Why we need PCB V-cut for manufacturing?
By:PCBBUY 05/26/2023 14:49
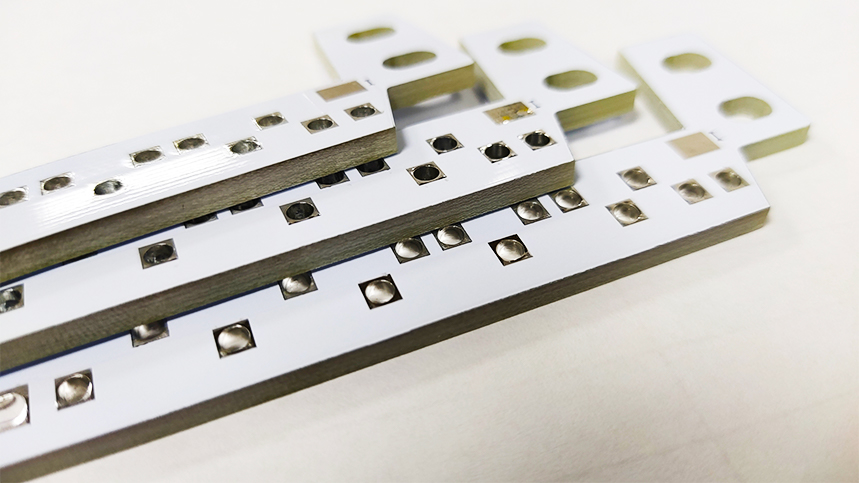
The printed circuit board is also known as a PCB array. Although a single board that incorporates multifold separate boards. When put together, the panel is then severed one by one into single PCBs. However, the V cut could also be manually broken. Though, manual breakage is not recommended to avoid the PCB from bending.
If you are going to learn more knowledge about PCB V-cut, you can check and read the content below for more information of PCB V-cut below in this passage.
Why we need PCB V-cut for manufacturing?
Cut is mainly used when you need to group a set of circuit boards to make the assembly process more efficient. The idea and the purpose behind cut the PCBs are to create a solid structure for the assembly process that allows you to apply minimal pressure and separate the assembled boards.
The purpose of PCB V-cut is to make more efficient use of board space and reduce manufacturing costs by making many of the same PCB on one manufactured board by providing a final board format that is more friendly for the manufacturer. You can also put two or more related circuits on the same assembly for more efficient sub-assembly later on.
Proper cut helps the customer, engineer, or technician separate the sub-PCBs that have been scored apart from the single manufactured PCB without breakage. This effectively turns on PCB into many.
Being able to V-score PCB provides excellent value to you or someone that has hired you. Being able to V-score a circuit board not only saves time and money, but it also lets you easily separate parts from a completed assembly.
What are the rules of PCB V-cut?
Scoring (also known as v-cut) is used for mechanical pre-separation of circuit boards. A V-shaped breaking line is formed in the circuit board with a precision cutting tool. Please observe the following rules:
· The circuit boards spacing in the layout is 0.0mm
· Scoring lines must be straight; horizontal and vertical lines are possible, and always run from circuit board outer edge to circuit board outer edge
· Jump scoring is possible. Please note that the roller blade of the scoring machine requires an entry and exit path. Therefore, the starting or end point of a scoring line must not be directly adjacent to the next circuit board, a distance of 15mm is necessary
· PCBs down to a minimum thickness of 0.8mm (on request 0.5mm as special production) can be scored. Where applicable, scoring is done one-sided.
· If you separate the panel by hand, we recommend scoring only down to a minimum PCB thickness of 1mm for handling reasons.
What are the terms of PCB V-cut?
· Rails: also referred to waste tabs or border. Rails are not the parts of the PCB board, but the extra material around your PCB(s) to form a panel. Rail is usually applied for enforce the mechanical stability of the panel and allows non-functional material outside the PCB which can be used for clamping the panel during assembly.
· Fiducials: Fiducials are little target registration marks that etched on panel rails or inside of PCBs on top and/or bottom copper layers, and allow the vision system of the SMT machines to recognize where the PCB is at, and where the SMD components are placed.
· Tooling Holes: Tooling holes in the four corners of the PCB panel rails be used by the PCB fabricators for aligning the board during drilling, routing and E-test fixtures; the assemblers for alignment with stencils during solder pate printing, and for alignment with SMT carriers, PCBA testing fixtures, or final enclosure assembly (mating with small moulded plastic posts).
What are the common problems of PCB V-cut?
However, PCB comes with varying issues. It could be that parts get away easily which cracks the board or measurement issue. These issues could rise as a result of a bad singular procedure and wrong measurement.
Stiff resistance in detaching parts from the assembled design could be as a result of how it was earlier fixed. Therefore, many times, manual separation has not been a good option to detach the assembled parts. The effect of this creates more problems for the board. Forcefully detaching parts from the assemblies could lead to components breaking. Fiberglass could break as well the resin base laminate.
To reduce or put an end to some of the issues faced by this process, observing a few rules will be helpful
· Spacing on the board layout must be at 0.0mm
· The V cut lines have to be straight, although the vertical and horizontal line is viable.
· The lines should run from one PCB outer edge to another
· Separation done by hand should be on a PCB density of 1 mm
· Jump cutting is feasible as well.
Industry Category