Vapor phase reflow
By:PCBBUY 07/13/2021 09:06
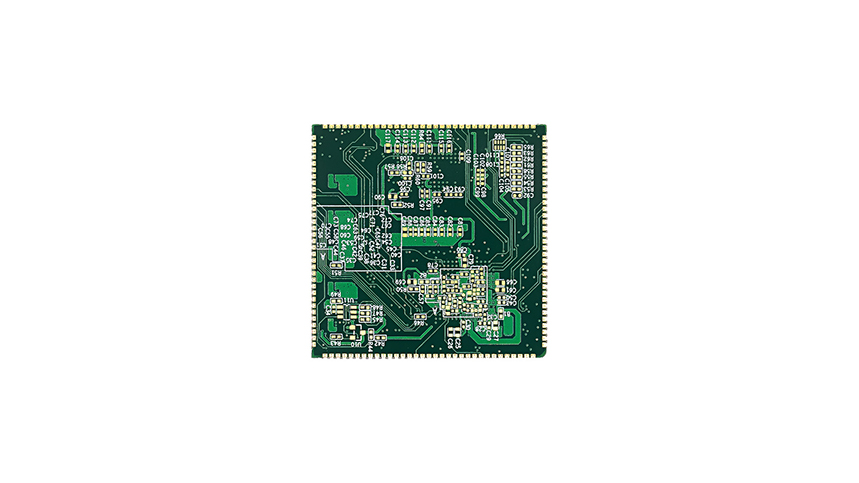
Vapor phase reflow refers to an advanced PCB soldering technology that uses an inert liquid with a high boiling point. This technology has, in recent years, gained massive popularity among large scale PCB assemblers. To solder electronic components to PCBs, manufacturers usually need high temperatures. It’s a complex process that has become even more challenging as electronic components become smaller.
Vapor phase reflow soldering ensures that the PCB board and its members don't face temperatures higher than necessary. For that reason, parts don't overheat. This soldering process provides the ideal wetting of the details. Moreover, the entire soldering process takes place within an inert atmosphere. In the end, PCB assemblers get the highest possible PCB soldering results.
In this passage we will focus on the details knowledge about vapor phase reflow and please read the content we prepare.
Why we use vapor phase reflux?
Vapor phase reflow if quickly replacing other soldering technologies in the market. There are many reasons for this development. We look at two of them in this section.
The Welding Problems Faced
The vast majority of manufacturers now opt for leadless solder bases. These bases need manufacturers to use even higher temperatures to melt the solder effectively. As a result, the risk of damage to the electronic units due to overheating is higher.
Vapor phase reflow technology helps counter this problem by virtually eliminating temperature fluctuations, topography, and board layout.
PCB Circuit Board Components
PCB circuits need require parts of different masses, which makes the soldering process a complicated one. That’s because the heat these components store varies significantly based depending on their groups. The result is that there’s uneven heat distribution, which could lead to warping of the PCBs. To reduce these issues, PCB assemblers and designers opt for vapor phase reflow.
What is the working principle of vapor phase reflux?
To understand how vapor phase reflow works, we need to look at three different things:
· Heat adjustment
· Level adjustment
· Void formation
Heat Adjustment
Heat adjustment involves PCB engineers adjusting the temperature gradients in vapor phase reflow equipment. They do so by regulating the power that goes to the equipment’s heating elements. As more power goes to the heaters, there’s more vapor production. It means more heat transfer to the PCB assembly, even though the liquid’s boiling point remains the same.
As we hinted earlier, the vapor phase reflow takes place in an atmosphere that's entire oxygen-free. This atmosphere reduces the likelihood of oxide formation. It also improves wetting.
Usually, there's a slight delay in the creation and the subsistence of vapors. Thus, there's no creation of sophisticated temperature profiles. To solve this challenge, manufacturers developed soft vapor phase (SVP) machines.
Level Adjustment
One of the top benefits of SVP machines is that they allow you to control immediate temperature gradients. During the SVP process, the PCB's temperature rises as it moves deeper into the vapor blanket.
To achieve the ideal preheating of the PCB board, hold it at a specific depth. Note that as you increase the center, the board will move towards liquidus temperature. Assemblers and designers can create just about any thermal profile they want. They do so by automatically preselecting and controlling the soldering time.
As soon as you're through soldering, the SVP machine will move the board up from the depths of the vapor blanket to the vapor boundary. Here, the board's temperature lowers. You can then lift the board out of the vapor to allow it to cool down.
Usually, the SVP process doesn't need any extra mechanisms to stop overheating. That's because the liquid's boiling point limits the PCB's peak temperature.
Void Formation
The void formation is inevitable with vapor phase reflow. Voids can compromise or diminish both the thermal and electrical conductivity of a solder joint.
So, how do engineers mitigate void formation? One effective way is through a vacuum controlled procedure that outgasses these voids. When you reduce the pressure over a liquid, its boiling point reduces, and vice versa. Using a vacuum can extend the time above liquidus by 30 seconds or so, reducing existing voids and stopping new ones from forming. Of course, you should conduct void reduction when solder joints are liquids.
Industry Category