What the Essential Considerations Are of Reflow PCB?
By:PCBBUY 10/27/2023 16:07
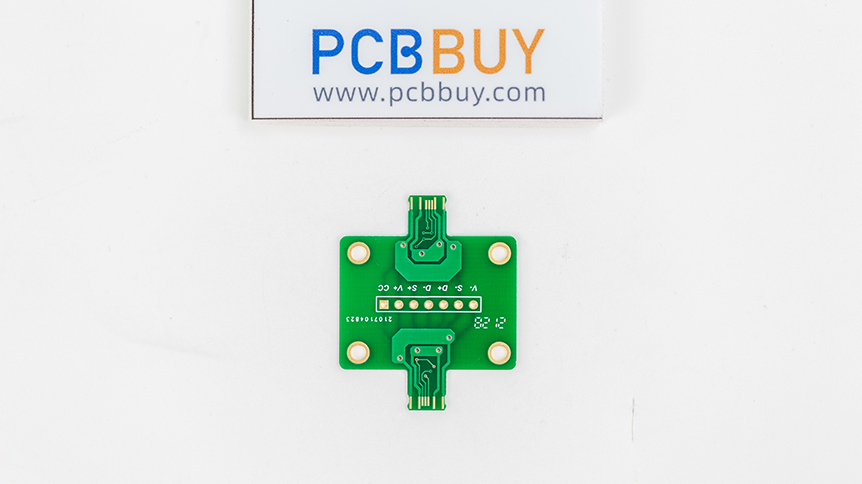
How do you know which type of soldering to use and when? It may depend on a variety of factors, such as pad shapes, the amount of time you have, component orientations, type of printed circuit board and more. In some ways, wave soldering is more complex. Issues like board temperature and time the board spends in the solder wave need careful monitoring. Failure to create the right wave soldering environment is much more likely to lead to board defects.
In this passage, if you are looking for more information about reflow PCB, please check and read the content below for professional knowledge.
What the Essential Considerations Are of Reflow PCB?
Reflow soldering is the most popular and widely used method of connecting surface mount technology (SMT) components to a printed circuit board (PCB) . The process is focusing on creating acceptable solder joints by pre-heated components, which provides the opportunity to melt the solder without causing damage by overheating.
In order to create an appropriate reflow profile, thermocouples are connected to a simple assembly (often using high-temperature solder), in different locations to measure the range of temperatures across the printed circuit board.
Proheat- During this phase of the process the printed circuit board, components and solder are heated to a specific dwell or soak temperature, with the main aspect, which is not to be heated too quickly (usually no more than +2 degrees a second). Fast heating could cause component defects such as solder paste slattering or cracks.
Soak- This is the part of the project in which it ensured that the components have reached the required temperature before entering the next reflow stage. The soaks last no more than 60 to 120 seconds, depending on the type of assembly.
Reflow- In this general stage, the temperature in the oven is increased above the melting point of the solder paste, forming it into liquid. The time in which the solder is held above the melting point temperature is important to ensure that the "wetting" occurs between the printed board and the components. The time is about 30 to 60 seconds and it should not exceed to avoid the creation of brittle solder joints.
Another thing that you should know is that the peak of the temperature has to be strictly controlled as many of the components could fail if they are exposed to excessive heat. On the other hand, it is important for the temperature to be high enough in order to achieve the desired results. If the reflow profile provides insufficient heat, it will result in bad solder joints which is one of the most common defects.
Cooling- It is not healthy to heat the assembly fast, here would be the same. Make sure to never cool down the assembly too rapidly as it could lead to malfunctions. The recommendation here is to keep the rate of cooling above 3 degrees a second.
What are the basic solder components?
After the printing of a circuit board, the first step in reflow soldering is the application of the solder to the board. The paste must be applied only to the relevant areas of the circuit board. In this stage, accuracy is key.
For this reason, a paste mask is essential when applying solder. The paste mask is a stencil to be placed on the PCB. (You can read more about the solder paste printing process here) It indicates the areas for solder application. Some mass production systems utilize both a solder mask and paste machine for a more automated process.
After the direct application of solder to the specified areas of the board, it is time to put the components in place. This requires the use of a pick and place machine. The technology removes the need for a laborious and lengthy manual process. Pick and place machines allow for rapid, highly precise application of the electrical components to the circuit board in a repeatable process.
Following placement, the natural adhesive of the solder paste temporarily holds the components in place. This allows for the secure transfer of the components to the oven.
Reflow soldering VS wave soldering
As mentioned already, an infrared lamp is used to heat the air and melt the solder in the reflow soldering technique. The board is passed through a tunnel or reflow oven where it is heated in a controlled manner. In this, you apply the solder paste only over the areas (contact pads) where you want to assemble the electronic components. Failure to create the right wave soldering environment is much more likely to lead to board defects. You don’t need to be nearly as concerned about controlling the environment when you’re utilizing reflow soldering to fabricate your printed circuit boards. However, even with that being the case, wave soldering tends to be faster and cheaper than reflow soldering. In more than a few cases, it’s the only practical way to solder a board.
Reflow soldering is typically used in smaller-scale manufacturing products that don’t require a method amenable to fast, cheap mass production. Keep in mind that you may be able to use both reflow soldering and wave soldering for certain situations. You might reflow solder parts on one side and then wave solder them on the other. Also, you can always manually solder or hand solder PCB components, but this will rarely be a good approach if you have access to one of the mechanical methods of soldering. Manual soldering would only be an alternative to reflow soldering, but reflow soldering is still far superior.
Industry Category