Why is There a PCB Shortage & How to Solve it?
By:PCBBUY 01/04/2022 09:41
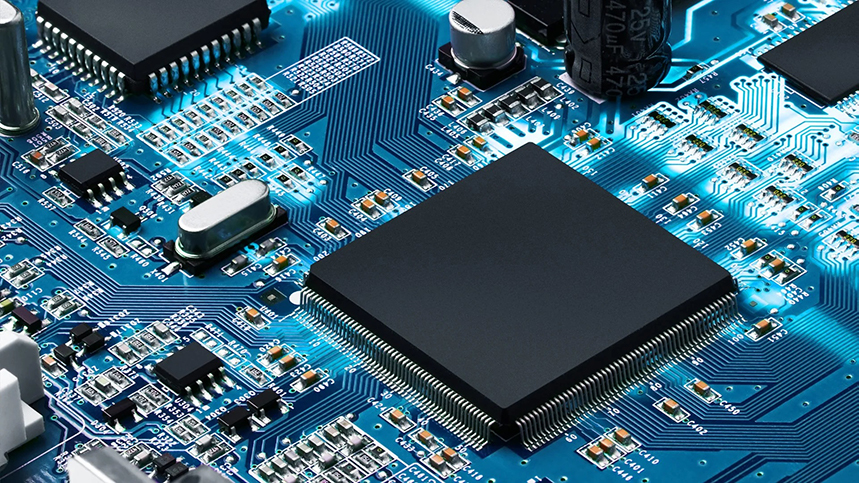
The pandemic, partnered with a higher-than-anticipated demand for new hardware, created conditions for a shortage of vital printed circuit board raw materials. Specifically, COVID-19 related quarantine mandates created a shortfall in foil copper supplies used to make PCBs. Demand for copper foil is increasing from both PCB and battery production for e-mobility leading to an upward price pressure for copper foils as post lockdown pent-up demand starts to exceed capacity. Lead times are stretching and prices are increasing.
This negatively impacts PCB manufacturers and their supply base. Demand for aluminum in metal-backed printed circuit boards (MPCB) is also increasing, exacerbating already strained supplies. In this passage, we are providing all the information of PCB shortage.
What’s the result of these shortages?
In short, global printed circuit board supply shortages are causing widespread manufacturing delays in several industries, including automotive and electronics. The automotive industry has been the most visibly impacted by this shortage. Many major car brands announced that they needed to reduce production expectations and acknowledged that they anticipate falling short of 2021 production targets. For the electronics sector, it was previously reported that PCB components are running more than fifty weeks behind the original schedule. Pricing for components has also gone up substantially as a result of these shortages.
What are the challenges of PCB shortage?
It’s convenient to blame the COVID-19 pandemic as the source of the semiconductor industry’s problems, and people aren’t wrong to do so. Consider these industry changes and difficulties due to the pandemic:
· Changing needs and requirements: With personal and professional habits changing due to the pandemic, consumer spending was drastically impacted. This change in spending forced businesses to alter the products they produced. The automobile industry is a prime example. Carmakers reduced the number of new vehicles they produced in response to people driving less, which cut back on the number of electronics they required for production. Without electronic components to build for cars, the semiconductor industry switched to producing parts for other electronic devices.
· The market demand for new electronics: Sales of new electronics accelerated as people were sheltered in their homes for work and study. The semiconductor industry had to ramp up production to supply components for the following:
· Computers, networking, and display equipment for the home office
· Laptops, tablets, and educational systems for virtual classrooms at home
· Cell phones and communication systems for connecting homes together
· Television and gaming systems for home entertainment
· Cameras and other smart home devices for home security
How to deal with the PCB shortage as manufacture?
As COVID-19 disrupts offshore supply chains, electronic manufacturers should consider switching to procurement from onshore partners.
The longer a supply chain is, the more fragile and dependent it will be, so working with dependable suppliers is crucial. Switching to an onshore manufacturer will shorten and increase the strength of your supply chain.
Before partnering with an onshore electronics manufacturer, discuss how the pandemic has impacted them and how they are handling the semiconductor shortage.
A seasoned onshore manufacturing company will be able to recognize shortages early on and help you eliminate future production issues. An onshore electronics manufacturing service (EMS) provider can also help you design your PCB with variants in mind so that if a component is unavailable, your final product won’t be jeopardized. This flexibility is needed because any component can suddenly go out of stock or be held up in the supply chain.
The tariffs China and the U.S. placed on each other forced American companies that outsourced from China to find another way to get parts and continue with their production. Some companies turned to onshore solutions, but these companies still saw shipment and production delays at the pandemic’s peak.
The shortage of electronics components caused prices to jump tremendously across the industry.
Many companies were able to stay afloat during COVID-19 thanks to relief packages, but now that the U.S. has no plans to provide such aid any further, companies will need to be resourceful when procuring parts for PCB manufacturing.
To continue with production, talk to your electronics manufacturer and see if there are any drop-in alternatives. Drop-in alternatives are components that can be used to replace unavailable components. The replacement parts must have the same pinout and land pattern.
Industry Category