Why to Choose Kapton PCB Material in Manufacturing Process?
By:PCBBUY 12/09/2021 09:18
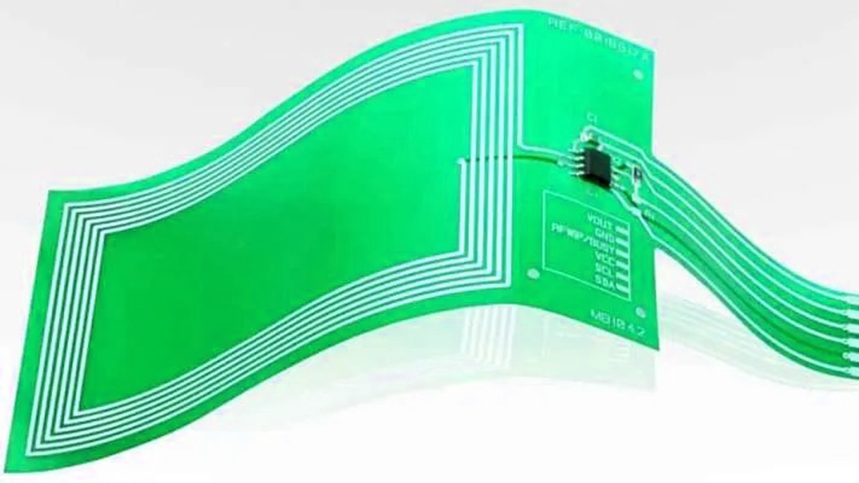
Kapton is prized by manufacturers all across the globe for its ability to maintain its stability in the most extreme temperatures. This thin film is incredibly tough, able to withstand temps as high as 400 degrees Celsius (752 degree Fahrenheit). It’s no wonder that you can find Kapton in thermal blankets used on spaceships and satellites which have to pass through the earth’s atmosphere. Kapton is also regularly used as insulation on electrical wiring.
In this passage, if you are looking for more information of Kapton PCB in the whole manufacturing process, please check and read the content below for more professional knowledge.
Why to choose Kapton PCB material?
Kapton can be thought of more like a printed circuit board (PCB) with very thin/flexible (.005” thick material). The conductive traces are copper just like a PCB and processed similarly. Many companies offer and design Kapton circuits as an option, however most companies do not process it in-house. Kapton circuits require a special chemical processing, similar to PCB boards – it is a subtractive process (chemical intensive, not eco-friendly), in comparison silver printing is an additive process and better for the environment.
Both Kapton/copper and polyester/printed silver can be covered with a dielectric cover layer for protection of the circuit traces from oxidation, abrasion, or electrical shorts. While the two materials do have their similarities, they also have their differences; Kapton offers some advantages over printed silver circuits:
· Kapton is the base circuit material and offers good insulation properties and heat resistance
· Copper trace widths can be very narrow while the electrical resistance remains For instance, with printed silver, a typical switch resistance spec is 100 ohms max, while these same traces might be less than 10 ohms for Kapton/copper circuits. This means that a copper circuit can conduct the same electricity in a narrower trace width than silver can.
· The copper can be gold plated (and typically is), this provides low contact resistance for metal domes during life cycling
· Any components, LED’s, resistors, capacitors, integrated circuit (IC) chips, etc. can be soldered on Kapton/copper circuits. This is where Kapton really performs like a traditional printed circuit board – the high temperature resistance of the film allows the high temperatures of reflow soldering without damage. Electrical circuit functionality is greatly increased using Kapton (consider it equal to a PCB board but more flexible.) This cannot easily be done with silver circuits because the polyester film cannot tolerate the time and heat requirements of soldering. As a result component attachment processes such as conductive epoxy and encapsulation can be used to mount certain components to polyester.
· It is possible to etch much narrower trace widths/spaces with Kapton/copper than it is to screen print on silver circuits – although the gap is closing – Kapton with gold plating circuit tails can be made to fit ZIF connectors down to 0.2mm trace pitch traces while printed silver is just now approaching applications for ZIF connectors down to 0.5mm trace pitch. At 0.5mm trace pitch it is challenging to screen print carbon over the silver at the tail ends for protection.
What are the features of Kapton PCB material?
Kapton can be used on extremely high and low-temperature ranges. Kapton can maintain extraordinary mechanical, electrical, and physical properties in the wide range of -452 to 752 Fahrenheit. Kapton is a good resister and an effective insulator so it is a good choice for demanding application industries such as electric applications and aerospace. Below is mentioned some useful features if Kapton:
· It is highly effective
· It is highly stable in high ranges of temperatures
· It can tolerate extreme levels of both heat and cold
· It possesses excellent mechanical, physical, and electric properties which make it an excellent choice for demanding industries
· It is well suited for diverse applications
· It has excellent radiation and chemical resistance
· It provides reliable labeling
What are the advantages Kapton PCB material?
Kapton printed circuits are serving in many fields. The flexibility of the Kapton circuit boards is the basic requirement for many electronic devices. Following are the advantages of using Kapton printed circuit boards:
· Kapton printed boards are designed in such a way that they can meet higher and smaller density mountain designs and can improve flexibility. Kapton helps in decreasing the assembly process and reliability can be increased through it. Miniaturization and signals flowing in electric devices can only be improved by Kapton printed circuit boards.
· There is a thick polyimide film on the substrate of the circuit including a copper foil. For thin and light circuits or compact and complex devices, the solution is ranging through single base Kapton circuit to multilayer or 3D Kapton printed circuit boards. The additional mechanical stability and strength can be enhanced by reinforcing the base material of the circuit. In this way, the strength of the circuit would also be increased.
· As clear from the name, the Kapton circuit is having flexibility so it can be bend, move, and torsion effect also. And the conductivity would not be damaged by this flexibility.
Industry Category