PCB impedance matching
By:PCBBUY 07/20/2021 17:35
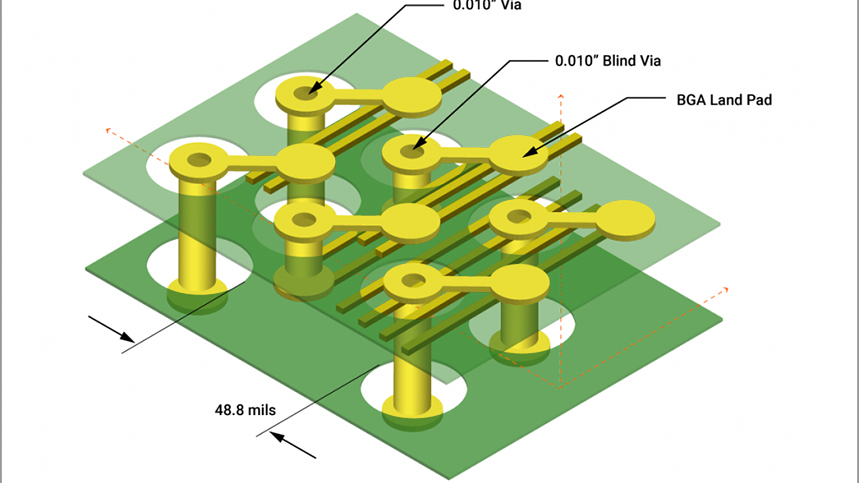
Do you know impedance matching? Impedance matching means that when source is transmitted, the load impedance must be equal to the characteristic impedance of the transmission line. In this passage, we will provide everything about impedance matching. If you are curious about this topic please check and read the content we prepare.
What is the importance of impedance matching in PCB?
Here’s a news flash: PCB design has become more complex. Whether in the consumer or industry market, high-speed and high-frequency devices have become the norm. And this is only the beginning.
When we work with these ultra-high-frequency designs, we must account for the fundamentals. As an example, impedance matching often became an afterthought for design teams working with lower and medium frequencies. However, impedance matching challenges RF and microwave circuit design because the window for error decreases as frequency increases. High speed digital circuits require very stable controlled impedances because of the impact on bit error rate and the potential for pulse distortion, reflection, and EMI.
Proper circuit operation depends on impedance matching—or the ability of the circuit to efficiently transfer signals from the source into the routing and then from the routing to the load. Impedance—if not treated correctly—has a remarkably negative impact on circuit performance. Without the proper impedance matching, reflections can exist along the path from the source to the load.
Until attenuation occurs, the signals happily propagate back and forth in the trace and interfere with the transmitted signal. Reflections and standing waves in high frequency lines mix with desired signals—and form a witch’s brew of amplitude and phase distortion. The direct results of this interference include data jitter and a reduction in the signal-to-noise ratio. As the distance from the source to load increases, standing waves cause impedance to ebb and flow.
What is the working principle of impedance matching?
Good PCB design requires attention to fundamentals. When considering the impact of impedance on a circuit, we need to consider the fundamental relationships between resistance, reactance, and impedance.
Everyone knows that a resistance opposes a steady electric current and—as a result—reduces energy. Reactance measures the opposition to current caused by a capacitance or an inductance. While a perfect resistance does not vary with frequency, the impact of changing frequencies on a capacitor or an inductor causes inductive (XL) or capacitive (XC) reactance to change with the frequency of an AC signal.
With all those things in mind, let’s make the jump to impedance. We know that impedance is the total opposite of a device or circuit to the flow of an alternating current. In addition, we also know that the impedance of a capacitor has an inversely proportional relationship to capacitance while the impedance of an inductor has a direct relationship with inductance.
How to make impedance matching?
Well-controlled impedance means that the trace impedance is constant at every point along the path on the PCB. This means that wherever the trace travels, even if it changes layers, the impedance should be the same throughout the part, from the source to the destination. We don’t have much control over the impedance in the driver or in the load but, we can control the impedance on the PCB. So, we want to have matching circuitry on the PCB that matches the impedance of the source and load. Therefore, we can ensure a consistent appearance throughout the entire path.
There are a few important design criteria that we need to consider. Keep in mind that many of the problems relating to reflections relating to EMI can be prevented by good PCB design techniques. Another crucial point is the choice of materials.
In the past, typically FR4 was specified. But, with high-speed designs, the use of the correct laminate is critical. The use of a material with a lower dielectric constant (Dk) is advisable and preferred. This not only ensures the best signal performance, but it will also minimize any signal distortion or phase jitter of the signal.
From the table, you can see that material like Isola FR408 provides a consistent dielectric constant of 3.7. So, it is essential to choose the laminate material carefully. Otherwise, you might see an inconsistency in operation between board batches: one batch of boards might work and the next batch of boards you order might not.
Another important criterion is the loss tangent or dissipation factor. This is a measure of the signal loss as the signal propagates down the transmission line on the PCB. For very high-frequency designs you would want to select the lowest loss material.
From the table, you can see that the different laminates having varying loss tangents.
So, you would need to select the material that is the most suitable for your application and specify this in your manufacturing notes. Ensure that the bare laminate used in the PCB fabrication process complies with IPC4101 grade. It is important to ensure good dielectric spacing between the copper and the laminate that it is bonded to in order to achieve a consistent electrical performance of the trace running across the PCB.
An additional point to consider in selecting the laminate material is the fiberglass weave pattern. A typical PCB core and prepreg substrates are constructed from various woven fiberglass fabrics bound together with epoxy resin. The glass and epoxy each have different Er/Dk values, resulting in an inhomogeneous medium for signal propagation. A loose weave pattern produces less uniform dielectric constants in the PCB laminate that can cause trace impedance variation and propagation skews.
The higher the frequency, the more evident this problem will be. The tighter the weave pattern, the more uniform the dielectric constant. So, it is better to practice to choose a tighter weave so the signal moves over more glass than anything else. The outcome of this will be a very consistent dielectric constant throughout the PCB.
Industry Category