What is ceramic PCB?
By:PCBBUY 06/30/2021 17:16
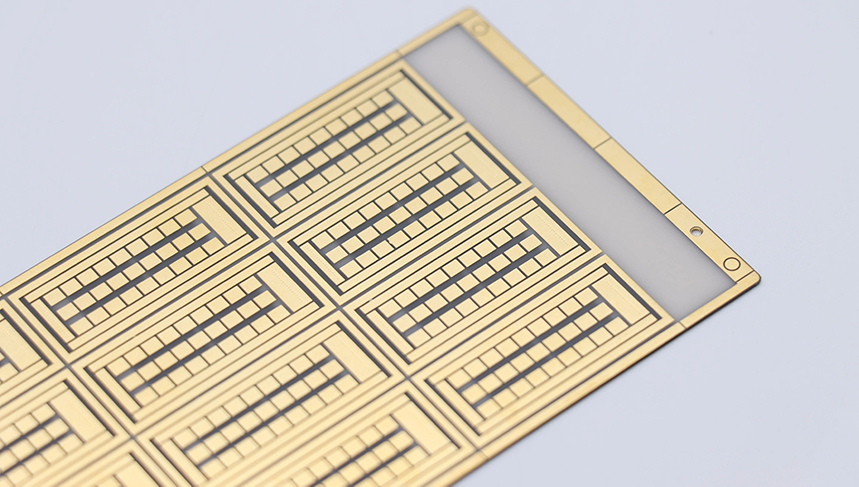
Ceramic PCB contains a thermally transitive ceramic residue and a binder. The first point to remember is to prepare the heat transmission, organic ceramic boards, at a heat transmission of between 9 to 20W/m. With this in mind, we can define a ceramic PCB as a board containing ceramic base materials. In this passage we will talk about all the details about ceramic PCB, come and read the content we prepare.
What are the types of ceramic PCB?
Alumina- you can also call it A1203 or metal baseboard. It is a type of board with dielectric thermal properties and electrically insulated components between aluminum and copper substrates. It would be best to use Alumina ceramic boards for heat dissipation purposes and general temperature maintenance and regulation.
Alumina assemblies consist of three primary layers:
· The first one is a circuit layer containing copper of about 1-10 oz wide.
· Secondly, there is an insulating layer consisting of a thermally transitive and electrically insulating substrate.
· The third layer comprises copper aluminum material.
AIN- you can also call it Aluminum Nitride. AIN is a modern commercial ceramic material. It contains elements that are reproducible and regulated for the past 20 years. AIN is an excellent alternative to alumina due to its dielectric capacities, less thermal expansion coefficient, and sound thermal transmission. Besides, it does not react with most semiconductor manufacturing chemicals.
You can use AIN boards in heat sinks, microwaves, molten metal processing machines, electronic package substrates, insulators, and others.
Why is ceramic PCB so popular?
High Thermal Expansion
The first reason why ceramic boards are so popular in the electronics sector is their excellent thermal coefficient expansion. It is good to note that the ceramic base heat transmission almost matches silicon and can act as a connection material. Besides, you can use it as an isolator. Therefore, there is maximum use for the thermal properties of ceramic boards, even in adverse conditions.
Stability
The application of ceramic brings a stable dielectric capacity, and you can modify the balance into a partial radiofrequency loss to increase your device's power. Still, despite the surface toughness, ceramic materials come with an inherent resistance against chemical erosion. Ceramic's chemical resistance can change to resistance against liquids and moisture.
Versatility
You can create several use cases to integrate a metal core board with a high thermal expansion. Besides, you can still turn the metal core into reliable conductors using the sintering technique. Therefore, the application of ceramic PCB is beneficial because of its high processing temperatures.
Durability
The ceramic board fabrication process creates durability through the use of unique properties, such as toughness. That prevents your PCB from wear and tear. So you can be confident that you will not change your PCB soon because of its slow aging capacity. Also, the high thermal resistance of ceramic PCB makes it assume a decelerated decomposition process.
Adaptability
Lastly, the use of metal cores can serve as inflexible carriers that offer mechanical stiffness. This property makes it easier to use ceramic PCBs in any state of matter because of the high resistance to corrosion and normal wear and tear.
What are the classifications of ceramic PCB?
High-Temperature Co-fired Ceramic (HTCC) PCB
You can create high-temperature co-firing by concocting aluminum oxide, plasticizer, lubricant, and solvent. Then it would help if you perform roll forming, the curtain covering, and circuit tracing on refractory surfaces, such as tungsten. After that, cut and laminate your PCB, put it in a high-temperature oven of 16000C- 17000C, and bake for 32-48 hours.
Remember to bake in a minimized gas, like hydrogen, to avoid oxidizing tungsten and molybdenum.
You can use ceramic circuit boards produced under high-temperature co-firing on small-scale PCBs and carrier circuits. It is impossible to use these methods in large-scale PCBs because of their low shrinking lenience, warpage, and moderately high tracing opposition of surfaces.
Low-Temperature Co-fired Ceramic (LTCC) Circuit Board
You can fabricate LTCC PCBs by mixing crystal glass, composite glass, and non-glass adhesive materials. Then it would help if you carried out sheet generation and circuit tracing with a highly conductive gold paste.
LTCC creates a conduit to metal paste for circuit tracing. Besides, you can complete circuit board baking by making some changes to the thick film pasting. Also, you can improve the product accuracy and shrinking capacity of your board.
Thick Film Ceramic PCB
You can repeat a thick layer of gold paste on print on your ceramic base. However, you should bake the layers at a temperature below 10000C. While this fabrication strategy is ideal for large-scale ceramic circuit board production, its use is limited because of the high gold prices.
Alternatively, you can create a multi-layered, highly concentrated copper circuit board. That is the most common ceramic circuit board in the PCB manufacturing industry right now.
Remember to bake your ceramic board in nitrogen gas to prevent the oxidation of copper. Apart from that, the dielectric paste produced by nitrogen gas is an essential ingredient of this technology.
Industry Category