Why PCB Board Is Green in Colour & What Are the Advantages of It?
By:PCBBUY 12/29/2021 09:24
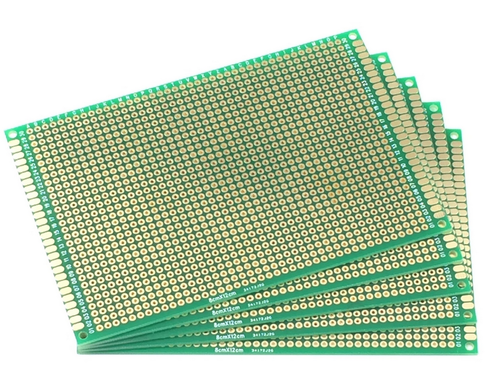
PCB’s do not have to be green. Different colors can be useful to distinguish different PCBs or to customize them. ABL Circuits offer colored printed circuit boards. Green, Blue, Black, Red and White are available for standard production or we can produce bespoke colours or corporate colors as required.
Why PCB is usually green?In this passage, we are preparing all the details about PCB colors. If you are searching for more professional knowledge please check and read the content below.
What are the main reasons for choosing green PCB?
Green can relieve visual fatigue and aid in inspections
In the early days, due to technological restrictions, quality inspections relied on workers manually checking the boards with their bare eyes. Squinting at tiny circuits all days is tiring work, but neurologists and psychologists agree that the wavelength of green light has relaxing effects on the body and can reduce fatigue. Additionally, they have found that the sensors in human eyes, or cones, are most sensitive to green light. Therefore, the contrast is greater between the circuit traces, pads, silkscreen printing and empty spaces. Just by observing the boards from the outside, one can easily identify defects in the outer layers. Compare the below images of green boards to other colors such as blue, yellow or even black and white. With higher contrast, errors are easier to spot.
The military’s role in PCB development
Some believe that the green color was chosen and made standard because of the military. The United States military studied PCB colors and found that green was the most effective color, especially when they tested them in adverse situations.
Because of their tests, the military decided that green printed circuit boards would be the norm. And, the PCB manufacturers who supplied circuit boards to the military had several non-military customers, too. Businesses didn’t need to make them in different colors, because most PCBs aren’t seen by anyone other than the manufacturers.
They are cheaper than other material
Solder mask is created using silkscreen technique. This method involves a large blob of oil applied on a screen mesh with the circuit board underneath. After application. the circuit board is then removed to dry up, and the next circuit board will be placed under the mesh.
Because manufacturers of all types are concerned with costs, green PCBs became the norm. In a nutshell, green is a less expensive color to use than the others that are available.
In a scenario where a company need different colour solder mask, the excess solder mask oil initially used must be removed and the silkscreen must be washed before applying new colour. Another solution to save such hassle will be the installation of another silkscreen station for other colors. However, the chemicals will be wasted if it is not often used. Time & efficiency will also be impaired.
For contrast
A white silk screened ident is often printed on the component side of rigid boards. Green is the best contrast for this layer, to allow for human readable text. In fact, this theory was closest to the mark according to Peter Skippings who was one of the joint founder of Artetch Circuits in the late 1960s.
The conventional PCBs that Peter’s team made were screen printed, etched, printed with green solder resist and then roller tinned to the exposed copper pads on the board. The solder resist protected the copper tracks on the PCB from the heat of the roller tinning process.
Peter said that green was the only colour available, and it provided the heat resistance needed, which is why that was all they used. So it seems there isn’t a single reason why PCBs are green, but like most products it’s often the colour used for mass production which proves to be the most cost effective.
Is PCB necessary to be green?
While most PCBs are green, they do not have to be in that color. While making a PCB, the color does not have any impact on the performance of the board and the device it will power. But, the resolution of it changes. This means the solder mask is more difficult to see on different colored boards. Along with green, the other more commonly used colors include red, blue, black, and white. But, all the colors of the rainbow do show up on some circuit boards.
The different colors are often coded to special parts of the device. For example, in computers, motherboards are generally coded green. This helps people who work on computers quickly identify the most important PCB on their computers. Other boards for smaller tasks are often different colors to show what they do.
Circuit boards of different colors are not as easy to work with when compared to green ones. For example, black circuit boards struggle with the heat that is used to press them together.; it often gets overheated. White boards are difficult to read. Red is easy to use because so many colors stand out on it. Blue also works well and is easy on the eyes.
Industry Category