What Is PCB Board Material?
By:PCBBUY 08/28/2023 12:02
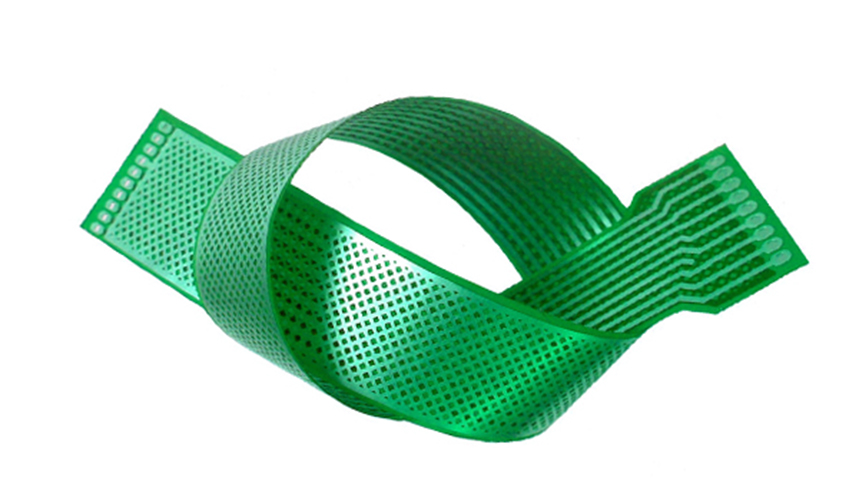
Introduction
Printed Circuit Board (PCB) materials form the foundation of all electronic devices, from smartphones to industrial equipment. The right PCB board material ensures optimal performance, reliability, and cost-efficiency. This guide explores the types of PCB materials, their properties, and how to choose the best one for your application.
What Is PCB Board Material?
PCB board material consists of two primary components:
1. Substrate (Base Material) – Provides mechanical support and insulation.
2. Conductive Layer (Copper Foil) – Forms the circuit traces for electrical connections.
The choice of PCB board material impacts thermal management, signal integrity, and durability.
Types of PCB Board Materials
Different applications require specific PCB board materials. Below are the most common types:
1. FR-4 (Flame Retardant-4)
· Composition: Fiberglass-reinforced epoxy laminate.
· Advantages:
o Cost-effective
o Good electrical insulation
o Flame-resistant
· Applications: Consumer electronics, industrial PCBs.
2. Polyimide (PI) – Flexible PCBs
· Composition: High-temperature-resistant polymer.
· Advantages:
o Bendable and lightweight
o Excellent thermal stability
· Applications: Wearable devices, aerospace, medical implants.
3. Metal Core PCBs (MCPCBs)
· Composition: Aluminum or copper base for heat dissipation.
· Advantages:
o Superior thermal conductivity
o Ideal for high-power circuits
· Applications: LED lighting, automotive systems.
4. High-Frequency Materials (Rogers, Taconic)
· Composition: PTFE (Teflon) or ceramic-filled laminates.
· Advantages:
o Low signal loss at high frequencies
o Stable dielectric constant
· Applications: 5G, radar, RF circuits.
5. Ceramic PCBs
· Composition: Alumina (Al₂O₃) or aluminum nitride (AlN).
· Advantages:
o Extreme thermal conductivity
o High mechanical strength
· Applications: Power electronics, military systems.
How to Choose the Right PCB Board Material?
Selecting the best PCB board material depends on several factors:
1. Electrical Requirements
· Dielectric Constant (Dk): Affects signal speed (critical for high-frequency PCBs).
· Dissipation Factor (Df): Determines signal loss (lower is better for RF applications).
2. Thermal Performance
· Glass Transition Temperature (Tg): Higher Tg materials (e.g., FR-4 High-Tg) resist heat deformation.
· Thermal Conductivity: Metal-core and ceramic PCBs dissipate heat efficiently.
3. Mechanical Strength & Flexibility
· Rigid PCBs: FR-4 for standard applications.
· Flexible PCBs: Polyimide for bendable circuits.
4. Cost vs. Performance
Material |
Cost |
Best For |
FR-4 |
Low |
Consumer electronics |
Polyimide |
Medium |
Wearables, medical |
Rogers |
High |
5G, RF applications |
Ceramic |
Very High |
Aerospace, power modules |
PCB Board Material Comparison Table
Property |
FR-4 |
Polyimide |
Metal Core |
High-Frequency |
Ceramic |
Thermal Conductivity |
Low |
Medium |
High |
Medium |
Very High |
Flexibility |
Rigid |
Flexible |
Rigid |
Rigid |
Rigid |
Cost |
$ |
$$ |
$$ |
$$$ |
$$$$ |
Best For |
General use |
Bendable circuits |
Heat dissipation |
RF/microwave |
Extreme environments |
Why PCB Board Material Selection Matters?
· Signal Integrity: Poor material choice causes signal loss in high-speed designs.
· Reliability: High-Tg and metal-core PCBs last longer in harsh conditions.
· Manufacturing Yield: Low-quality materials increase defects.
FAQs About PCB Board Materials
Q1: What is the most common PCB board material?
A: FR-4 is the most widely used due to its balance of cost and performance.
Q2: Which PCB material is best for high-frequency applications?
A: Rogers or Taconic materials offer the lowest signal loss.
Q3: Can I mix different PCB materials in one design?
A: Yes, rigid-flex PCBs combine FR-4 and polyimide for hybrid solutions.
Conclusion
Choosing the right PCB board material is critical for performance, durability, and cost-efficiency. Whether you need FR-4 for consumer electronics or ceramic for aerospace, understanding material properties ensures optimal design.
Industry Category