Why PCB Insulation is Important in Manufacturing Industry?
By:PCBBUY 05/19/2023 15:12
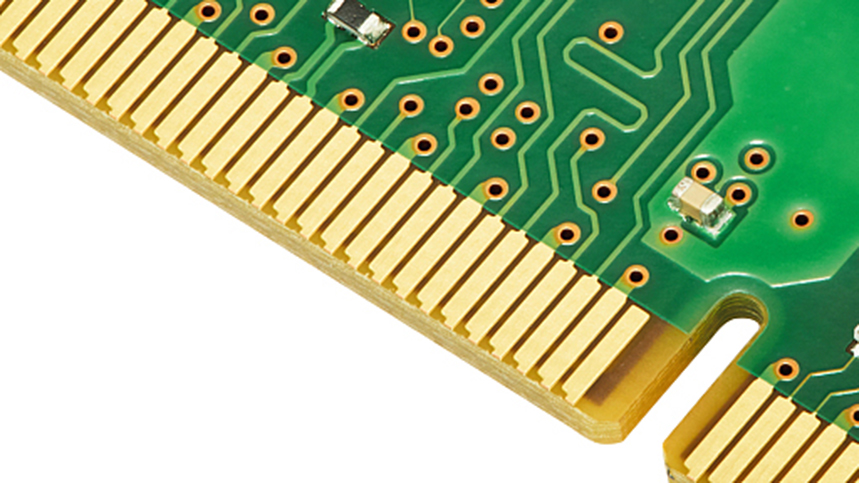
Common PCB insulation materials are often formed into non-conductive substrates, which meld together in several layers to allow electrical currents to travel correctly throughout the board. Simpler PCBs may be single-sided or single-layered. Complex PCBs, such as those used in high-speed digital communication, may be comprised of over twenty layers.
In this passage, we are providing all the basic information of PCB insulation and the importance. If you are searching for more knowledge of PCB insulation, please check and read the content below for all the details about it.
What are the functions of PCB insulation?
· Minimize or eliminate signal interference between adjacent layers.
· Maintain adhesion during the assembly temperature cycling.
· Aid in thermal distribution during assembly.
· Aid in signal and power integrity.
Why PCB Insulation Is Important?
As you can see, PCB or printed circuit board is one of the most important parts of the electronic devices and gadgets these days. Most of the devices in your house come with this board in it. The printed circuit board allows the electronic devices to function properly and correctly. Without the presence of these boards, it is impossible to operate the phones, computers and televisions. In order to operate this board, electricity plays a vital role. Without it, the PCB will not be able to function properly.
The printed circuit board contains some copper wiring which are printed and everyone knows that copper is a natural conductor of heat and electricity. But these electrical components can get quite hazardous if they are not properly insulted or enclosed in a case which is non-conductive in nature. If not, then it can become quite hot. Thus, PCB insulation is very important in order to prevent the corrosion of the copper elements. The insulation is also important to reduce any kind of accidental contacts with the conductive material.
With the proper insulation, you can keep your printed circuit board from getting overheated. Overheating can cause severe damage and even bursting into flames. This can be quite dangerous and damaging for the board as well as the device. Some of the main objectives of insulation for printed circuit board are:
What are the PCB insulation materials?
Common PCB insulation materials are often formed into non-conductive substrates, which meld together in several layers to allow electrical currents to travel correctly throughout the board. Simpler PCBs may be single-sided or single-layered. Complex PCBs, such as those used in high-speed digital communication, may be comprised of over twenty layers.
A PCB insulation calculator can help you determine creepage distances and clearance, which will factor into the exact type and quantity of insulation materials you may need. Creepage distance is the shortest distance between conductive parts, and clearance refers to elements separated by air, not substrate. Understanding creepage distance and clearance is essential for calculating PCB insulation.
To better understand PCB insulation and insulation materials, let’s explore the five most common forms of PCB insulation materials.
FR-2
FR-2 is a low-grade, flame-resistant laminate substrate option. It is a composite material created from paper and plasticized phenol resin, making it both lightweight and durable. Single-sided circuit boards often employ this material. FR-2 is halogen-free, non-hydrophobic, and can be punched or milled easily. One of the least expensive choices of PCB insulation, FR-2 is a common choice for companies producing single-use consumer electronics.
FR-4
FR-4 is a high-grade, flame-resistant laminate substrate option. It is a composite material created from woven fiberglass, and it is often used in the manufacture of double-sided and multilayer PCBs. FR-4 can withstand higher temperatures and physical pressure than FR-2. It is also an affordable material, making it a popular choice for manufacturers of high-end consumer electronics. FR-4 is not as quickly mechanically processed and requires tungsten carbide tools to be milled, punched, or machined.
RF
RF substrates are designed to allow PCBs to function within applications that use high-powered radio frequencies and microwaves. RF substrates are most often used on PCBs installed in military electronics, aeronautical electronics, and aerospace electronics. Though, it is important to note that there are a few consumer electronics that contain this type of substrate. The plastics that comprise a typical RF substrate do not create a tremendous amount of insulation, though they do perform well when tasked with generating strong electrical currents. RF and microwave PCBs typically have very few layers, sometimes only one or two.
Industry Category