of the merits of using castellated holes:
Easily change the pin layout of components
Castellated holes are advantageous when it comes to changing the pin layout. These holes give designers an easy time when they want to change the pin layout. Sometimes, users may have different pin layout requirements. With castellated holes, it’s relatively easy to change the pin layout.
Verify solder joint quality
Designers use castellated holes to combine two boards. When it comes to solder joint quality, castellated holes play an important role here. They are helpful as they help in validating the quality of the solder joint.
For small modules such as patch panels or Wi-Fi modules
Castellated holes are also helpful, especially for breakout boards and small modules such as Wi-Fi modules.
Create wireless PCB-to-PCB link
If there’s anything good about castellated holes, then it’s the fact that they foster wireless PCB-to-PCB links. Wireless links increase efficiency, flexibility, and bring about cost savings.
Further use in another component
Castellated holes are also advantageous as designers can use them in another component. PCBs that have castellated holes can easily mount to another PCB during production. The ease of mounting is another significant advantage that comes with castellated holes.
Easy installation
The ease of installation is an excellent reason to use castellated holes. Installing such holes on a PCB isn’t a complicated process as such. Unlike other types of holes, it’s easy to install castellated fixes.
What are the specifications of castellated holes?
When designing castellated holes, there are some design attributes to follow. Failure to comply with design attributes may end up being futile. It could affect the functionality of the board in totality. The following are what manufacturers need to follow.
Compliance with design attributes
When designing a castellated hole, compliance is necessary. Manufacturers need to comply with all the design attributes. That way, they’ll be able to manufacture boards that meet market expectations. If they happen to skip some steps, then the problem awaits them. Compliance is imperative. If there are steps, you need to follow them. Is there any necessary equipment to use? Don’t ignore them. Compliance is a significant specification when designing castellated holes. It’s as simple as that.
Size
Besides compliance with design attributes, size also matters. According to industry standards, it’s advisable to use the largest sizes. Do you have a chance to use the largest possible size? If so, then use it. But why does size matter? The size of the feature allows the use of any surface finish.
Surface finish
A surface finish is necessary for the design of a castellated hole. When designing castellated holes, surface finishing is essential. Manufacturers use surface finishes for two fundamental reasons: to ensure perfect solderability and protect the exposed copper. Of importance to note is that the surface finish that you use varies. Mostly, it depends on the intended use of your boards. The most recommended finis is ENIG. There are several types of finishes besides ENIG. Others include HASL and OSP, to mention but a few.
Pad Design
Pad design is another design attribute that you need to follow. It is advisable to use the most massive possible pad. It should be both on top and on the bottom of the place. By going for the largest possible residence, rest assured the best-castellated holes. Large pads give you room to drill holes with a lot of ease and precision. For the best results, consider using the most considerable places.
Number of Holes
Mostly, the number of holes depends on the design. Again, it’s advisable to go for the maximum number of spots. Many holes make things relatively easy for assembly. The optimum number of holes ensures easy alignment. Many holes provide that the assembly process isn’t complicated. It will be easy to see where each component will fit. Therefore, for an easy assembly process, many holes matter. The lesser the number of holes, the more difficult the PCBA assembly process will be.
ISO9001, UL, RoHS certification
Certifications matter during the design of castellated holes. Do they follow ISO9001, UL, and RoHS certification standards? Certificates are necessary here. Failure to follow certifications may see you producing faulty boards. For instance, RoHS certification calls for the best disposal methods of waste products. The castellated hole must follow UL and ISO9001 standards. They must meet criteria such as outer layer copper thickness and the minimum diameter of plated half holes.
Industry Category