What Are the 5 Essential Effects of PCB Microvia in PCBA Process?
By:PCBBUY 08/25/2023 14:13
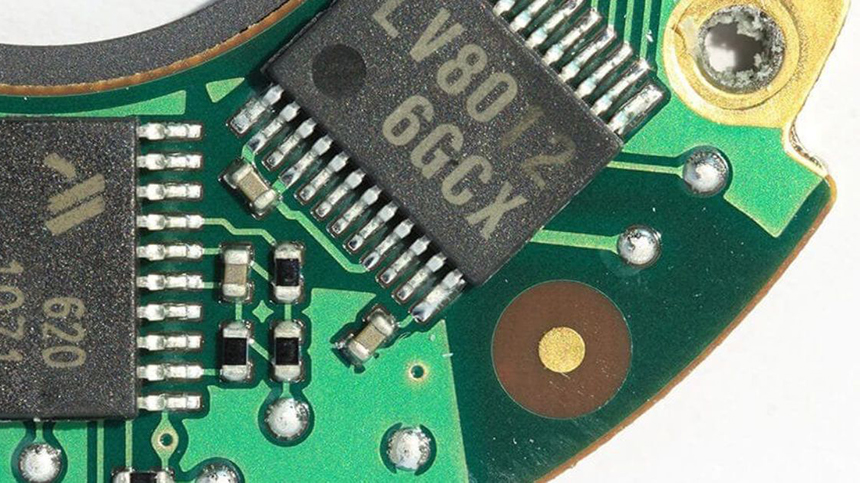
Introduction: The Role of Microvias in Modern PCB Assembly
Microvias are a critical component in high-density interconnect (HDI) PCBs, enabling miniaturization and enhanced performance in modern electronics. As devices shrink and speeds increase, understanding PCB microvia in PCBA process is essential for designers and PCB manufacturers. This guide explores microvia technology, its advantages over traditional vias, and best practices for reliability and cost efficiency.
What Are Microvias? (Definition & IPC Standards)
A microvia, as defined by IPC-2226, is a laser-drilled hole with:
· Aspect ratio of 1:1 (diameter = depth).
· Maximum depth of 0.25 mm (10 mils).
· Typically spans 1-2 layers (occasionally 3).
Microvia vs. Traditional Through-Hole Vias
Feature |
Microvia |
Through-Hole Via |
Aspect Ratio |
1:1 |
Up to 10:1 |
Drilling Method |
Laser |
Mechanical |
Plating Reliability |
High (uniform plating) |
Risk of barrel voids |
Applications |
HDI, smartphones, 5G |
Standard PCBs |
Why PCB Microvias?
· Enable finer pitch BGAs (e.g., 0.3 mm pitch).
· Reduce signal loss in high-frequency designs.
· Save up to 40% board space vs. through-hole vias.
PCB Microvia in PCBA Process: Key Manufacturing Steps
1. Laser Drilling (vs. Mechanical Drilling)
· Laser Types: CO₂ (for organic materials) / UV (for smaller holes).
· Advantages:
o No drill wander or smear.
o Supports via-in-pad and stacked microvias.
2. Sequential Lamination (Multi-Stage Process)
Microvias require multiple lamination cycles:
1. Drill & plate inner microvias.
2. Laminate new layers.
3. Repeat for stacked/staggered microvias.
Critical DFM Rule:
· Limit to ≤4 lamination cycles to avoid registration drift.
3. Plating & Filling (Ensuring Reliability)
· Electroless Copper + Electrolytic Plating: Ensures uniform barrel coverage.
· Epoxy Filling (for Buried Microvias): Prevents voids during thermal cycling.
Microvia Reliability Challenges & Solutions
Common Failure Modes
1. Barrel Cracking (Due to CTE mismatch between copper and FR-4).
2. Plating Voids (From poor solution flow in high-aspect-ratio vias).
3. Registration Errors (Caused by excessive lamination steps).
Best Practices for Robust Microvias
Stacked vs. Staggered Microvias:
Stacked: More compact but higher stress.
Staggered: Better reliability but uses more space.
Material Selection: Use low-CTE substrates (e.g., Megtron 6) to reduce thermal stress.
Cost-Benefit Analysis: When to Use Microvias?
Microvia Cost Drivers
Factor |
Cost Impact |
Laser Drilling |
+20–30% vs. mechanical |
Additional Lamination Steps |
+15–25% per cycle |
Epoxy Filling |
+10–15% |
When Are Microvias Worth It?
✅ HDI Designs: Smartphones, wearables, 5G mmWave.
✅ High-Speed PCBs: >10 Gbps signals (reduced stub effects).
❌ Avoid If: Budget-constrained & via density is low.
FAQ: PCB Microvia in PCBA Process
Q1: Can microvias replace all through-hole vias?
A: No—through-hole vias are still used for power/ground planes in hybrid designs.
Q2: How small can a microvia be?
A: Typically 50–100 µm diameter, but advanced lasers achieve ≤25 µm.
Q3: Do microvias affect impedance control?
A: Yes—proper anti-pad design is critical for high-speed signals.
Conclusion
Integrating PCB microvia in PCBA process requires balancing:
· Performance needs (HDI, high-speed).
· Reliability risks (thermal cycling, plating quality).
· Cost constraints (laser drilling, lamination steps).
Pro Tip: Collaborate early with your PCB manufacturer to validate microvia DFM rules.
References
1. IPC-2226 (HDI Design Standard).
2. "Microvia Reliability in HDI PCBs," Journal of Electronics Manufacturing, 2023.
3. Prismark Report on HDI Technology Trends (2024).
Industry Category