What is the use of Prepreg in PCB?
By:PCBBUY 06/26/2021 16:54
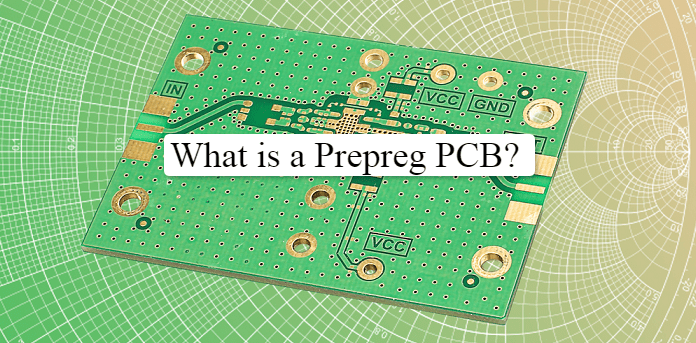
Prepreg is a dielectric material that designers pack in between a copper and a Core or between two Cores in a PCB to provide the required insulation. Prepreg is simply an insulation layer. Since it can bind a copper foil and a Core, it is safe to refer to it as a binding material. Users can also modify Prepreg to their needs as peculiar dielectric materials. They can also use a chemical process to transform a certain part of a Prepreg into a conductive region through the combination of specific catalysts and additives.
In this passage, we will lead you to learn everything about Prepreg in PCB. Please follow us to read the content we prepare.
What is a Prepreg PCB?
Prepreg is a dielectric material that designers pack in between a copper and a Core or between two Cores in a PCB to provide the required insulation. Prepreg is simply an insulation layer. Since it can bind a copper foil and a Core, it is safe to refer to it as a binding material. Users can also modify Prepreg to their needs as peculiar dielectric materials. They can also use a chemical process to transform a certain part of a Prepreg into a conductive region through the combination of specific catalysts and additives.
Prepreg is a part of untreated FR4. The FR4 is utilized in the PCB manufacturing process, where it performs the function of binding the etched cores together. It can also be useful in gluing the copper foil with the etched core. Thus, the Prepreg in a PCB can vary in thickness in accordance with the height of the etched boards. If we compare Prepreg vs. core, the latter is FR4 coated with copper either side and is made in a core factory. But the Prepreg is sort of virgin FR4 that gels itself into the structure of a PCB board.
What is the Prepreg PCB preparation process? A typical Prepreg process involves:
· Reinforcing with resins which can be either thermoplastic or thermoset.
· Removal of excess resin
· Preparation of curing with high and low-temperature settings
What is the use of Prepreg in PCB?
Advanced fabricating experts use prepregs to achieve the purpose of minimizing the weight of the part they are preparing. The low weight parts are needed where the devices or products are supposed to work against any flow or resistance. For example, the aerospace needs lightweight parts; so, does the racing and sporting materials. The pressure vehicles and a few commercial products also fare well in terms of cost-efficiency when they weigh less. It becomes possible to achieve with prepreg. Fabricators need to have experience in processes like vacuum bagging and hand layup to use prepreg in their work.
Primary industries where Prepreg finds its application are:
· Construction
· Defense and ballistic
· Marine
· Transportation
· Infrastructure
· Wind energy/power and a few others.
What are the applications of Prepreg?
Multi-layered boards
What holds the layers together is the multi-layered board of Prepreg. The user will need to fuse them when they stack all the board’s layers by exposing it to high temperatures. They will then have the similarity between the overall board thicknesses with the Prepreg thickness. When the designers use the Prepreg on a multi-layered board, it must have specific characteristics. The new surface must not have excessive resin powder, cracks, foreign matter, defects, stains, or oil. It must have a smooth feel and look.
Complex PCBs
Engineers will probably have a more complex Prepreg if they have a complex PCB. As a result, they can only achieve the needed thickness for the board and Prepreg to use different types of Prepreg.
Why is Prepreg so important?
Prepreg is an integral part of the PCB manufacturing process because:
· These are easy to apply and to learn to work with. Getting accustomed to it does not require much technical expertise. With regular use, even a less tech-savvy person can become familiar with Prepreg. Thus, the cost of labor does not shoot up when the prepregs are used.
· PCB Prepreg material is very less messy as compared to the wet style layups. Thus, these contribute to waste management during the manufacturing process better, followed in PCB making units.
· These are available in various types, such as Kevlar, fiberglass, and hybrid as well. Thus, you name the purpose, and there is a suitable Prepreg available for it.
· To top it all, the possibility of reducing the weight of the device becomes higher, which is quite essential in some particular types of equipment required for working in unique conditions.
It is worth learning that the PCB Prepreg material displays a better shelf life when these are stored in colder temperatures. It is because its resin part remains deactivated, allowing it to remain intact and usable beyond a chosen timeframe.
Industry Category