What is the Chemical Solution Used in PCB Etching?
By:PCBBUY 10/12/2021 09:37
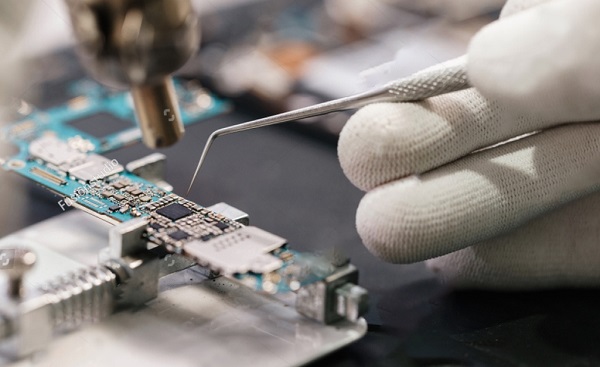
In PCB Making concentrated Hydrochloric Acid OR Concentrated Nitric Acid is used for etching process. This will remove unwanted copper. In the modern process, these unwanted removed copper is collected in a drum and is recycled for copper plating.
In this passage, we will focus on the chemical solution used in PCB etching. Please check and read to learn more information about chemical solution used in PCB. let’ s start it!
What are the types of chemical solution used in PCB etching?
The etch rate is stable. It is particularly suitable for producing the correct topography and cleanliness for hot air levelling. It is non foaming and sprayable.
150 MG copper etchant
It is a proven etchant, specially designed for etching copper in the manufacturing of printed circuit boards during mass production. MG Etchant chemicals are based on ammoniac compounds in highly selected proportions. It can be used in spray or immersion application.
1932 Nickel cleaner
It is an aquoues solution of acidic chemical components used to restore the solderability of nickel plated and nickel alloy surfaces. Tarnish can be removed by immersing the part for 15-20 seconds at room temperature. Immersion time can be reduced if the solution is warmed up to 74°C . After treatment the part should be thoroughly cleaned through hot water spray, followed by cold or hot water immersion.
6401 Solder stripper
It is an acid based stripper designed to be used for stripping tin, tin / lead and lead from PCBs. It is extremely economical and will hold in excess of 15 oz. per gal. without replenishment. It contains a unique stabilizer, copper inhibitor system which reduces base metal etching during stripping.
6810 Resist stripper
It is a concentrated alkaline solution formulated specially to remove alkaline soluble dry films and silk screen printing inks from printed circuits boards. It contains no organic solvents and can be used in dip tanks and spray equipment.
8200 De-foamer
It is an alkaline, non-silicon de-foamer (foam suppressant) used in conjunction with all alkaline resist stripper and developer solutions. It is recommended for use in conveyorised spray machines. It operates over a wide temperature range, which allows it to be used where necessary to control excessive foaming
6109 Lacoquer
It is a fast drying resinous system designed to protect printed circuit boards and other electronic parts against oxidation. It protects and preserves the solderability of metallic surfaces and leaves a coating of resin that is completely compatible with almost all rosin base fluxes.
What are the chemicals of PCB development?
Along with cleaners, there are chemicals used during PCB development that should be noted.
Replenisher
During the assembly process, a printed circuit board encounters wear and tear. Using a replenisher on it will help make the PCB work normally during development.
Copper can get stripped in the assembly process, and a replenisher essentially neutralizes, brightens, and restores the balance between components of the developer.
Cleanser PCB manufacturing chemicals
In the PCB development process, cleansers are used to apply a dry photoresistant film. This is essential for PCBs because it gives the board the ability to resist etching or damage from solvents when exposed to light.
Antifoams
Antifoams are used to reduce the natural foam produced by sprays and other foamy chemicals used in the PCB manufacturing process. These are mostly used during development and stripping.
How to process PCB etching with chemicals?
Acidic etching process
The acidic method is used to etch off the inner layers in a rigid PCB. This method involves chemical solvents like Ferric chloride (FeCl3) OR Cupric Chloride (CuCl2). The acidic method is more precise and cheaper but time-consuming, compared to the alkaline method. This method is implemented for the inner layers because the acid doesn’t react with the photoresist and doesn’t damage the required part. Also, the undercuts are minimum in this method.
Undercuts are the lateral erosion of the etched material below the protective tin/lead layer. When the solution hits the copper, it attacks the copper and leaves behind the tracks that are protected. The tracks are protected with either a plated etch resist or a photo imaged resist. At the track edge, there is always some amount of copper removed under the resist, this is known as an undercut.
Cupric chloride etching
Cupric chloride is the most widely used etchant since it accurately etches off smaller features. The cupric chloride process also provides a constant etch rate and continuous regeneration, comparatively at a lower cost.
The maximum etching rate from the cupric chloride system is obtained from a combination of cupric chloride-sodium chloride-HCl systems. This combo gives a maximum etching rate of 55s for 1oz copper at 130°F. Hence, this type of etching is used to etch fine line inner layers
Industry Category