Why PCB Conformal Coatings Are Important?
By:PCBBUY 03/20/2024 16:33
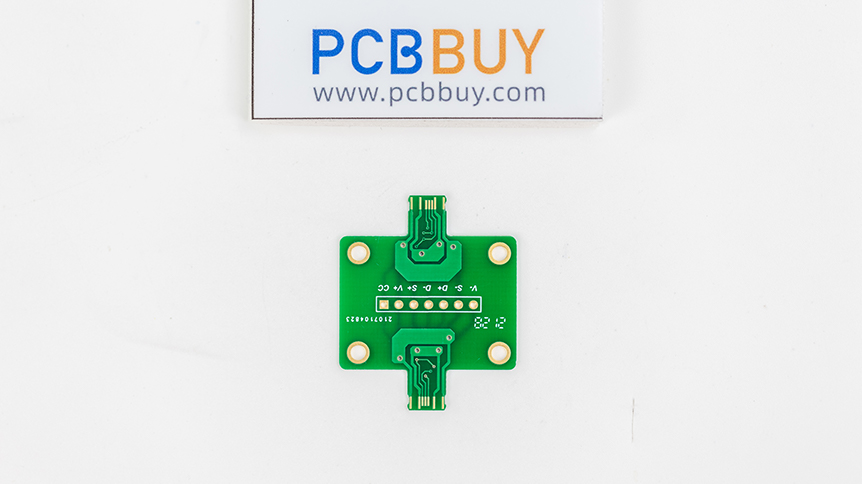
Depending on its applicability, a printed circuit board can suffer from elements such as dust, moisture, and extreme temperatures, and as such, coatings are necessary. A surface is more of a protective non-conductive layer applied to a PCB and its parts to protect it from damage. But what are the benefits associated with PCB coating? Why consider PCB coating?
Then do you know how to remove PCB coating? In this passage, we are providing all the information of PCB coating removal. Please check and read the content below.
Why PCB Conformal Coatings Are Important?
Moisture
Moisture is the commonest and destructive factor causing damage to PCB boards. Too much moisture will dramatically decrease insulation resistance and the value of Q, accelerate high-speed decomposition, and get conductors eroded. It's common for us to see metal parts that have been assembled on PCB board is covered with a layer of green copper just because chemical action just takes place between copper and water vapor and oxygen.
Pollutant
It's hardly believe that hundreds of pollutants can be found on the surface of printed circuit boards when conformal coating isn't applied on them. Those pollutants are equivalently hazardous to the reliability and functionality of PCBs. Similar with moisture or high humidity, pollutants contaminated on circuit boards can also lead to bad results such as electronic failure, conductor erosion, or even irretrievable shortcuts. Majority of contaminants left on circuit boards derive from residues during manufacturing process including flux, solvent parting agent, clipped wire and marking ink. Moreover, some contaminants result from manual residue when boards are touched by operating people including human oil, finger print, cosmetics and food residue. Plus, lots of pollutants even come from operating environment, such as salt spray, sand soil, fuel, acid and other erosive vapor and mould.
What are types of conformal coating of PCB?
There are five types of conformal coatings with four primary methods in which they are applied. All coatings can be sprayed by hand or spray booth.
Some coatings can be applied manually using a brushing method however this requires an experienced hand. Dipping is a very common application method which is also performed manually or by a machine but is limited to slow-curing chemicals.
Lastly, a robotic coating can be used for all coatings with proper tooling if you have the provided equipment or use a conformal coating company.
· Acrylic Resins (AR)
· Smooth glossy finish.
· Good for long-term defense against moisture.
· Usually applied by being brushed, sprayed, or dipped manually or by machine.
· Epoxy Resins (ER)
· Smooth hard surface.
· Good against moisture, temperature, and abrasion.
· Resists chipping, peeling, or cracking.
· Usually applied by being brushed, sprayed, or dipped manually or by machine.
· Silicone Resins (SR)
· When cured, is rubbery and pliable.
· Excellent against humidity, corrosion resistance, and extremely high temperatures.
· Usually applied by being brushed, sprayed, or dipped manually or by machine
· Polyurethane Resins (UR)
· Uniform contour of PCB, can be thick or thin.
· Approved by FDA in medical applications
· Urethane is excellent at chemical resistance and good for applications needing protection from prolonged chemical exposure.
· Usually applied by being brushed, sprayed, or dipped manually or by machine.
How to remove PCB coating?
Although chemical solvents are used for coating removal more often than any other process, no single solvent methodology exists. Implemented essentially for most liquid process films – acrylic, silicone, urethane — coating material is the prime determinant of solvent choice. Spot-basis coating removal by brushing or swabbing the local area with controlled solvent-application can be very successful. For faster results, immersion of assemblies in large solvent-quantities is suggested. The solvent butyrolactone is effective for chemical removal of most acrylic resin coatings.
Chemical removal via methylene chloride or hydrocarbon-based solvents is recommended for silicone; they are far less likely to damage PCBs, components, metals and plastics than other solvents. For urethane, solvents composed of activators of ethylene glycol ether-base/alkaline or methanol-base/alkaline remove urethane conformal coatings efficiently. Chemical removal methods are generally ineffective for epoxy. Except in rare cases, solvent removal is futile for chemically-inert parylene. Tetrahydrofuran (THF) is the only chemical solvent that consistently removes parylene from assembly substrates; the limited chemical options remaining are highly specialized and seldom applied.
Micro abrasive blasting (abrasion) is inexpensive AND environmentally friendly. Assignment-specific formulas of abrasive media and inert gas/dry air are projected at the coated surface by a tiny nozzle attached to a stylus. Grounding devices dispel electrostatic potential; coating debris are removed from the substrate by filtration. Project focus can be as minute as an individual test node or as large an entire PCB. Unique among removal methods, micro-abrasion is recommended for acrylic, epoxy, parylene, silicone and urethane conformal films.
Often used to remove coating from specific components – connectors or similar highly-selective assembly mechanisms — oxygen-based plasma is versatile. Its fine-scaled procedures can be expanded, to strip conformal films from entire PCBs. This method is effective for parylene removal, and has been successful with wet coatings.
Industry Category