what is electric iron pcb?
By:PCBBUY 01/31/2024 23:57
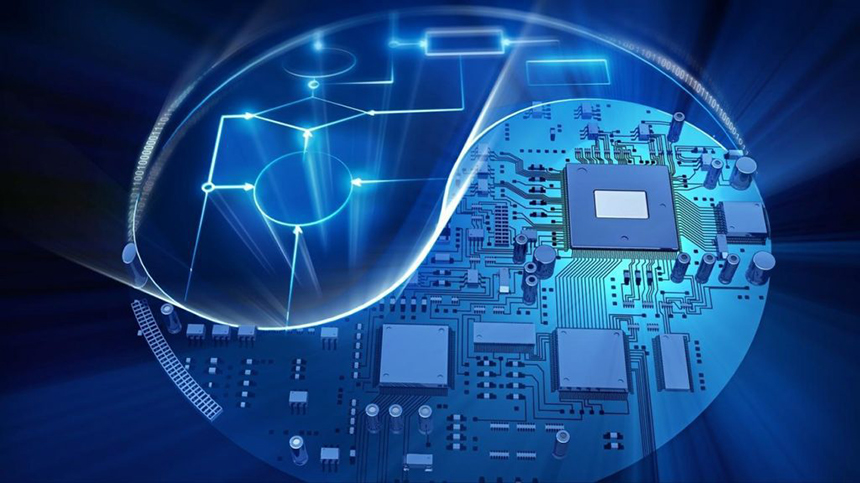
The core components of an iron PCB typically include a microprocessor, power circuit, heating element control circuit, temperature sensor, etc. Its working principle is based on the microprocessor processing input signals, driving the heating element, and controlling the ironing temperature to achieve the purpose of ironing clothes.
Structural Components of Iron PCB
The structural components of the iron PCB primarily include:
Microprocessor: Used to receive and analyze sensor signals, controlling the operation of the heating element based on preset algorithms and programs. The microprocessor typically incorporates modules such as ADC (Analog-to-Digital Converter) and PWM (Pulse Width Modulation) to achieve high-precision control and regulation.
Power Circuit: Converts input AC power to DC power, providing stable power to the entire PCB. The power circuit usually includes rectifiers, filters, and stabilizers.
Heating Element Control Circuit: Drives the operation of the heating element, commonly using power transistors or relays to control the on-off state of the heating element.
Temperature Sensor: Detects the ironing temperature, converts the detected signal into an electrical signal, and transmits it to the microprocessor. The microprocessor adjusts the operation of the heating element based on the sensor signal to maintain the appropriate ironing temperature.
Human-Machine Interface Circuit: Connects external devices like display panels and operation buttons. This circuit enables users to control and set the iron's functions easily. The interface circuit usually includes keypad input circuits, LED display driver circuits, etc.
Main Functions of Iron PCB
Temperature Control: The microprocessor adjusts the heating element's operation based on temperature signals from the temperature sensor, maintaining the appropriate ironing temperature to prevent clothes from being over-ironed or under-ironed.
Human-Machine Interaction: Through the human-machine interface circuit connected to external devices like display panels and operation buttons, users can set ironing programs, choose temperature settings, check ironing status, etc., providing a simple and user-friendly control experience.
Safety Protection: The iron PCB includes safety features such as overload protection and overheat protection to prevent damage to the heating element and ensure user safety. In case of anomalies, the PCB automatically cuts off power or issues an alarm.
Auto Power Off: Some irons automatically cut off power after a certain period of inactivity or when reaching a set idle time to save energy and protect the PCB. This function is typically implemented through a timer or the microprocessor's timer.
Steam Function Control: Some high-end irons feature a steam ironing function. Through PCB control, steam output quantity and pressure can be precisely adjusted to achieve the best ironing effect.
LED Status Display: LEDs are used to display the iron's working status, such as ironing temperature, operating mode, etc., allowing users to intuitively understand the ironing process.
Noise Control: By controlling the operation of the motor and heating element, the iron PCB can effectively reduce noise during the ironing process, improving user comfort.
Manufacturing Process of Iron PCB
The manufacturing process of iron PCB involves the following key steps:
Circuit Design and Wiring: Based on product requirements, design the circuit and wiring to determine component positions and connections.
PCB Fabrication: Print and process circuit patterns on copper-clad boards according to the designed circuit diagram, forming multi-layered composite PCBs.
Component Soldering: Solder electronic components onto the PCB according to design specifications to ensure proper arrangement and connections.
Testing and Debugging: Test and debug the assembled PCB to ensure all functions work correctly. Testing includes electrical performance testing, visual inspection, and functional testing.
Assembly and Packaging: Assemble and package PCBs that pass the tests, making them usable components for irons. The assembly process includes securing the PCB in the appropriate position, connecting the motor, heating element, sensors, etc., and conducting necessary adjustments and tests.
Development Trends of Iron PCB
With continuous technological development, iron PCBs are evolving. Some development trends include:
Smart Technology: By integrating more advanced artificial intelligence technologies and algorithms, iron PCBs will achieve more intelligent ironing control and management. For example, using machine learning technology to automatically identify clothing types and materials, intelligently adjust ironing temperature and pressure; implementing IoT technology for remote control and data sharing.
Multifunctional Integration: Future iron PCBs will trend towards multifunctional integration, such as integrating dust removal, sterilization functions, providing more comprehensive clothing care services; integrating voice recognition and synthesis technology for voice control and interaction; integrating wireless charging technology for a convenient charging experience.
Energy Efficiency and Environmental Protection: With increased global environmental awareness, iron PCBs will focus more on energy-efficient and environmentally friendly designs. This may involve using efficient heating elements, optimizing energy utilization efficiency; adopting eco-friendly materials and recyclable designs; and implementing measures to reduce energy consumption and emissions.
Industry Category