Ionic contamination PCB
By:PCBBUY 08/16/2021 10:22
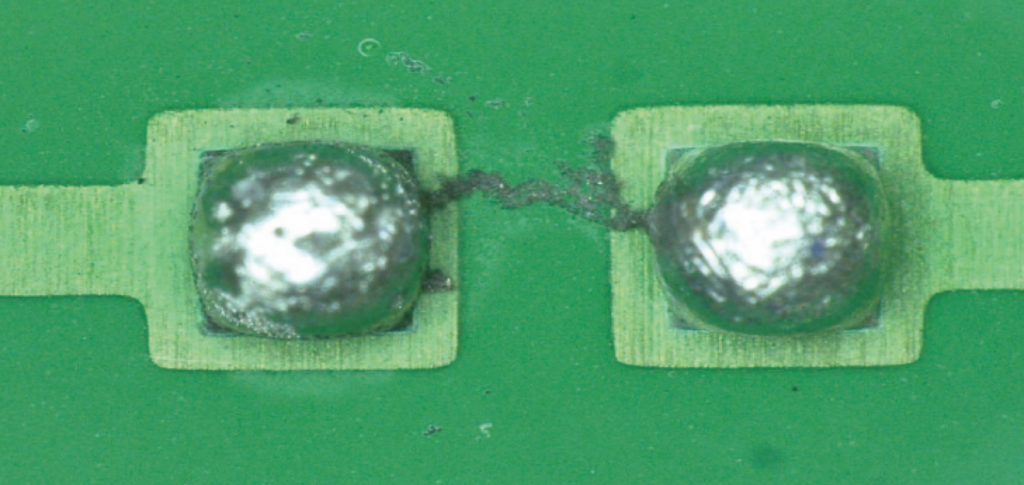
Ionic contamination issues arise due to the ionic residues left behind during PCB fabrication and assembly processes. These residues can be plastic, metal, and fiberglass granules, including salts, oils, and dust. These ionic residues have a zero net charge (the composition of positive cations and negative anions) and become charged when a PCB passes through multiple fabrication processes. During assembly, the components also carry various ionic/conductive contaminants along with cutting oils/fluids, biocides, and corrosion preventatives. How do we handle circuit boards in the production line is also a major cause of ionic contamination in a PCB.
In this article, you could learn everything about ionic contamination in PCB. Check and read the content below for more knowledge about it.
If you want to order PCB product, please check and custom your order online.
What are the sources of ionic contamination in PCB?
Ionic contamination may occur during PCB fabrication and assembly processes. During fabrication, the creation of PTHs, etching process, and drilling are responsible for the contamination. On the other hand, during assembly, flux residue in soldering, component biocides by pick and place machine, and ionic surfactants from solder preparation are responsible for PCB ionic contamination. Read the post on component placement guidelines for PCB design and assembly.
· Moisture trapped in PCB layers: Ionic contaminants in contact with moisture can increase short-circuit risk.
· Etching chemicals: Chemicals used for PCB etching purposes are highly conductive and corrosive. It is essential to neutralize/rinse them since they can be a potential cause of leakage current.
· Flux residues: Common conductive flux residues from the soldering process include various unreacted activators, binders, rheology components, and saponifiers. These residues must be removed by using solvent cleaning, say vapor degreasing, or by aqueous chemistries in the common batch.
· Inter-layer residues during drilling and plating (PTHs): Inter-layer residues generated during drilling and plating are also responsible for ionic contamination.
· Improper PCB surface cleaning: The majority of ionic contaminants come from the board itself. Before placing components over the bare board, you need to ensure that no contaminant is left from the previous production step.
What are the effects of ionic contamination in PCB?
The occurrence of ionic contamination on PCB assembly can inhibit its performance. In the production house, bare boards can carry ionic contaminants in the form of left-over flux, etching chemical, and solder material. If these residues are left on the board, major issues, like Electrochemical Migration (ECM), corroded traces, parasitic leakages, and dendritic growth, can hamper the PCB’s life-cycle. Read 8 soldering tips to avoid possible ionic contamination issues.
Electrochemical migration (ECM): Electrochemical migration is caused by the electric field in which metal gets dissolved, resulting in ion formation between two copper features. If the electric field is applied, the metal dissolves at the Anode and gets deposited to the Cathode resulting in dendrite growth. Because dendrites grow from conductive ions, they can direct PCB currents differently from what is intended, leading to short circuits. Dendrites create alternative current paths that can affect the accuracy of current measurements in a PCB.
Corrosion: Usually, PCBs corrode due to their material. Ionic contamination can corrode the entire PCB in a much shorter time. When ionic residue comes in contact with moisture, the short-circuit risk increases. The corroding metal flakes off, overlooking the chemical properties needed for the PCB product to operate correctly. Selecting apt PCB material and laminates helping with ionic contamination issues.
Ionic contamination alone is not responsible for the above consequences; moisture and environmental exposure are also. That is why PCBs are baked to eliminate moisture before starting any new process. The ionic contamination level needs to be controlled during the manufacturing of circuit boards by adopting a process control tool. This tool ensures that the individual production process steps (e.g., surface-mount or through-hole) are performed in a controlled manner to achieve a manageable ionic contamination level.
What is text of ionic contamination in PCB?
Bad quality control during PCB fabrication, component placement, and a sub-standard final cleaning are some of the major issues responsible for ionic contamination. It is crucial to identify, control, and mitigate such issues. This can be done with proper ionic contamination testing equipment and analysis. ROSE testing, ion extraction, and ion chromatography are some of the well-known methods. Sometimes, humidity validation testing is also performed at the beginning of the production.
To ensure the life-span of the PCB, testing of the bare board for ionic contamination prior to assembly reduces the risk of defects caused by contaminants. Ionic contamination testing is performed to detect ionic residues resulting from the fabrication and soldering steps. Let’s have a detailed analysis of cleanliness testing methods for the determination of ionic contamination.
What are the benefits of measurement of ionic contamination in PCB?
The PCB sample dipped in an extraction solution releases ions with an extraction liquid, which is determined by a conductance detector. The final result is calculated by an ionic contamination meter with the help of software. The measurement value is analyzed with reference to sodium chloride.
Benefits:
· The cleanliness measurement is ideal for post soldering evaluation as per official regulation. Also, it verifies surface quality prior to PCB coating and other chemical processes.
· The testing also performs quantitative determination of the ion contaminates for PCBs in µg/cm² equivalent NaCl.
· The cleanliness measurement continuously monitors contamination of quality through regular sample-based measurement.
Industry Category