What is the Guideline of PCB Stack Up Analysis and Design?
By:PCBBUY 04/28/2022 10:32
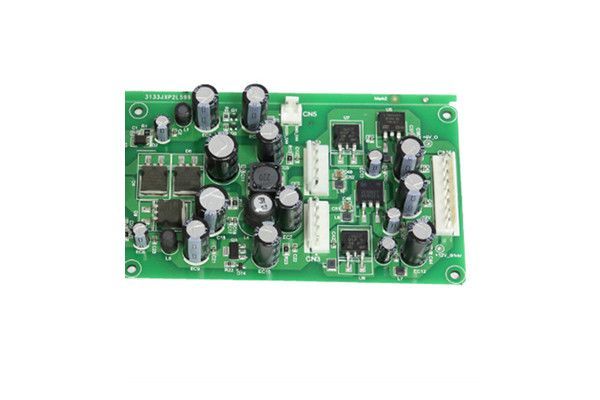
Printed circuit boards designed for aerospace and military applications shall have a high degree of reliability and robustness, without offering any margin for error. Challenging applications, such as space missions, require an accurate understanding of how printed circuits must be designed and created to ensure a very long period of operation, in often very extreme operating conditions. Unlike most traditional PCBs, printed circuit boards used in aerospace applications are subjected to extreme environmental conditions, radiation, chemicals, contaminants, and more.
If you are searching for the basic information about PCB stack up, please check and read the content below for more professional knowledge.
What are the different layers in a multilayer PCB?
A stack-up primarily consists of metal foil, prepreg, and copper-clad laminate (core).
· Metal foil: Copper is the most commonly used metal foil in PCB construction.
· Prepreg: It is an interwoven glass cloth impregnated in epoxy resin. The resin is left semi-cured.
· Copper-clad laminate: Single or multiple plies of prepreg bonded together along with the top and bottom copper foil makes a copper-clad laminate. This is also known as the core.
How to process PCB stack up design?
Building a digital twin, virtual model of the 2.5D/3D heterogeneous assembly provides a comprehensive representation of the full system comprising multiple devices and substrates. The digital twin enables automated verification of heterogeneous assemblies beginning with substrate-level design rule checking (DRC) and expanding into layout versus schematic (LVS), layout versus layout (LVL), parasitic extraction, stress and thermal analysis, and, finally, test.
One of the primary benefits of the digital twin approach is that it serves as the golden reference to drive complete physical and electrical verification at every level of the design hierarchy. That eliminates using multiple, static spreadsheets to represent pin and connectivity information, replacing them with a full, system-level netlist in Verilog format.
The preservation and reuse of original data, such as a device’s Verilog description, is key. The biggest risk comes when translation or conversion occurs, such as with a schematic or spreadsheet. If this is done, the “digital thread” is immediately broken, and the risk for connectivity errors skyrockets.
Why to process PCB stack up design?
Most circuit boards today have some elements of high-speed circuitry involved with them, meaning that the signal integrity of the board will be a primary consideration. High-speed transmission lines usually require an adjacent ground plane if routed on the board’s surface in what is known as a microstrip layer configuration. If the high-speed transmission lines are routed on internal layers sandwiched between two ground planes, this is known instead as a stripline configuration. These layer configurations will provide an excellent reference plane for clear signal return paths, eliminating the most prolific cause of electromagnetic interference (EMI) in circuit boards. The ground planes also help shield the high-speed transmission lines from incoming interference and radiate their own interference.
Sensitive high-speed signals require added space to protect them from other forms of noise and interference:
Trace separation
When high-speed traces are too close to each other, one signal may overwhelm the other and impose its signal characteristics on it instead. This imposition may cause the victim signal to mimic the aggressor signal instead of producing its expected behavior.
Impedance matching
Going through different areas of the board can change the characteristic impedance on high-speed signals. This change can cause signal reflections which could distort the original signal and interrupt the intended function of the circuit.
How to Select the right trace width in PCB layout?
The trace geometry (thickness and width) is of fundamental importance to ensure the correct operation of the circuit in all environmental and load conditions. The traces of a PCB are used to carry electrical signals and, therefore, must have a width compatible with the current passing through them. The designer must determine the minimum width of each trace in order to avoid dangerous overheating of the board; this parameter directly affects the routing process, as it reduces the space available on the PCB. The minimum width must therefore be determined before placing the traces, using one of the several calculator tools, also available online. By entering thickness, current and maximum acceptable temperature rise, these tools return the minimum trace width.
PCB trace thickness is measured in ounces of copper, corresponding to the thickness that would be obtained by uniformly distributing an ounce of copper over an area of one square foot. This thickness is 1.4 thousandths of an inch. Standard PCBs use 1- or 2-ounce thicknesses of copper, but for high current applications this can be as high as 6 ounces. If the available space is not an issue, the advice is to use traces with a width greater than the minimum, thus improving the thermal management and reliability of the board. Also keep in mind that the traces on the outer layers achieve a better heat exchange and, therefore, may have a smaller width.
Industry Category