Why To Prevent Corrosion on PCB?
By:PCBBUY 12/21/2023 15:36
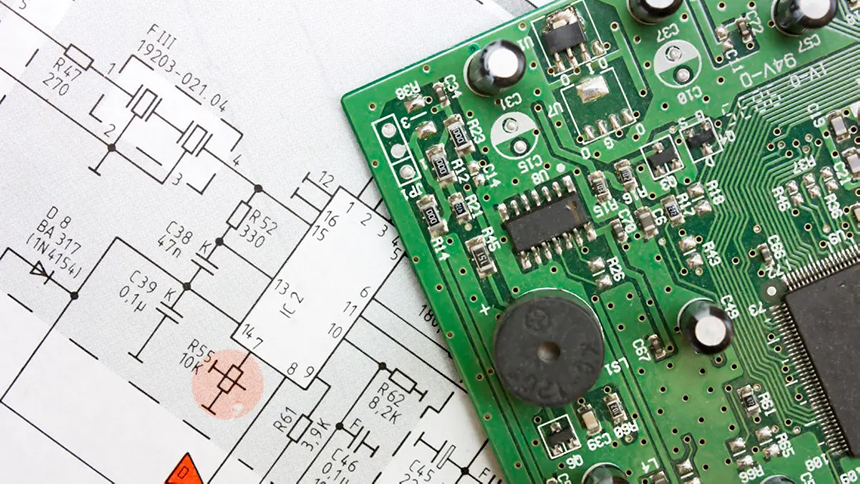
What people don’t realize is that simply drying out your phone is not a solution. Water ingress can cause the device to short out, killing the phone immediately. But if the device does not break, creep corrosion will accumulate over time. Electronic devices start corroding as soon as they get wet, and they continue corrode as they are operated. This is typically what causes devices to fail.
Do you know the methods of Prevent Corrosion on PCB? If you are searching for more information of corrosion on PCB, please check and read the content below for more information.
Why To Prevent Corrosion on PCB?
Corrosion is the gradual breakdown of material, usually metal, by a chemical reaction with its environment. The most common form of corrosion occurs with you combine metal with water and oxygen, creating iron oxide (or what is more commonly known as rust). This reaction occurs when you combine these elements together for an extended period of time.
What people don’t realize is that simply drying out your phone is not a solution. Water ingress can cause the device to short out, killing the phone immediately. But if the device does not break, creep corrosion will accumulate over time. Electronic devices start corroding as soon as they get wet, and they continue corrode as they are operated. This is typically what causes devices to fail.
If you ever took chemistry classes in college, you probably remember that different materials and plating will corrode at different rates when exposed to the environment. Moisture in humid air, air pollutants (atmospheric corrosion), or direct contact with water or an electrolyte solution like gatorade can cause electrical traces in a printed circuit board to start corroding. There are a number of corrosion mechanisms that degrade device performance or cause it to fail outright.
What are the types of corrosion on PCB?
There are several causes to why the metal in your circuit boards corrodes. Some include:
Atmospheric: This is the most standard type of corrosion. Metal is exposed to moisture, which contains oxygen, causing a reaction where the metal ions bond with the oxygen atoms and create an oxide. Copper experiences atmospheric corrosion very easily, which is not a problem for copper plumbing because corroded copper retains its mechanical properties. It does not, however, retain its electrical conductivity, so this is a big problem for circuit boards. Galvanic:
Galvanic corrosion occurs when different types of metals are in the presence of an electrolyte. In these circumstances, the more resistant metal will actually corrode faster than the baser metal it’s in contact with, so when gold is in contact with tin, for example, the gold will corrode much faster than usual.
Electrolytic: In this type of metal degradation, adjacent traces experience dendrite growth when ionic contaminated moisture infects the electrical voltage between them, creating metal slivers that result in a short circuit.
Fretting: With fretting corrosion, the action of closing solder-plated switches creates a wiping action that removes the surface oxide layer, allowing the layer beneath to oxidize. Eventually, excessive rust builds up and prevents the switch from activating.
How do you prevent corrosion on a PCB?
Different metals have varying levels of corrosion risk. While they can all corrode eventually, copper and other base metals corrode much easier and faster than noble metals and some alloys. The latter of these are more expensive, so many professionals will stick to the more common metals, making it necessary to know how to prevent corrosion on PCBs and not harm their circuit boards.
One simple way to prevent corrosion on a circuit board is by placing a coating over the exposed copper areas. There are many different types of coatings, including epoxy coatings, aerosol spray coatings, and solder masks.
You should also do your best to avoid humidity surrounding your PCBs. Try to keep them in an environment that isn’t affected by humidity. You can use a humidifier in the same room to help with this. But knowing how to stop corrosion on PCBs is the first step to success.
How to repair corrosion on a PCB?
Removing corrosion from a PCB is not a sure fire thing. Once it happens the board is compromised. However, you can clean it off and hope for the best. Make sure to remove all power from the board and isolate as best as possible. To do this you can take a cotton swab with a cleaning solution such as isopropyl alcohol, baking soda and water, or even vinegar to clean it.
Washing Water
Washing water refers to chemical industrial cleaning agent potion used to clean the flux and rosin on the surface of PCB circuit board after soldering. The traditional method for cleaning printed circuit boards is to use organic solvents. A mixed organic solvent consisting of CFC-113 and a small amount of ethanol (or isopropanol) has a good ability to clean the residue of rosin flux, but because of CFC- 113 has a destructive effect on the atmospheric ozone layer and has been banned in 2013. The optional non-ODS cleaning processes include water-based cleaning, semi-water-based cleaning, and solvent cleaning.
Baking Soda
The alkalinity and abrasiveness of baking soda make it an ideal cleaner for PCB corrosion. It can effectively remove all corroded areas without causing any damage to the PCB itself.
Industry Category